5-axis machining:What types of parts are suitable?
Over the past few years, CNC machining technology has evolved from simple machines to more complex ones. 5-axis CNC machining is one of the most advanced machining processes available today. It utilizes subtractive machining techniques, which offer endless possibilities for part manufacturing. This technology uses cutting tools that work on the 5 axes of the machining table to cut the workpiece into the desired shape and size.
5-axis machining improves accuracy, efficiency, and reliability. The increase in the number of axes also allows 5-axis milling machines to outperform similar machines. In addition, the process allows for full automation and management using computer numerical control (CNC). As a result, many reliable precision machine shops rely on this technology to provide accurate CNC machining services.
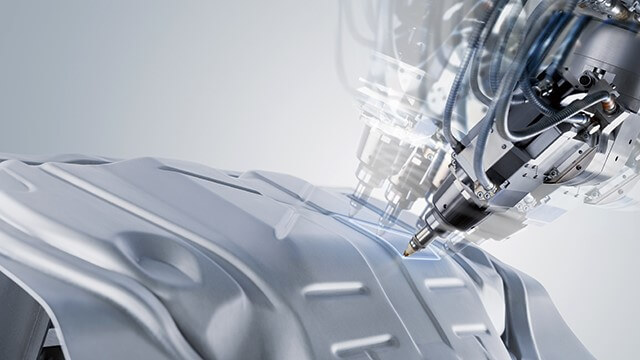
1.Advantages of 5-axis Machining
The ability to move the tool and workpiece to 5 sides simultaneously brings many advantages to many industries, and it enables the manufacture of complex parts in a cost-effective manner. The following are the main advantages of this manufacturing process:
1) Simple setup operations
5-axis CNC machines can machine up to 5 surfaces simultaneously. With traditional 3-axis machining, you may need to set up multiple setups for parts with multiple surfaces. But 5-axis technology can complete the machining of contoured parts and other parts with multiple faces in one structure. This allows you to manufacture parts with complex geometries with fewer setups.
2) Machining Complex Shapes (GD&T Tagging)
The additional rotation in this machining process helps achieve more complex designs and geometries. The machine can seamlessly machine arcs and angles that were previously only possible using multiple special fixtures. The 5-axis CNC milling process can rotate the part to achieve the desired geometry in a single operation without the need for complex fixtures.
In addition, this technology combines perfectly with GD&T tagging to generate datum features in a single operation. 5-axis precision CNC milling is also suitable for CNC machining applications that require surface profile tolerances on complex contour surfaces.
3) High Accuracy and Repeatability
Compared to CNC machining, manual machining requires additional setups, which can cause machinists to lose precise alignment during the manufacturing process. However, the minimal setup required for 5-axis CNC milling reduces the possibility of errors and increases the accuracy required to achieve excellent quality.
Today, different types of 5-axis machines eliminate the need to reposition the workpiece at different angles during machining. As a result, you can ensure improved machining tolerances. In addition, some machine configurations allow for the use of shorter cutting tools. This can extend tool life and ensure repeatability.
4) High Cutting Speeds
5-axis machining ensures that the cutting tool is tangential to the cutting surface. This arrangement allows the tool to remove more material per revolution. As a result, it reduces machining cycle times and reduces overall machining costs.
5) Smooth Surfaces
The additional axis in this technology ensures that the workpiece is properly positioned, closer to the cutting tool. As a result, you can use shorter cutting tools to create the desired shape. These shorter tools can cut at extremely high speeds with little to no vibration.
The less vibration, the less likely it is that “chatter” marks will appear on the finished product. The vertical machining process also improves spindle utilization when machining inclined surfaces. As a result, you can achieve better surface finishes with this technology and reduce the cost and time associated with post-processing.
6) Save Cycle Time and Money
Due to the high speed advantages of the process, 5-axis machining of a part can usually be completed in a single operation. This saves time and money with only one setup. In addition, shorter tool life and longer tool life saves money and time because there is no need to constantly change tools.
In addition, the 5-axis milling process can be automated, reducing manual operations and labor requirements. This reduces the labor costs involved in the process. Therefore, 5-axis CNC machining is a cost-effective solution that accelerates your product to market.
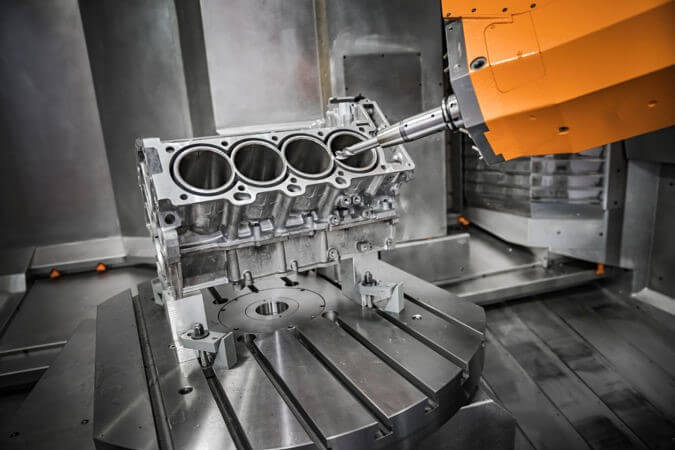
2.Disadvantages of 5-axis machining
Despite the many advantages of 5-axis CNC technology, its use is not suitable for some applications. Some disadvantages of the process include:
1) High initial cost
The cost of purchasing a 5-axis CNC machine and its basic software is high. It costs much more than what is required for a 3-axis machining center. Similarly, the maintenance requirements of this machine are more challenging than traditional machines. This aspect also directly increases the cost of machining 5-axis parts.
2) Difficult programming
The two additional rotational movements and the spatial trajectory of their movements are relatively abstract and complex. For example, processing free-form surfaces requires multiple coordinate transformations, complex spatial geometry operations, and consideration of the coordination of the movements of each axis. All of this is to avoid collisions and interferences and ensure the correct amount of interpolation movement. Therefore, it is much more difficult to program to achieve the required machining accuracy and surface quality.
3) Higher requirements for operators
5-axis CNC milling is an advanced technology that involves advanced programming, machine setup, and operation. Therefore, the process requires skilled operators. This usually means increased labor costs.
4) Make the most of 5-axis machining
It is common to underutilize the 5-axis function. Some operators do not understand the full capabilities of the machine. Others may not have the programming knowledge for cutting-edge operations.