Explore efficient 5 axis workholding solutions
As a key technology in modern manufacturing, five-axis machining technology has greatly improved machining efficiency and precision. 5 axis workholding is an important part of this technology, which directly affects the stability, precision and production efficiency of the machining process. This article will analyze 5 axis workholding in detail from multiple aspects.
1.Overview of five-axis machining technology
Five-axis machining technology is a high-precision and high-efficiency machining method that can complete multi-faceted machining of complex workpieces in one clamping. It is widely used in high-precision manufacturing fields such as aviation, aerospace, and automobiles.
This technology realizes the machining of complex angles and shapes of workpieces through the control of five axes, greatly improving machining efficiency and precision. Five-axis machining technology can not only handle complex geometric shapes, but also complete multiple processes in one clamping, reducing the number of clamping and adjustment of workpieces, thereby reducing machining errors and production time.
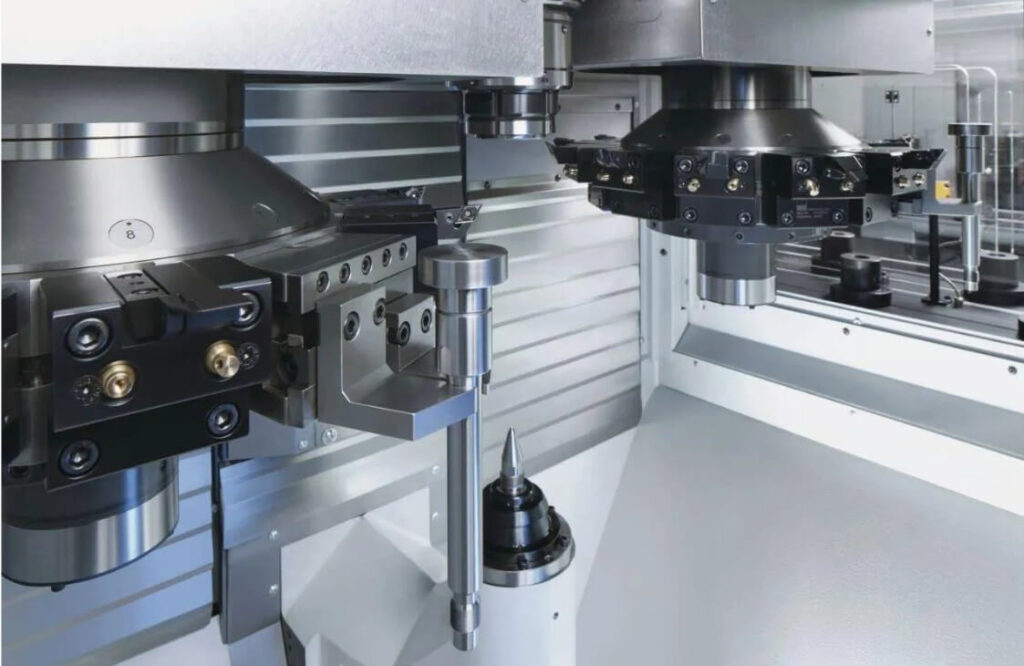
2.Overview of 5 axis workholding
5 axis workholding refers to the use of specific fixtures or devices to firmly fix the workpiece on the workbench of the five-axis machining machine tool so that its position can be kept stable during machining. Five-axis machining centers have five motion axes (X, Y, Z, A, B or C), which can realize multi-angle and multi-directional machining of workpieces. Therefore, the 5 axis workholding system must have a high degree of stability and adaptability to meet the clamping needs of workpieces of different shapes, sizes and materials.
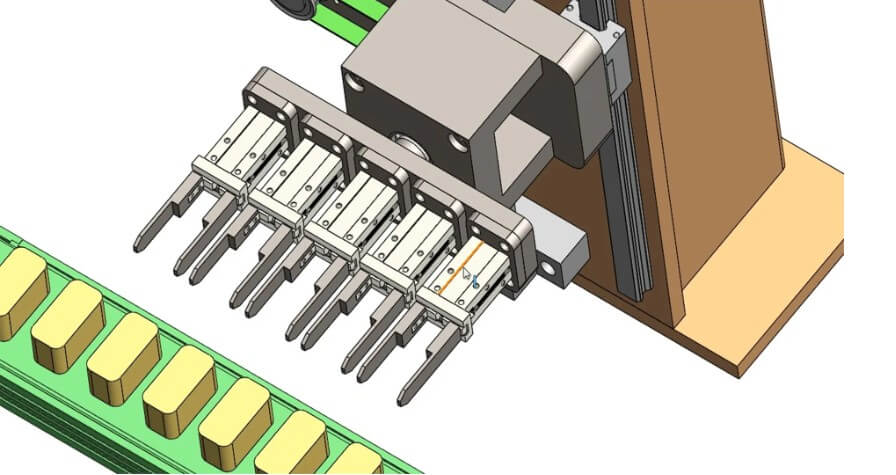
3.The importance of 5 axis workholding
(1) Improving machining accuracy:
Stable clamping can ensure that the workpiece does not move or vibrate during the machining process, thereby ensuring machining accuracy. Five-axis machining usually involves parts with complex surfaces and high precision requirements. Good clamping effect is the basis for ensuring that these requirements are met.
(2) Improving production efficiency:
A fast and reliable clamping system can shorten the clamping time of the workpiece and improve the utilization rate of the machine tool. In an automated production line, an efficient 5 axis workholding system is the key to achieving continuous and efficient production.
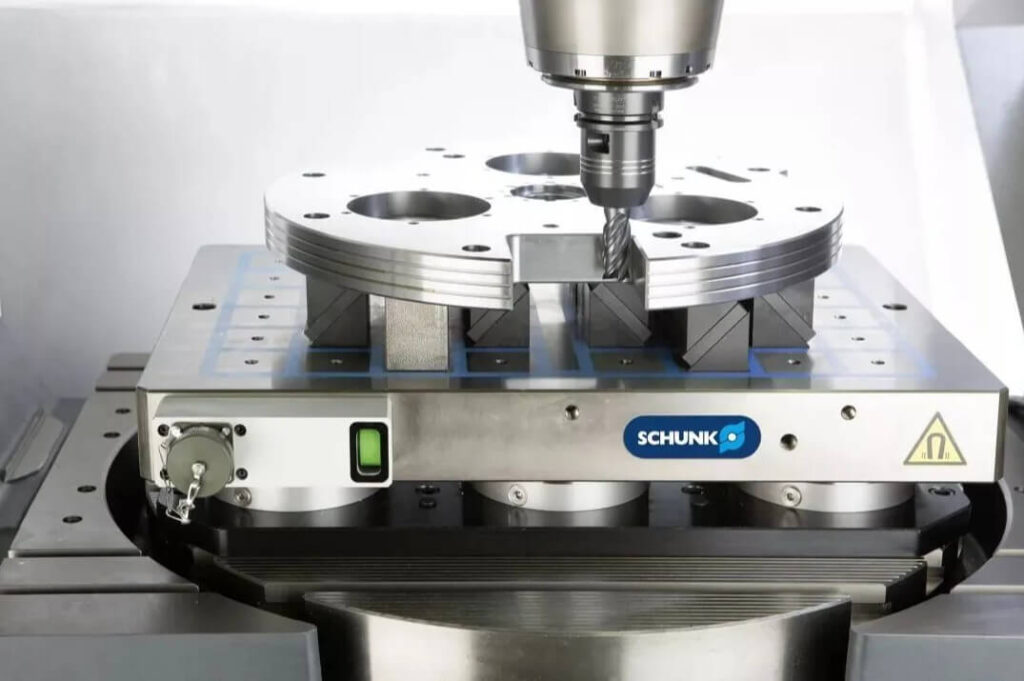
(3) Expanding the machining range:
The 5 axis workholding system can adapt to workpieces of various shapes and sizes, giving the five-axis machining center a wider range of machining capabilities. Whether it is a small precision part or a large complex structural part, it can be processed by a suitable clamping system.
4.Common 5 axis workholding methods
(1) Mechanical clamping:
1) Vise clamping:
Applicable to workpieces of regular shapes, such as plates, bars, etc. The vise clamping structure is simple and easy to operate, but the clamping force is limited and is not suitable for high-precision processing.
2) Chuck clamping:
Commonly used for clamping cylindrical workpieces. Chuck clamping has a large clamping force and high precision, but its application range is relatively narrow.
3) Special fixture:
The fixture designed for specific workpieces can achieve efficient and precise clamping. The cost of special fixtures is high, but it can meet special processing needs.
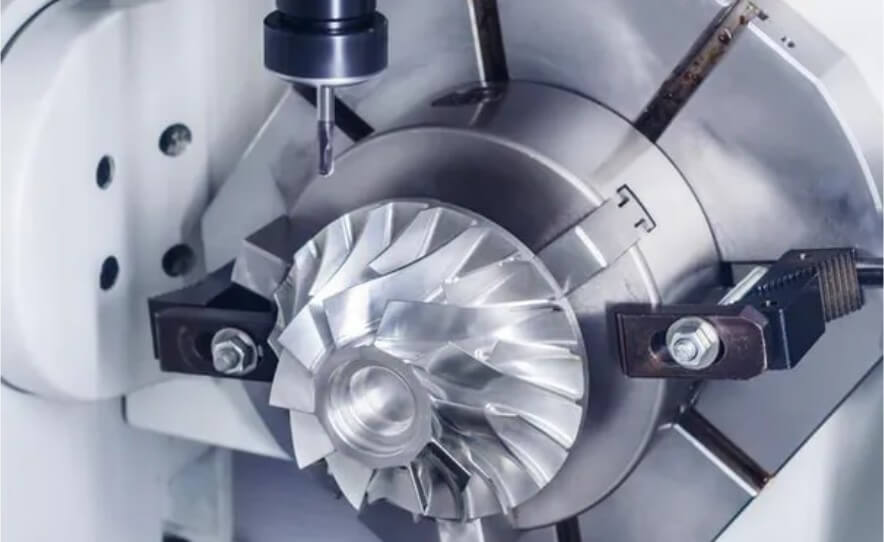
(2) Vacuum adsorption clamping:
Vacuum adsorption clamping uses vacuum negative pressure to firmly adsorb the workpiece on the fixture. This clamping method is suitable for thin plates, thin-walled parts and irregularly shaped workpieces.
Vacuum adsorption clamping has the advantages of uniform clamping force and no damage, but the stability of the vacuum system needs to be paid attention to during the processing.
(3) Magnetic clamping:
Magnetic clamping uses electromagnetic force to adsorb the workpiece on the fixture. Magnetic clamping has the advantages of large clamping force and easy operation, and is suitable for workpieces made of magnetic materials. However, magnetic clamping is not applicable to workpieces made of non-magnetic materials or that need to process non-magnetic surfaces.
5.Key technologies for 5 axis workholding
(1) Clamping force control:
Reasonable clamping force is the key to ensuring stable clamping of the workpiece. Excessive clamping force will cause deformation or damage to the workpiece, while too little clamping force may cause the workpiece to shift during the processing. Therefore, it is necessary to accurately control the clamping force according to factors such as the material, shape, size and processing requirements of the workpiece.
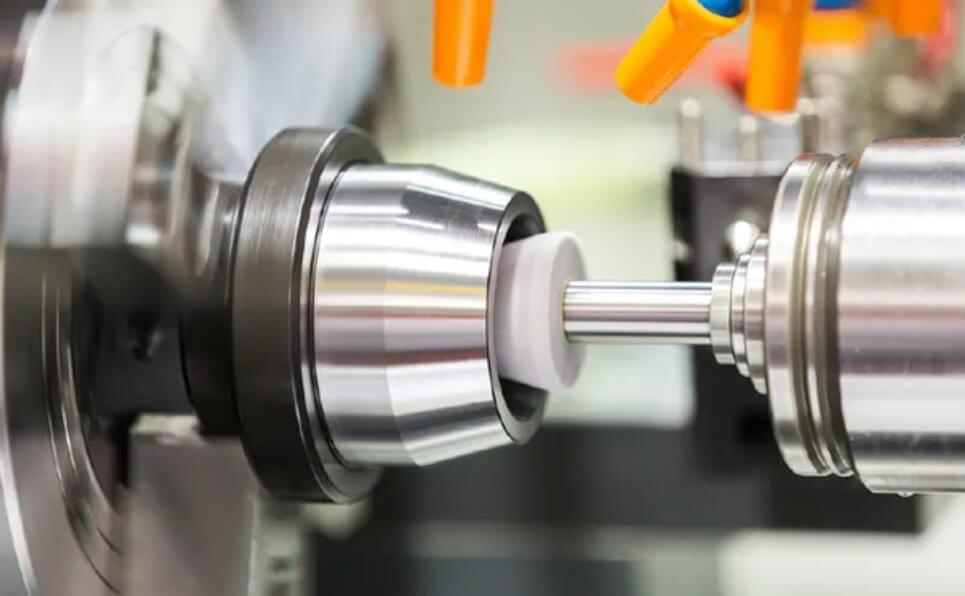
(2) Positioning accuracy:
High-precision positioning is the prerequisite for ensuring processing accuracy. The 5 axis workholding system must have a high-precision positioning function to ensure that the workpiece can be accurately positioned at the predetermined position during the clamping process. This usually requires precise fixture design and manufacturing, as well as advanced positioning technology.
(3) Adaptability:
Five-axis machining machines need to process workpieces of various shapes and sizes, so the clamping system must be highly adaptable. This can be achieved by designing modular, adjustable fixtures to meet the clamping requirements of different workpieces.
6.Analysis of causes and solutions for deformation and vibration in 5 axis workholding
In five-axis machining, deformation and vibration of workpiece clamping are important factors affecting machining accuracy and efficiency. The following is a detailed analysis of its causes and solutions:
(1) Cause analysis
1) Uneven clamping force:
Uneven distribution of clamping force can cause deformation of the workpiece during machining.
2) Workpiece material characteristics:
Workpieces of different materials deform to different degrees when subjected to external forces, especially thin-walled parts or soft materials.
3) Improper selection of cutting parameters:
Excessive cutting force or unreasonable cutting speed and feed rate can easily cause vibration.
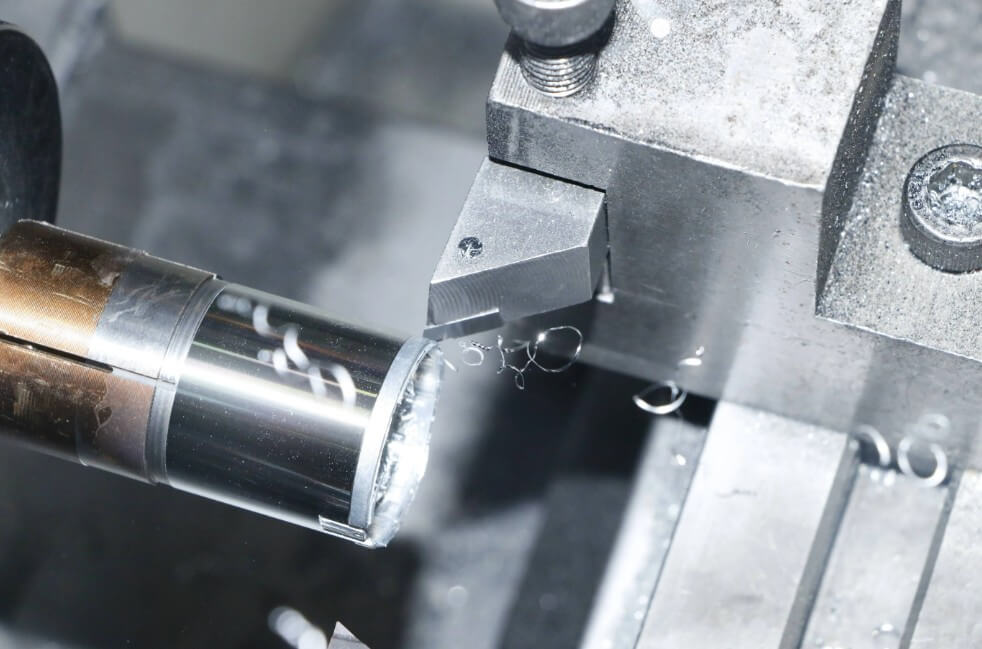
4) Insufficient rigidity of machine tools and fixtures:
The structural rigidity of machine tools or fixtures is insufficient and cannot effectively resist cutting forces, resulting in vibration.
5) Tool wear:
Tool wear will change the distribution of cutting forces, thereby causing vibration.
(2) Solutions
1) Optimize clamping methods:
Use special fixtures or customized fixtures to ensure uniform distribution of clamping forces and reduce deformation. Use multi-point clamping or vacuum adsorption to improve stability.
2) Select appropriate cutting parameters:
According to the material and hardness of the workpiece, reasonably select cutting speed, feed rate and cutting depth to reduce vibration caused by cutting forces.
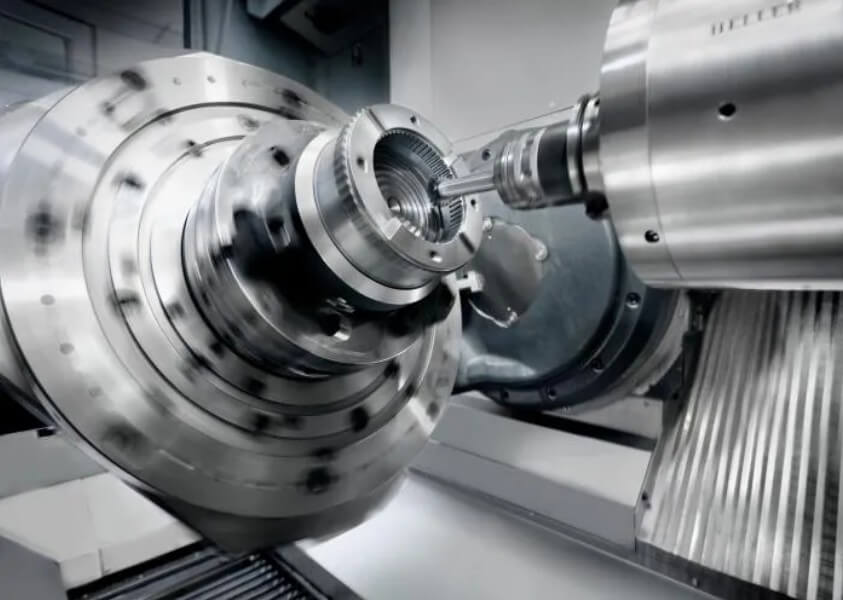
3) Improve the rigidity of machine tools and fixtures:
Regularly maintain and service machine tools, use high-rigidity fixtures and accessories, and improve the vibration resistance of the overall system.
4) Use vibration-damping tools and devices:
Use tools with vibration-damping functions or install vibration dampers to effectively absorb and reduce vibration.
5) Real-time monitoring and adjustment:
Use the online monitoring system to detect the vibration during the processing in real time, and adjust the cutting parameters or clamping methods in time according to the feedback data.
7.Conclusion
In short, exploring efficient 5 axis workholding solutions is the key to improving the quality and efficiency of five-axis processing. By adopting precise workpiece positioning and optimized clamping design, combined with specific application scenarios and needs, clamping solutions suitable for different workpieces can be developed.