Common types of anodized aluminum processes
Anodized aluminum is a versatile material that is used in a variety of industries. The aluminum anodizing process involves forming a protective oxide layer on the surface of the metal, which enhances its durability and corrosion resistance. There are several types of aluminum anodizing processes, each with its own unique properties and applications.
1.Sulfuric Acid Anodizing
The process involves immersing the aluminum in a sulfuric acid bath and passing an electric current through it. The result is a thick, porous oxide layer that can be dyed to obtain different colors. Sulfuric acid anodizing is widely used in architectural applications such as window frames and curtain walls, as well as decorative and ornamental parts in the automotive industry.
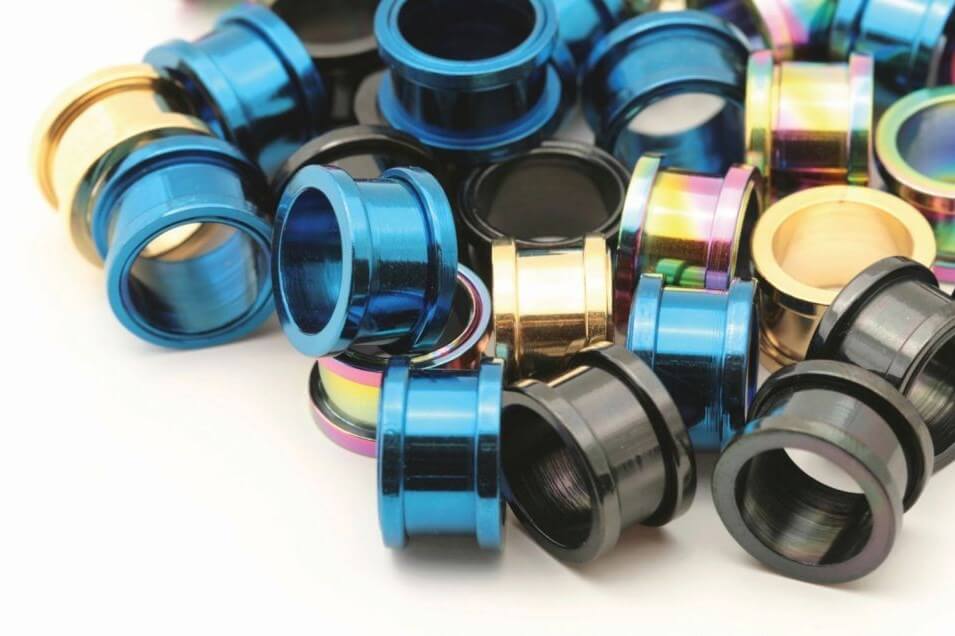
2.Hard Anodizing
The process is similar to sulfuric acid anodizing, but uses higher voltage and lower temperatures, resulting in a thicker, harder oxide layer. Hard anodized aluminum is known for its excellent wear resistance and is often used in applications that require high durability, such as aerospace components, cookware, and firearms.
3.Chromic Acid Anodizing
It uses a chromic acid solution instead of sulfuric acid to produce a thin, dense oxide layer, and chromic acid anodizing is often used in applications such as electrical connectors and electronic components that require a thin, uniform coating. It can also be used as a pre-treatment for bonding, as it provides an excellent bonding surface.
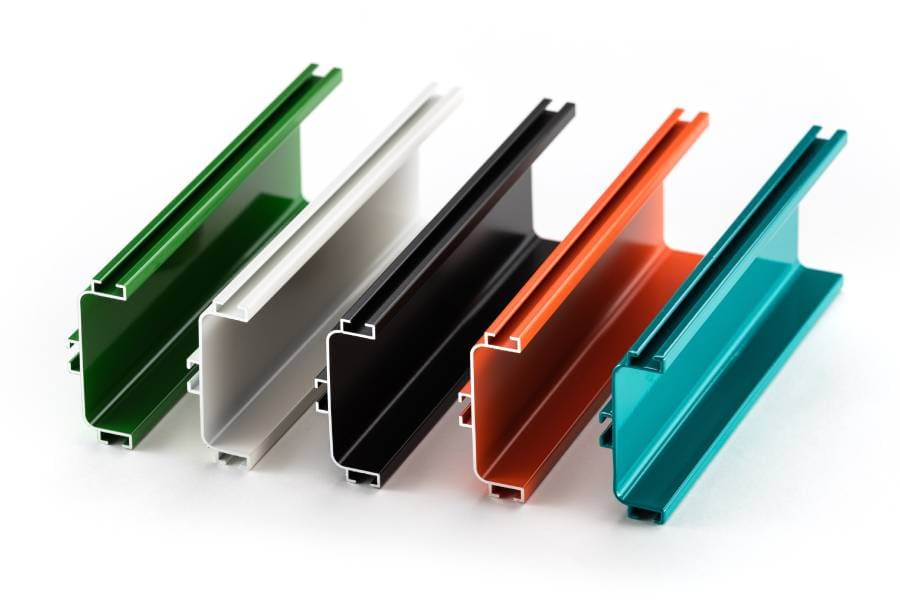
4.Other Anodized Aluminum Types
In addition to these traditional aluminum anodizing processes, there are specialized processes that offer unique properties and applications. For example, hard anodizing is a type of hard anodizing that uses a special electrolyte and lower temperatures to create a thicker, harder oxide layer. This process is often used in applications that require extreme wear resistance, such as pistons, cylinders, and hydraulic components.
Another specialized process is called two-step anodizing. This process first anodizes the aluminum in sulfuric acid and then treats it with hot water or steam to seal the pores in the oxide layer. Two-step anodizing produces a dense and corrosion-resistant coating that is often used in architectural applications, such as building facades and signage.
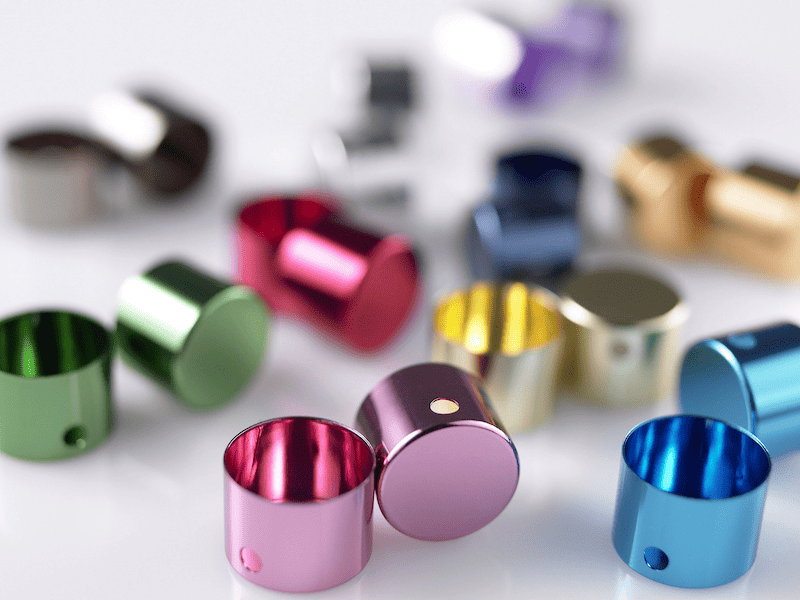
In summary, anodized aluminum is a versatile material that can be used in a variety of applications. Different types of anodized aluminum processes offer unique properties and capabilities that can be tailored to specific requirements.
Whether it is sulfuric acid anodizing for architectural applications, hard anodizing for durability, or a specialized process for extreme wear resistance, anodized aluminum offers durable and beautiful solutions for a variety of industries.