3D printing vs injection molding: an in-depth comparative analysis
I.What is 3D printing?
3D printing, also known as additive manufacturing, is a revolutionary technology. It is completely different from traditional subtractive manufacturing (such as carving an object from a whole block of material). It builds objects based on digital designs by adding materials layer by layer until the final physical object is formed.
II.Types of 3D printing processes
(i) Fused deposition modeling (FDM)
This is the most widely used 3D printing technology. Its principle is to extrude heated filaments (usually plastic) through a nozzle and deposit them layer by layer to build an object. FDM has the advantages of being affordable and available in a variety of materials (such as ABS and PLA), and is often used for prototyping and functional parts manufacturing. However, its surface finish is relatively poor.
(ii) Stereolithography (SLA)
SLA uses a laser beam to solidify liquid resin layer by layer, producing highly detailed and smooth prints. It is the preferred technology for making high-precision prototypes, jewelry, and dental models. However, SLA resins are more expensive than FDM filaments and are usually toxic, so caution is required when operating them.
(iii) Selective laser sintering (SLS)
SLS uses a laser beam to sinter powder materials such as nylon or metal. The parts manufactured by this process are extremely durable and are suitable for functional parts that withstand high temperatures and high loads. However, SLS printers are generally more expensive than FDM and SLA machines.
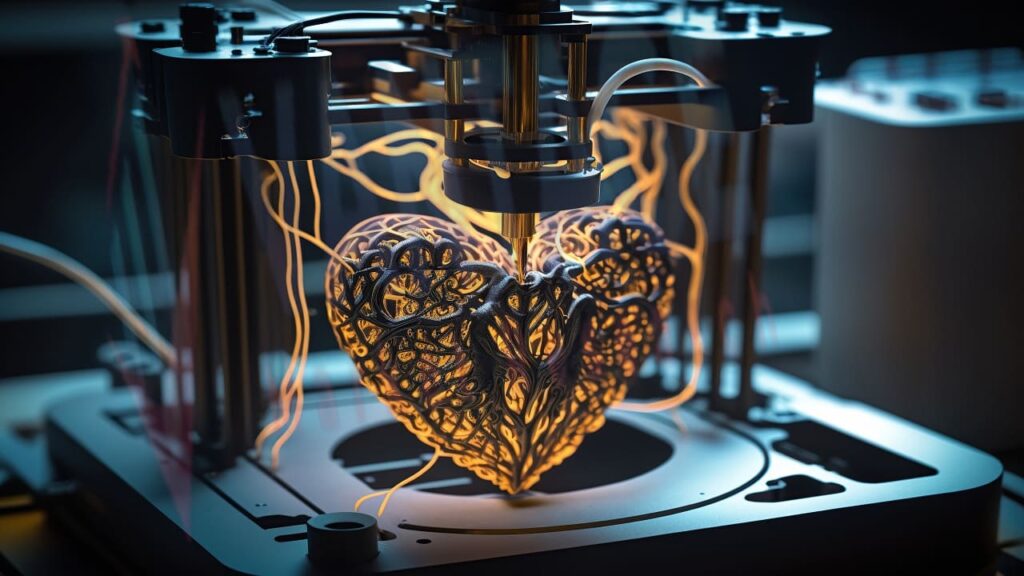
(iv)SLM/DMLS
SLM or DMLS uses a high-powered laser to carefully fuse metal powder particles layer by layer. This technology can produce high-strength and complex metal parts, and is suitable for applications with high strength-to-weight ratio requirements, complex internal features, and the use of multiple metals such as titanium, aluminum, and stainless steel.
(v)Multi-Jet Fusion (MJF)
MJF uses a unique inkjet method to print high-resolution nylon parts, using two nozzles, one for selective bonding of nylon powder particles and the other for refining the surface to present excellent details. This innovative process produces beautiful and powerful parts with a wide range of applications in prototyping.
(vi)PolyJet
PolyJet has high-precision inkjet technology that builds objects layer by layer by UV-curing liquid photopolymer resin. It can present a variety of material properties, including rigid, transparent, biocompatible and heat-resistant resins, and excels in manufacturing parts with high precision, complex details and smooth surfaces.
III.Definition of injection molding
Injection molding is a molding process used for mass production, which uses prefabricated molds to produce identical plastic parts. The mold serves as a template for the final product, shaping the molten plastic during its cooling and solidification process to ensure fast and stable production.
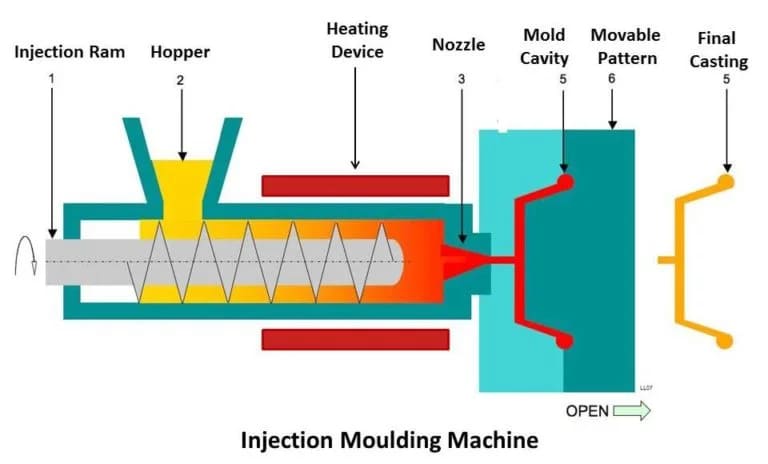
IV.Injection molding process steps
Mold making
This is the first critical step in the entire injection molding process. The mold is usually made of steel or aluminum and consists of two main parts: the cavity and the core. The cavity determines the external shape of the final product, while the core is used to create internal features such as holes.
Material preparation
Plastic resin pellets are fed into the hopper to prepare for subsequent melting and injection.
Melting and injection
The resin pellets are heated and melted in a barrel equipped with a screw, which simultaneously mixes and pressurizes the molten plastic. When ready, the screw pushes the plastic out through the nozzle at high pressure.
Mold filling
The molten plastic is injected into the clamped mold cavity through the main gate (main channel), runner (distribution channel), and finally through the gate (entry point into the cavity).
Cooling and solidification
The mold is equipped with cooling channels, which circulate coolant (water or oil) to quickly solidify the plastic into the desired shape.
Ejection
After cooling is completed, the mold opens and the ejector pushes the finished product out. The mold is then closed and the above cycle is repeated for continuous production.
V.Types of injection molding
Thermoplastic injection molding
This is the most common type of injection molding and is suitable for a variety of thermoplastics, such as polypropylene used for bottle caps and ABS used in Lego bricks. Thermoplastics can be reheated and reshaped, making them suitable for mass production.
Thermoset injection molding
This process uses thermosetting resins that undergo a permanent chemical reaction during the molding process. Since thermosetting resins cannot be remelted once molded, they are often used to manufacture parts that require high heat resistance or electrical insulation, such as engine parts and electrical housings.
VI.3D Printing vs Injection Molding: Material Selection Comparison
(I) Material Types
3D Printing: A wider range of materials, covering not only plastics (such as ABS, PLA, nylon), but also metals (such as titanium, aluminum), ceramics, and even biomaterials.
Injection Molding: Mainly focuses on thermoplastics because they can be melted and reshaped during processing, and the selection of thermosets is relatively limited.
(II) Material Compatibility
3D Printing: Compatibility varies depending on the specific printing process. For example, the FDM process is compatible with common plastics such as ABS and PLA, while the SLA process requires the use of special resins.
Injection Molding: The threshold for introducing new materials is high, and the mold needs to be specially designed based on the thermal properties and flow properties of the selected plastic, which makes the trial of new materials costly and time-consuming.
(III) Customization Options
3D Printing: Digital designs can be easily modified to print parts with unique functions, gradients, or embedded electronic devices, making it an ideal choice for prototypes and small batch production.
Injection molding: The degree of customization is limited. The mold determines the final part shape. Changes require major modifications or even re-molding. It is not suitable for one-off or dynamically changing designs.
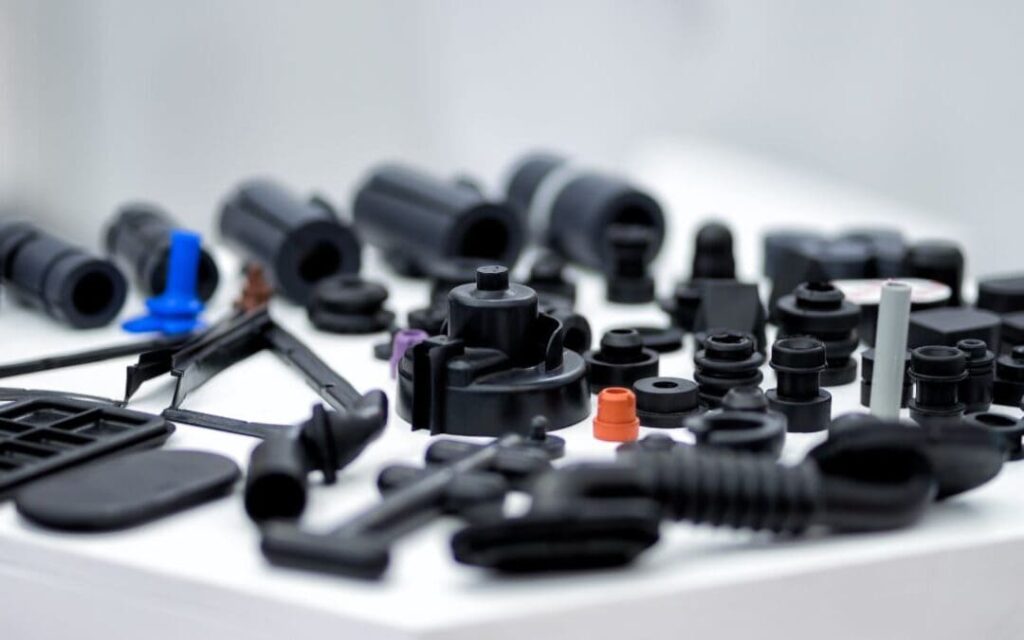
VII. 3D printing vs injection molding: Product attribute comparison
(i) Mechanical properties
Mechanical strength
3D printing: Strength varies depending on the printing process, material and filling density. Due to the layer-by-layer structure, it is usually more fragile than injection molded parts.
Injection molding: A uniform and dense material structure is formed through high pressure and high temperature. It has high mechanical strength and is suitable for high-load or high-stress applications.
Rigidity
3D printing: Similar to strength, stiffness is affected by many factors. Some materials (such as nylon) have a certain stiffness, but are generally more flexible than injection molded parts.
Injection molding: Due to its denser material structure, injection molding can produce parts with higher stiffness, which is critical for parts that need to maintain shape stability under pressure.
Durability
3D printing: Durability varies depending on the material and printing process. Although some materials (such as metals) have good durability themselves, 3D printed parts may be more prone to wear and tear depending on the specific application.
Injection molding: The material structure is dense and there are more high-performance thermoplastics available. The parts produced are usually more durable and suitable for manufacturing durable products.
(ii) Dimensional accuracy
3D printing: Accuracy varies depending on the printer and printing process. FDM printers are limited by filament width and layer thickness, while SLA and SLS have higher accuracy. .
Injection molding: Injection molding is able to provide excellent dimensional accuracy due to the high-precision characteristics of the mold. The replication accuracy of parts produced by injection molding can always be maintained within a tight tolerance range.
(iii) Complexity
3D printing: 3D printing is well suited for manufacturing parts with complex geometries. The layer-by-layer construction method enables complex designs with internal channels, overhangs, and even internal moving parts.
Injection molding: Although injection molding is also capable of handling complex shapes, it has certain limitations. Some designs with undercuts or very fine features may be difficult to achieve due to mold design and demolding considerations.
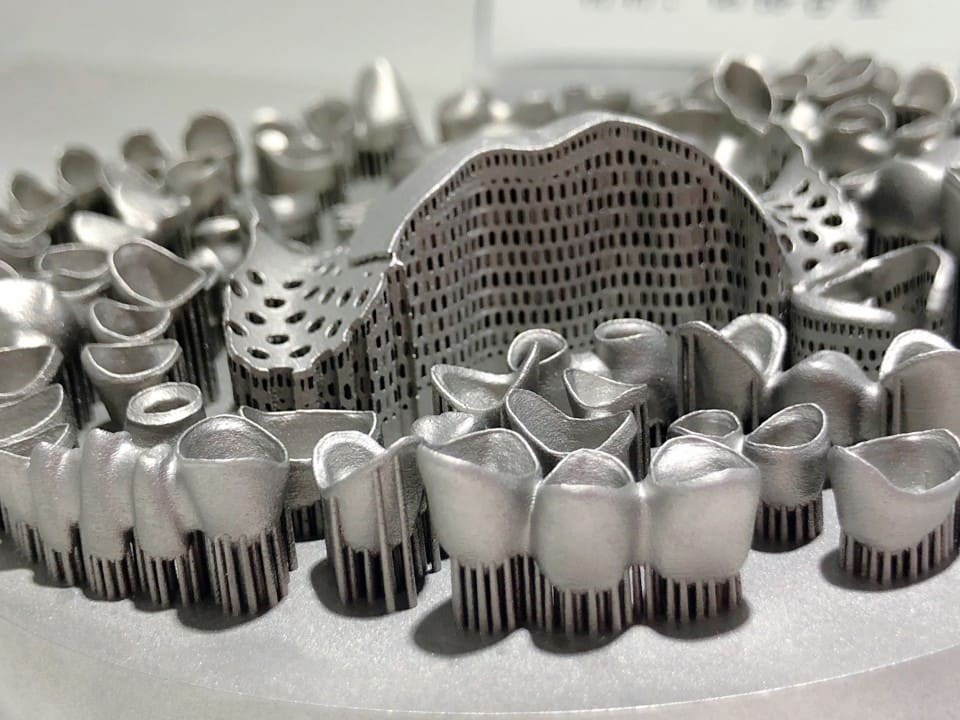
VIII.3D printing vs injection molding: cost analysis comparison
(i) Initial setup cost
3D printing: relatively low, mainly including printer and software costs.
Injection molding: very high, involving mold design and processing costs.
(ii) Production volume cost
3D printing: less cost-effective for small batch production (from the perspective of time and materials).
Injection molding: suitable for large-scale production, cost-effective.
(iii) Material cost
3D printing: material (filament/resin) cost may be higher.
Injection molding: uses bulk plastic particles, which is cheaper.
(iv) Labor cost
3D printing: generally low, mostly automatic or semi-automatic printing.
Injection molding: may involve more setup, operation and quality control links.
(v) Waste and efficiency
3D printing: will produce support structures and waste from failed prints.
Injection molding: can minimize waste, and the remaining plastic can be recycled.
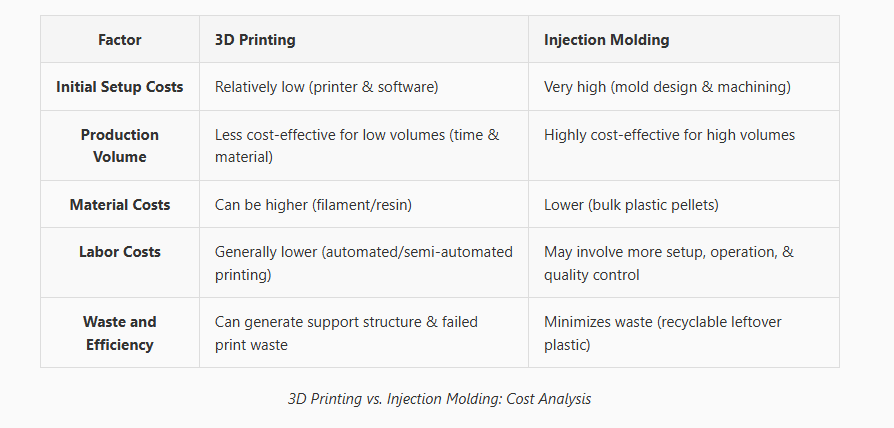
IX.3D printing vs injection molding: speed analysis and comparison
(i) Small batch production (1-100 parts)
3D printing: usually faster. While print times for individual parts will vary depending on part size and complexity, overall 3D printing offers faster turnaround times when producing in smaller batches.
Injection Molding: Not ideal when producing small batches. The high upfront cost of mold making makes injection molding uneconomical in this situation, and the time it takes to make the mold may exceed the time required to produce some of the parts.
(ii) Medium batch production (100-10,000 pieces)
3D printing: still a viable option. Throughput can be increased by printing multiple parts simultaneously or using multiple printers. However, for complex parts or higher volume production, injection molding may be more competitive.
Injection Molding: Once the mold is made, injection molding is extremely fast and can produce a part in seconds, which can significantly reduce the overall time for medium-volume production.
(iii) Mass production (10,000 + parts)
3D printing: Not suitable for mass production due to slow printing speed and high cost per part.
Injection Molding: Injection molding is the fastest and most cost-effective way to produce large quantities of identical parts when you have a mold. Cycle times (the time it takes to make a part) can be as short as a few seconds, enabling the rapid production of large quantities of parts.
X.3D printing vs injection molding: Comparison of Applications
(i) Prototyping and Rapid Iteration
Ideal choice: 3D printing. It has a fast design-to-print workflow that facilitates rapid iteration.
(ii) Small-batch production
Ideal choice: 3D printing. Suitable for complex or customized parts, but the cost per part and the time required to print in large quantities need to be considered.
(iii) Large-scale production
Ideal choice: Injection molding. It is the fastest and most cost-effective method for large numbers of identical parts.
(iv) Functional parts with specific requirements
Ideal choice: 3D printing. Ideal for parts with unique functions, complex geometries, embedded electronic devices, and diverse materials (metals, biomaterials).
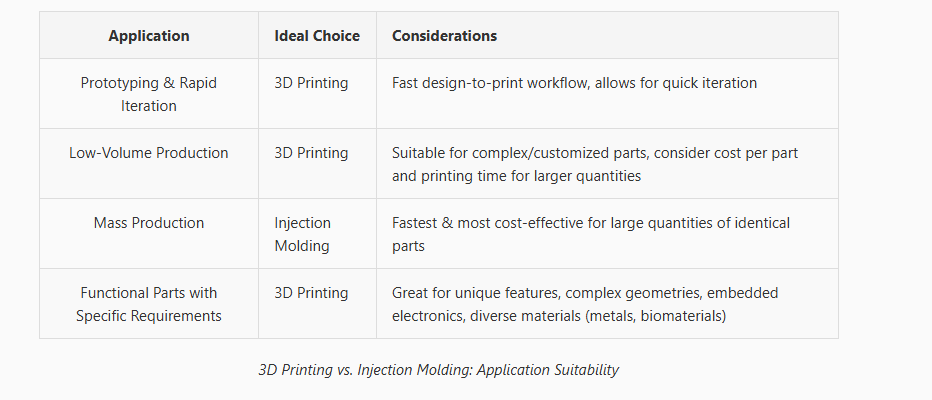
In conclusion
3D printing vs injection molding each have their own advantages in making plastic parts. 3D printing offers significant advantages in prototyping, customization and handling complex geometries, while injection molding dominates series production due to its speed and efficiency. Manufacturers need to choose the appropriate manufacturing process based on specific production needs, cost budget, product characteristics and other factors.
1 Comment