The Importance of CNC Machining in Medical Parts Manufacturing
The medical industry is constantly innovating to find ways to improve the quality of life and treatment outcomes for patients. One such technology is computer numerical control (CNC) machining, which has become a revolutionary tool in the field of medical hardware manufacturing. In this rapidly evolving field, CNC machines not only offer high levels of precision and accuracy, but are also capable of processing a wide range of materials and complex geometries. In this article, we’ll explore seven key applications in the field of medical CNC machining that have revolutionized the manufacturing and customization of medical hardware, from hip replacements to dental tools. Let’s take a deeper look at these exciting application areas.
1.Hip Replacements and Knee Implants
Like other machined medical hardware, human implants such as knee implants and hip replacements require a high level of precision and accuracy. Minor errors in the manufacturing process can have a significant impact on the life and health of a patient.
Swiss CNC machines facilitate the precise manufacture of patient-specific parts while achieving tolerances as small as 4 μm. CNC machining centers receive requests from orthopedic surgeons, create CAD models, and recreate body parts using reverse engineering and CNC technology.
The medical industry requires these implants to be made from biocompatible materials such as PEEK and titanium. These materials are difficult to machine – they generate excessive heat during machining, and the use of coolants is often prohibited due to concerns about contamination. CNC machines help address this challenge as they are compatible with a wide range of materials.
2.Surgical Instrument Production
Complex surgical procedures require high-precision, specialized tools. These instruments range from simple scalpels and scissors to complex robotic arms for minimally invasive surgery. These tools must be manufactured with high precision. CNC machining plays a vital role in producing the surgical tools required for a variety of medical procedures.
CNC machines can achieve complex geometries and tight tolerances, making them ideal for producing complex surgical instrument designs. For example, robotic-assisted surgical instruments can be machined using CNC technology to ensure the highest precision, allowing surgeons to perform complex surgeries with greater accuracy and fewer complications.
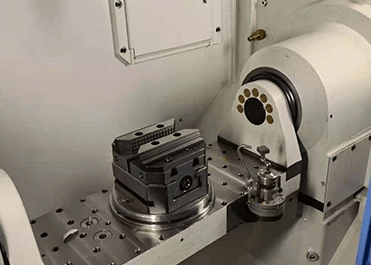
3.Electronic Medical Devices
Many medical devices such as MRI scanners, heart rate monitors, and X-ray machines are equipped with thousands of CNC-machined electronic components. Examples include switches, buttons, and levers, as well as electronic housings and casings.
Unlike implants and surgical tools, these medical devices do not need to be biocompatible because they do not come into direct contact with the patient’s internal systems. However, the manufacturing of these parts is still overseen and controlled by multiple regulatory agencies.
Failure to adhere to the standards set by these regulatory agencies can result in a machine shop incurring large fines (and sometimes even jail time). In some cases, the medical professionals involved have had their medical licenses revoked. Therefore, it is important to choose a medical device manufacturer wisely.
4.Custom Prosthetics
Personalization is becoming increasingly important in healthcare, and nowhere is this more evident than in the field of prosthetics. Patients demand a prosthetic that fits their body perfectly, and custom manufacturing can help you address this problem, as traditional mass production techniques often fail to meet the needs of patients.
CNC machining is changing the field of prosthetics by producing custom devices based on each patient’s unique physiological characteristics. CNC machines use 3D scanning and CAD modeling to create prosthetics with intricate details and high-precision dimensions, ensuring optimal function and comfort for patients. Therefore, with CNC technology, prosthetics can be produced with high precision to ensure comfort and full functionality.
5.Small Orthotics
Orthopedic devices, such as plates, screws, and rods, are widely used in the medical field to repair or replace damaged bones and joints. Given the critical role these devices play in patient rehabilitation, they must be manufactured with the highest precision and quality.
CNC machining plays a vital role in the production of these orthopedic devices. CNC technology is well suited to the production of these devices because it is able to machine complex geometries with high precision. Additionally, CNC machining can process a variety of biocompatible materials, including titanium and stainless steel, which are commonly used in orthopedic devices.
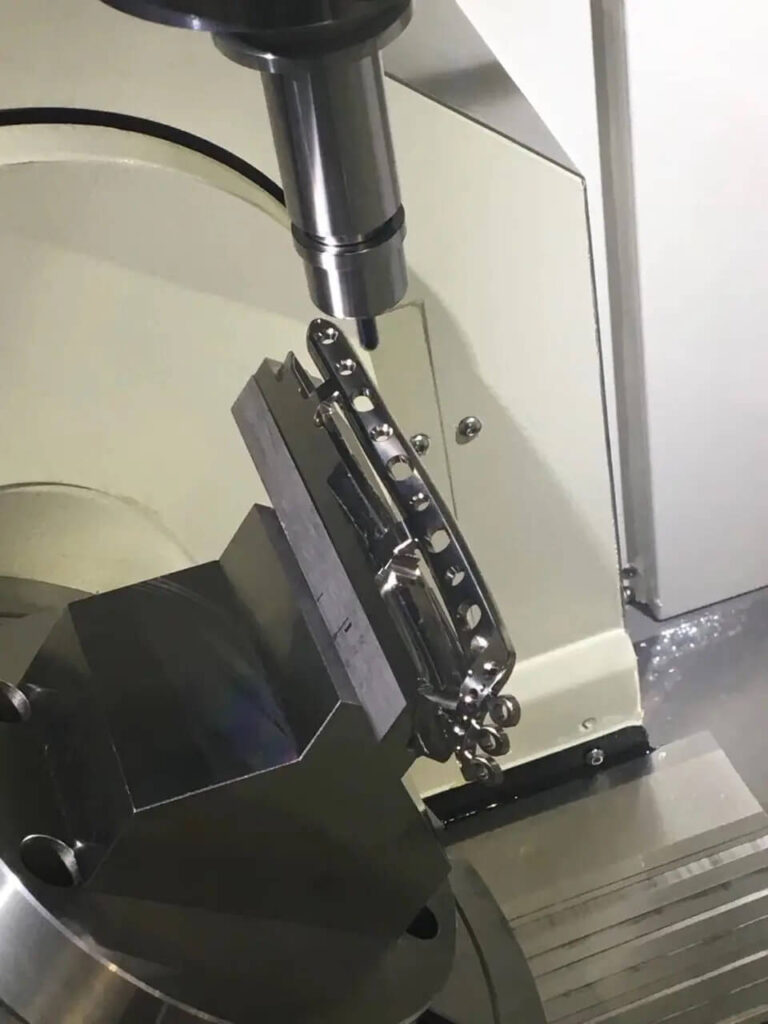
6.Medical Device Prototyping
Before mass producing any medical device, it is critical to create prototypes for testing and validation, and Richconn’s CNC machining provides a fast and cost-effective solution for producing medical device prototypes, whether it is medical CNC turning services or CNC milling services, we can meet your needs. With the ability to quickly generate multiple iterations of a design, engineers can test and improve the device to ensure it is safe, effective, and meets regulatory requirements.
This capability is critical in the fast-moving field of medical device development, where being able to quickly bring new products to market can provide a significant competitive advantage. CNC machining can also produce low-volume prototypes, allowing manufacturers to minimize waste and save on material costs during the development process.
7.Dental Tools and Implants
CNC machining is essential to providing high-quality dental care through the creation of custom dental tools and implant abutments. Dentists around the world rely on advanced CNC technology for precision treatment. The technology is ideal for manufacturing durable instruments such as drills, scalers, probes, and forceps, which are essential for a variety of procedures.
The production of these instruments requires exceptional durability to withstand sterilization while ensuring patient safety. CNC manufacturing provides repeatability and strict quality control, guaranteeing that each tool meets exacting standards.
Dental implants provide a long-term solution for missing teeth and require precise customization using precision CNC machining. These implants are created from digital scans, ensuring an accurate and personalized fit for each patient. CNC machining has revolutionized the manufacturing of dental restorations and improved treatment outcomes. By effectively utilizing materials such as titanium and zirconium oxide, CNC technology enables precise modifications with exceptional efficiency and effectiveness.