Benefits of Machined Parts
Machined parts are everywhere, and for good reason: CNC machining works on a wide variety of metals and plastics, and machined parts can be made quickly, affordably, and without any tooling.
1.What are machined parts?
What are machined parts? A machined part is a part that is made by a subtractive cutting machine, such as a CNC mill, CNC lathe, CNC grinder, CNC EDM, or even a manual mill and lathe. Machined parts are widely used for rapid prototyping and mass production.
In manufacturing, machined parts may be contrasted with molded parts, cast parts, forged parts, extruded parts, and 3D printed parts, all of which are made using different technologies. That being said, “machined part” may describe a component that is partially made using one of these other methods but has been machined to its final finish. (For example, a cast metal part with machined features.) If a machined part is made using a digital machining center, it may also be called a CNC machined part or CNC part.
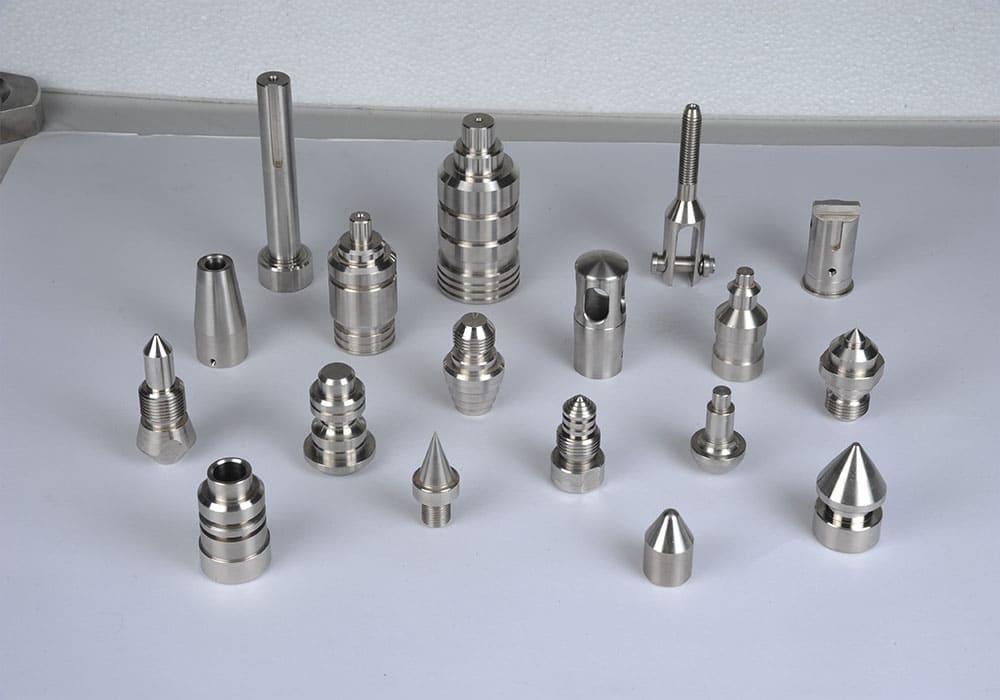
2.Advantages of Machined Parts
①No Minimum Order Quantity
One of the main advantages of machined parts is that there is no minimum order quantity required to purchase them. For molded parts, metal molds need to be built—a process that takes a long time and often costs tens of thousands of dollars. Machined parts, however, are cut directly from the blank workpiece, which makes it cost-effective to order very small batches or even one-off parts.
Of course, requiring a large number of (plastic) parts may mean that molding is a better choice. But machining is almost unique in providing high-quality parts without minimum order quantities, making it suitable for smaller companies, small batch production and prototyping.
②Viable Prototype Solutions
Some companies choose to order injection molded prototypes, but this is usually only affordable for large companies. The cost of molds makes prototyping cost-prohibitive. Machined parts are suitable for use as prototypes and are affordable because they can be manufactured in one-offs. Machining is also much faster than molding, which means that R&D departments can quickly iterate multiple versions of a part and then subject it to any testing or evaluation required before going into production.
The material versatility of machining also means that companies can order machined parts in several different metal alloys or composite plastics to see which material performs best under test conditions.
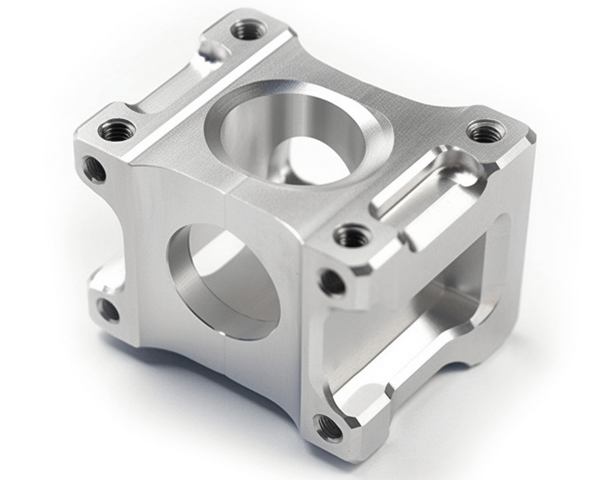
③Design Freedom
Machinery parts can come in a wide variety of shapes and sizes. That’s because CNC machining isn’t limited to extreme molding designs like thin walls and tapers; machined parts can be thick and strong, but their features can also be fine and detailed. While machined parts have some limitations in areas like internal sections and deep channels, machining is still one of the manufacturing processes with the most geometric flexibility.
On the other hand, molded parts must have thin walls and often meet more stringent design criteria. 3D printing is often seen as one of the best manufacturing technologies in terms of design freedom, but even so, it has limitations, such as avoiding overhangs. (And more complex, bulky designs may require extensive support structures that must be removed in expensive post-processing steps.)
④Quality
Machinery parts can be manufactured to a very high standard. Perhaps more importantly, the customer can specify the tolerances that the machinist needs to meet. This means the machinist or machine operator can spend more time on tight tolerance parts and individual features.
While injection molds can also be manufactured to tight tolerances, it’s unlikely that every individual mold will be manufactured to such a high standard. Molds produced near the end of a mold’s life may lack the definition of earlier units. Machining also avoids molding-related surface quality issues, such as flash at flow lines, jets, and parting lines.
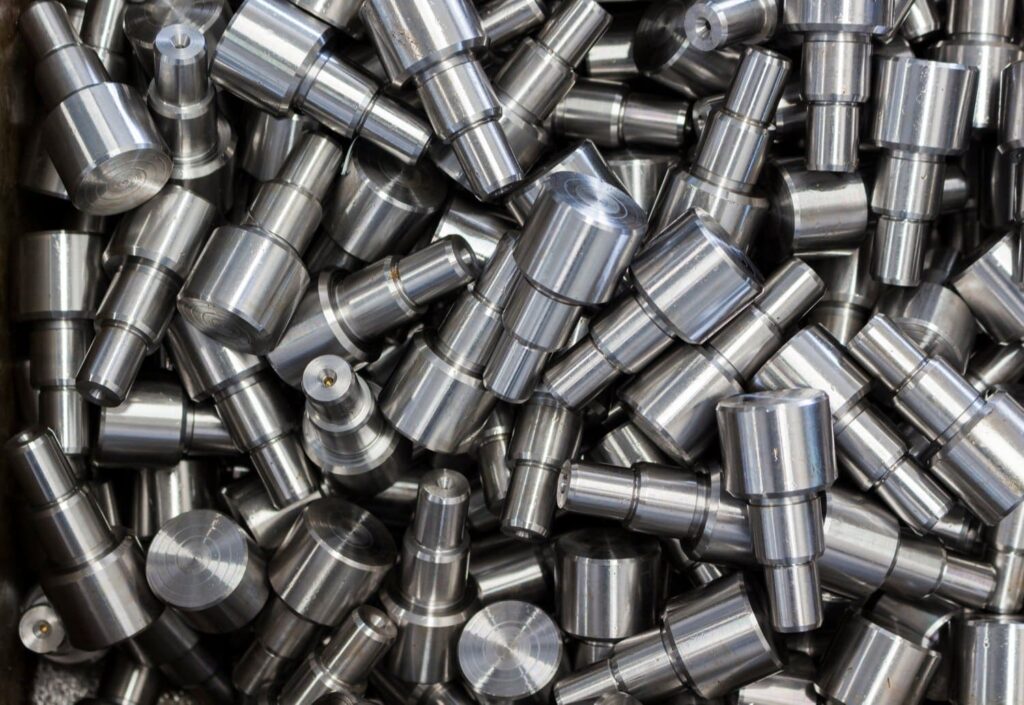
⑤Lead Time
Machine-machined parts can be made faster than parts made by other production processes such as molding.
This is partly due to the lack of labor-intensive tooling, but the manufacturing process itself is also very efficient: some of the faster machining centers equipped with linear guides can process at speeds of around 4,000 cm per minute (although parts should not actually be machined at such speeds). The one-step nature of machining combined with the speed of CNC machining centers makes machined parts among the fastest to manufacture (in small batches), which reduces lead time, shortens time to market, and enables practical rapid prototyping.
⑥Modifications
Because CNC machined parts are made from a digital CAD file, changes can be made to that digital design before manufacturing. This is very useful during R&D and prototyping, as engineers may want to make minor adjustments to a machined part or create multiple versions. It also reduces the potential for waste, as there is less chance of producing a defective part.
Machined parts have a significant advantage over molded parts: tools are not easily changed, and if a last-minute modification is required, it would be a huge waste of money to create a new mold. Does this mean that injection molding has less of an advantage? Of course not. Injection molding is one of the most efficient ways to manufacture high-volume parts. It all comes down to whether your part is suitable for the process. Learn more about injection molding.