3 axis vs 5 axis CNC: The leap and challenge of CNC machining technology
CNC machining technology is an indispensable part of modern manufacturing. It achieves high-precision and high-efficiency parts production through computer-controlled machine tools.
In the development history of CNC machining, 3 axis vs 5 axis CNC technologies represent different technical levels and application scopes.
This article will deeply explore the principles, advantages, disadvantages and challenges of 3 axis vs 5 axis CNC technologies to help readers better understand the leap and future development direction of CNC machining technology.
1.3-axis CNC machining technology: basics and wide application
(1) Technical principle
3-axis CNC machining is the most common and simplest form of CNC machining. In this technology, the cutting tool moves along the X, Y, and Z axes to process the workpiece fixed on the worktable. The tool can move along multiple axes at the same time to achieve cutting on different surfaces of the workpiece. This technology is suitable for machining parts with basic geometric shapes, such as planes, slots, holes, etc.
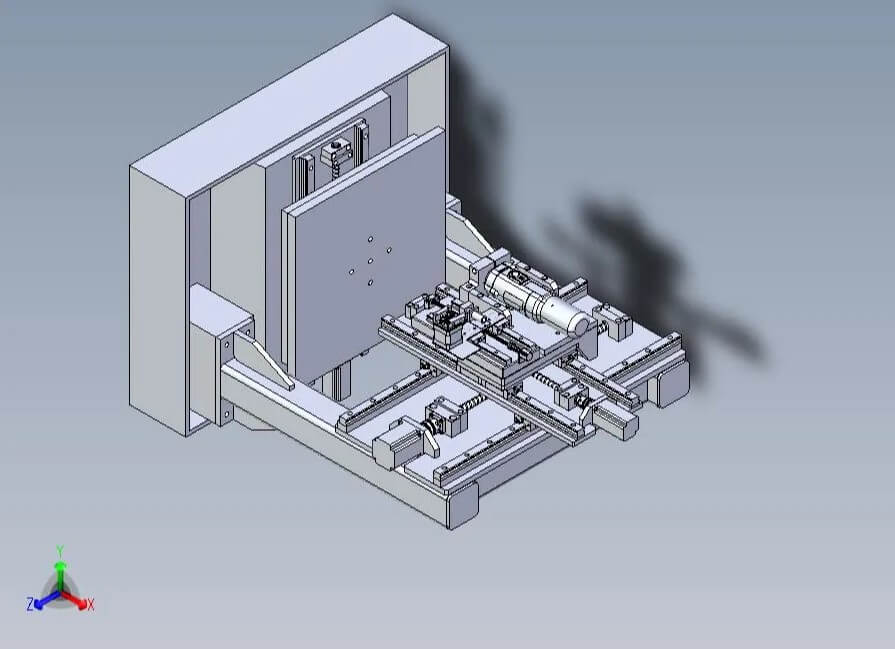
(2) Advantages
1) Low cost:
3-axis CNC machining machines and their programming are relatively simple, making their initial investment and operating costs low and suitable for use by small and medium-sized enterprises.
2) Versatility:
By replacing the tool, the 3-axis machine tool can perform a variety of operations such as drilling, milling, and turning, and has high versatility.
3) Efficient production:
For parts with simple geometric shapes, 3-axis machining can achieve rapid production and improve production efficiency.
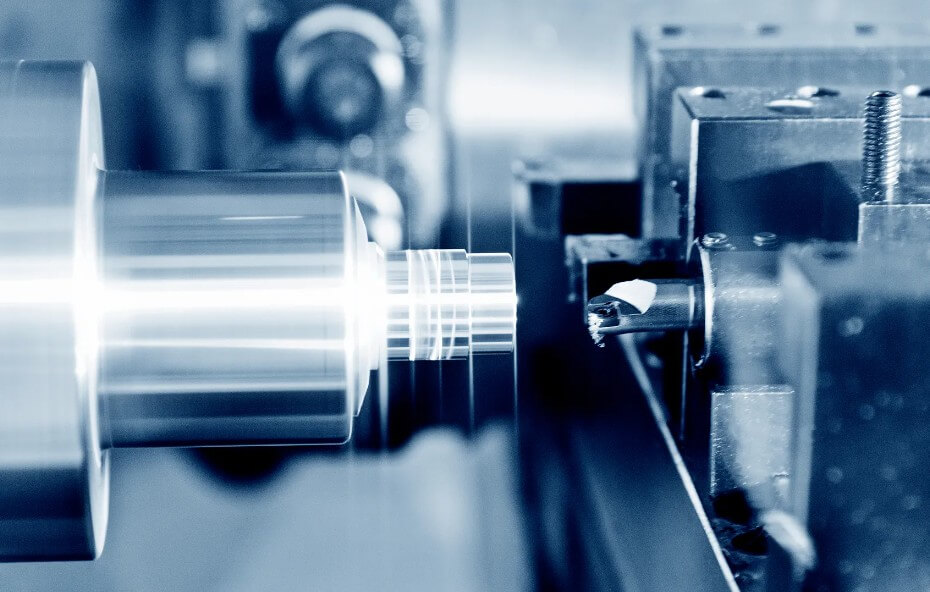
(3) Disadvantages
1) Design limitations:
Since the workpiece is fixed during the machining process, 3-axis CNC machining is difficult to process parts with complex geometric shapes or deep cavity features.
2) Multiple settings:
In order to machine different surfaces of the workpiece, multiple clamping and repositioning may be required, increasing production time and error risks.
3) Poor surface finish:
Longer tools are prone to vibration during machining, affecting surface finish.
(4) Application areas
3-axis CNC machining is widely used to manufacture parts of various basic geometric shapes, such as:
- 2D and 2.5D pattern engraving
- Slot milling and face milling
- Threaded holes and drillings aligned with the machine axis
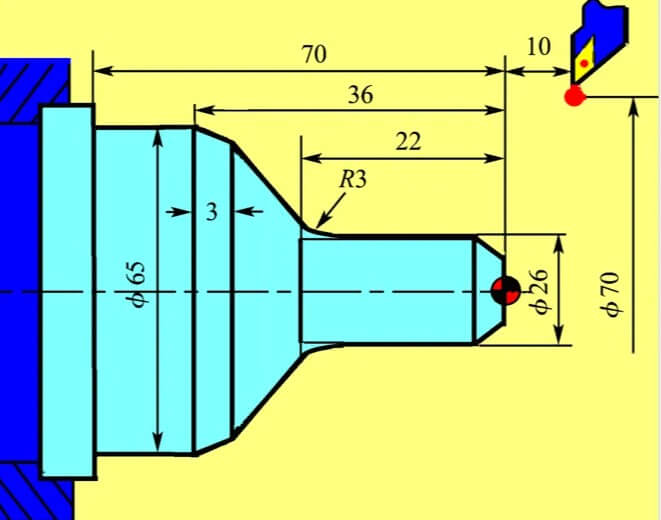
2.5-axis CNC machining technology: manufacturing of high-precision and complex shapes
(1) Technical principles
5-axis CNC machining is one of the most advanced and accurate CNC machining technologies. In addition to linear motion along the X, Y, and Z axes, 5-axis machine tools also have two rotation axes (A and B or B and C or A and C), allowing the workpiece to rotate in multiple planes. This multi-dimensional motion enables the machine tool to perform complex three-dimensional machining and achieve high-precision part production.
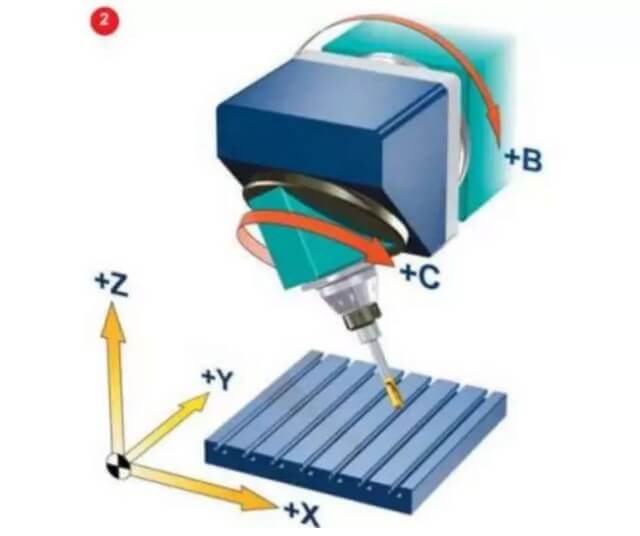
(2) Advantages
1) Complex part manufacturing:
5-axis CNC machining can handle a variety of complex geometries, such as curved surfaces, narrow cavities, and overhanging features, and is suitable for the aerospace, automotive, and energy industries.
2) High precision and efficiency:
Since multiple surfaces can be processed in one clamping, the number of repositioning and clamping times is reduced, and processing accuracy and efficiency are improved.
3) Shortened delivery time:
Without multiple settings, 5-axis machines can create complex shapes in a single machining process, significantly reducing delivery time.
4) High-quality surface finish:
Multi-axis motion allows the tool to get closer to the workpiece surface, achieving cleaner and more accurate cutting, thereby obtaining first-class surface finish.
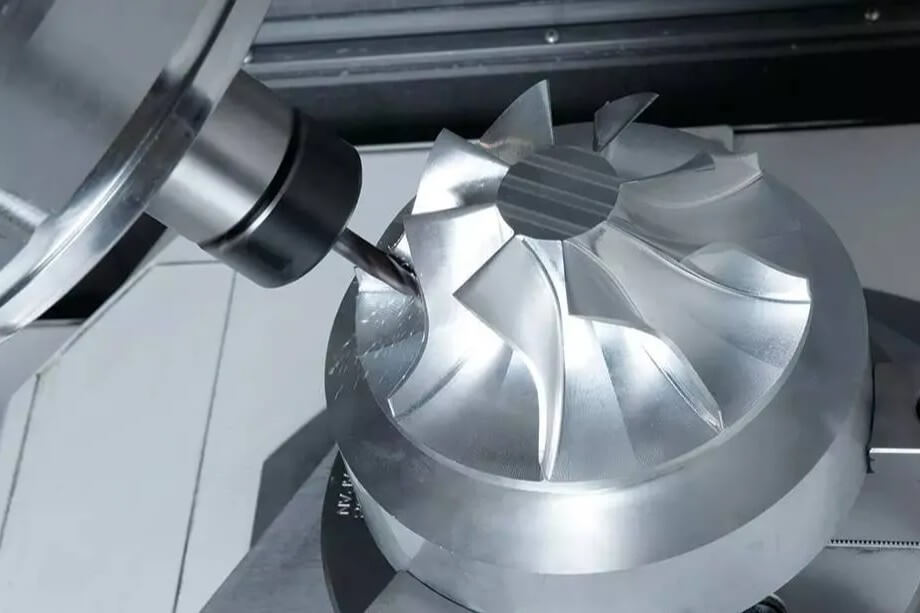
(3) Disadvantages
1) High cost:
The 5-axis CNC machining machine tools and their programming are complex, resulting in high initial investment and operating costs, and higher technical requirements for operators.
2) Complex programming:
Since it involves the movement of multiple axes, the programming of 5-axis machining is more difficult, requiring advanced CAD/CAM software and experienced technicians.
3) High requirements for CNC systems:
Five-axis machining requires the CNC system to have at least five-axis linkage control functions, and to have high computing speed and accuracy, which increases the complexity and development difficulty of the CNC system.
(4) Application areas
5-axis CNC machining is suitable for the manufacture of high-precision, complex-shaped parts, such as:
- Machining of complex shapes and inclined surfaces
- High-precision, low-tolerance applications
- Precision parts in the aerospace, automotive and energy industries
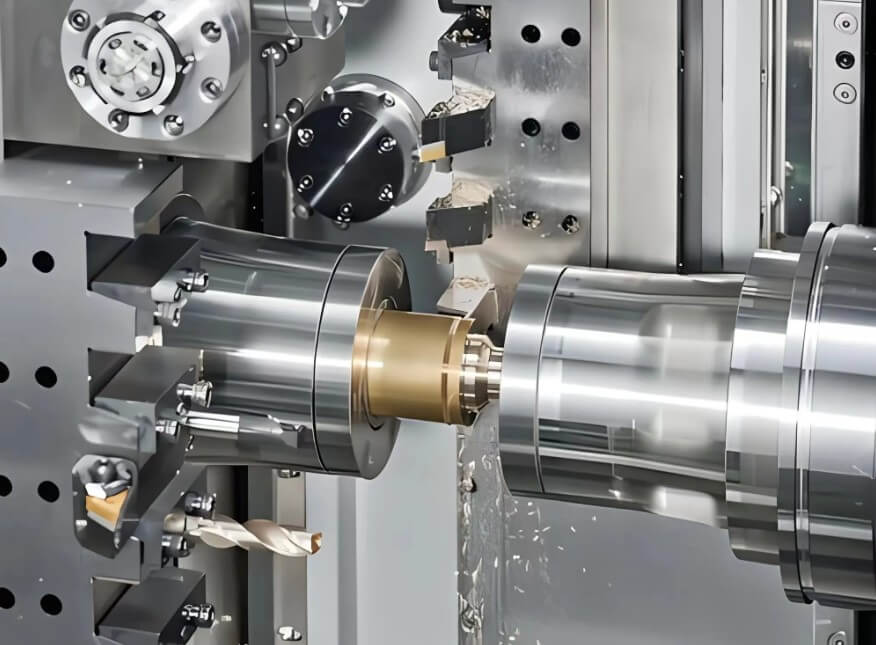
3.3 axis vs 5 axis CNC: Technological leaps and challenges
(1) Technological leap
The development of 3-axis to 5-axis CNC machining technology reflects a huge leap in CNC technology in terms of accuracy, efficiency and complexity. 5-axis CNC machining makes it possible to manufacture complex parts through multi-dimensional movement, meeting the needs of modern manufacturing for high-precision and high-quality parts.
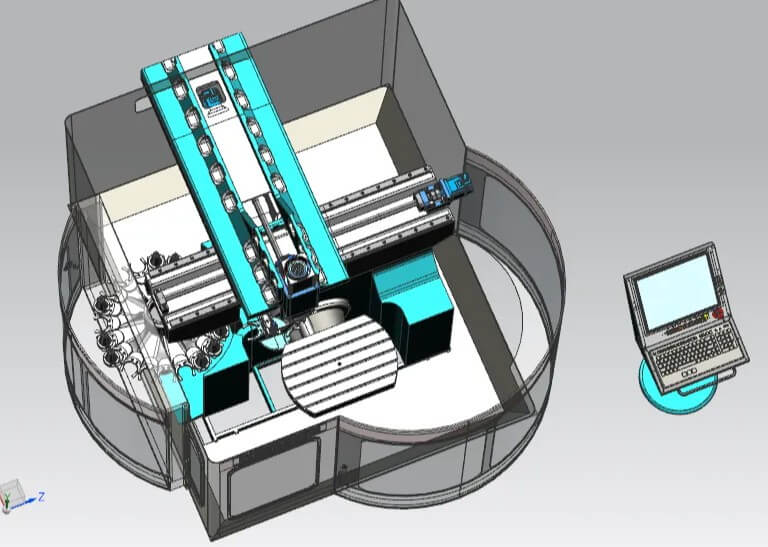
(2) Challenges
Although 5-axis CNC machining technology has significant advantages, its high cost, complex programming and high requirements for CNC systems also bring many challenges:
1) Cost pressure:
The high equipment and operating costs limit the popularity of 5-axis CNC machining technology in small and medium-sized enterprises.
2) Complexity of CNC system:
The realization and optimization of five-axis linkage control function requires advanced CNC system and powerful computing power, which puts higher requirements on the research and development of CNC system.
3) Programming difficulty:
Complex multi-axis motion requires advanced CAD/CAM software and rich programming experience, which increases the technical threshold.
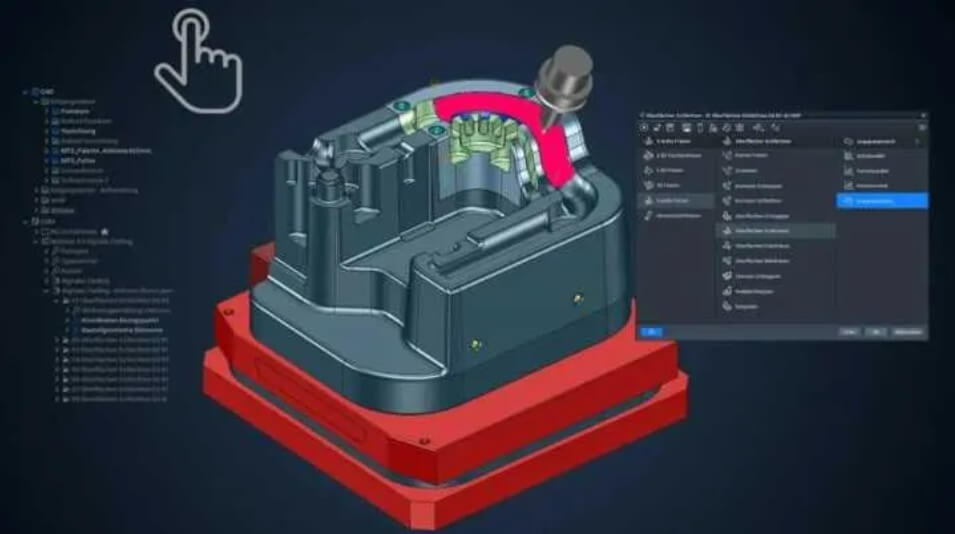
(3) Future development trend
With the continuous development of manufacturing industry, CNC machining technology will continue to develop in the direction of high precision, high efficiency, intelligence and low cost. In the future, 5-axis CNC machining technology is expected to be widely used in more industries. At the same time, new CNC technology and automation solutions will continue to emerge to meet the current challenges.
4.Combined application cases and advantages analysis of 3 axis vs 5 axis CNC machining:
(1) Combined processing cases of 3 axis vs 5 axis CNC machining
1) Aerospace parts manufacturing
Use 3-axis CNC machine tools for basic processing, such as rough milling and drilling.
Then use 5-axis CNC machine tools for complex surface finishing, such as impellers and blades.
2) Automobile parts manufacturing
In the processing of automobile engine cylinder blocks, first use a 3-axis CNC machining center for plane milling and hole processing to complete the basic shape and hole processing.
Then use a 5-axis CNC machining center to perform high-precision processing on complex surfaces and angles, such as the intake and exhaust ducts of the cylinder block, to ensure the performance and sealing of the engine.
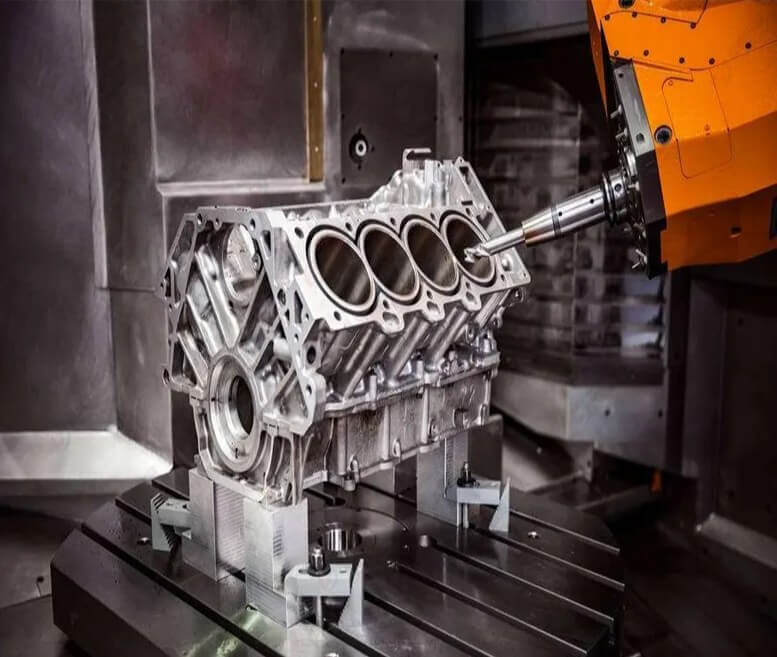
3) Medical device parts
Simple structures of parts such as connection parts are processed by 3-axis.
Key parts of parts such as complex curved surfaces of surgical knife handles are processed by 5-axis.
(2) Analysis of the advantages of 3 axis vs 5 axis CNC combined processing
1) Improve processing efficiency
3-axis machine tools handle simple processes, while 5-axis machine tools focus on complex processing, with clear division of labor and shortening the overall processing time.
2) Improve processing accuracy
5-axis machine tools can perform high-precision processing on complex parts through multi-axis linkage, and cooperate with 3-axis machine tools to ensure the quality of the final product.
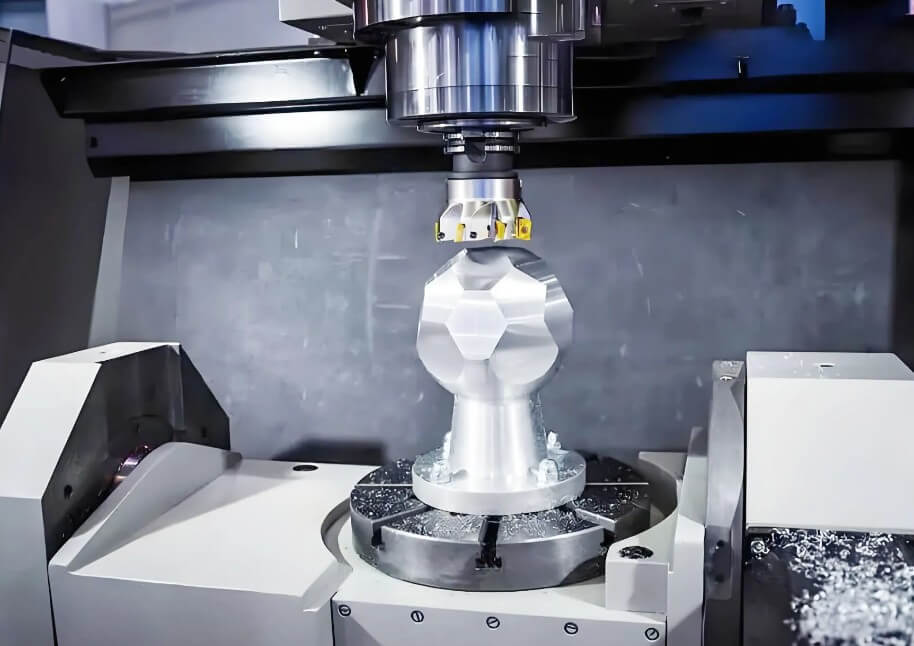
3) Reduce production costs
Reduce the number of part clamping times and tooling replacement time, and reduce labor and material costs.
4) Enhanced flexibility
3-axis machine tools are suitable for mass production, while 5-axis machine tools are good at processing small batches of complex parts. The combination of these two technologies can meet different production needs.
5.Conclusion
3 axis vs 5 axis CNC machining technologies play different roles in modern manufacturing. 3-axis CNC machining is widely used in the manufacturing of parts with basic geometric shapes due to its low cost and versatility, while 5-axis CNC machining shows unparalleled advantages in the manufacturing of parts with high precision and complex shapes.
Although 5-axis CNC machining technology faces some challenges, it has great development potential and represents the future direction of CNC machining technology. Through continuous innovation and technological progress, CNC machining technology will continue to promote the leapfrog development of the manufacturing industry.