We Care Your
Electrogalvanizing Solution
Proactively coordinate quality quality vectors vis-a-vis supply chains
quickly engage client-centric comprehensive services.
Our qualifications:
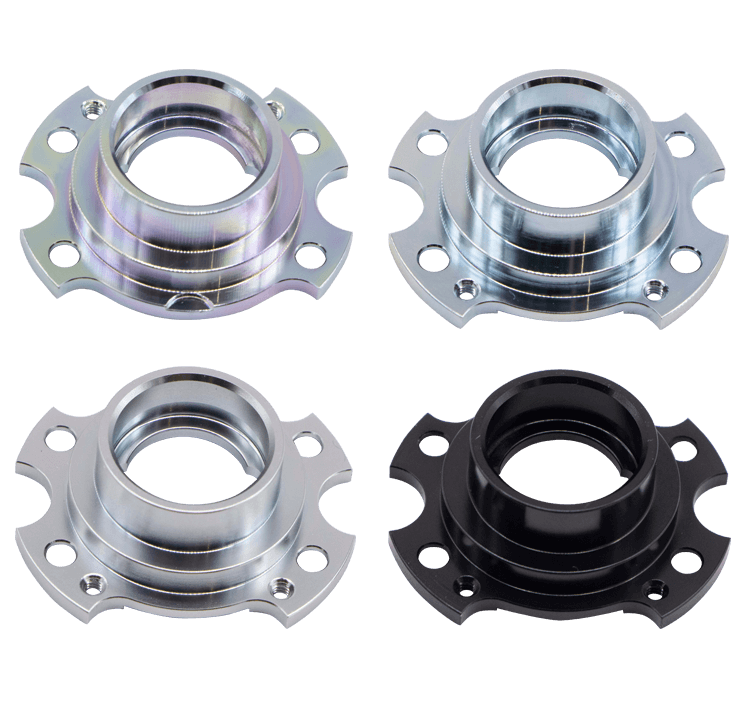
Surface finishes
Electrogalvanizing services
In contrast to other coatings, zinc also provides active cathodic corrosion protection in addition to its shielding effect. In contrast to the more precious iron, zinc acts as a sacrificial anode. This effect also protects the base material in case of damage after coating (scratches or impact marks). Additional properties are achieved by downstream processes, such as passivation, sealing and other similar processes.
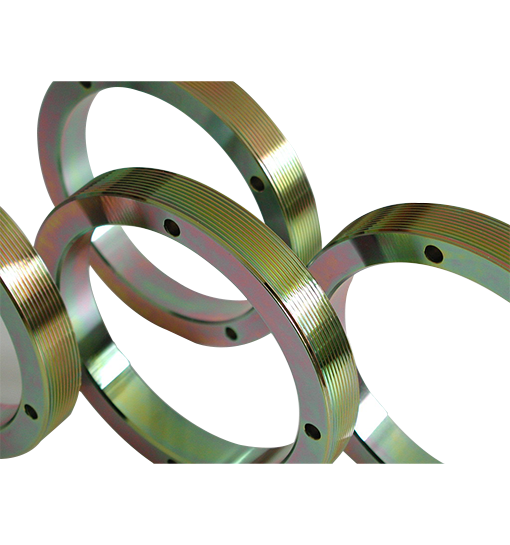
Part surface treatment
CNC machined parts galvanized surface treatment
Zinc plating, also known as cold galvanizing in the industry, is a process that uses electrolysis to form a uniform, dense, well-bonded anodic metal or alloy deposit layer on the surface of a manufactured part. Compared to other metals, zinc is a relatively inexpensive and easy to coat metal, is a low-value corrosion protection plating, and is widely used to protect steel parts, especially against atmospheric corrosion, and for decorative purposes.
Types of zinc plating for CNC machined parts
Types | Description | Minimum salt spray time(h) | Xavier |
I | Zinc plating only,no treatment | – | √ |
II | Colored chromate passivation | 96 | √ |
III | Colorless chromate passivation | 12 | |
IV | Phonsphate conwersion film | – | |
V | Colorless passivation without hwxavalent chromium | 72 | √ |
VI | Colored passivation without hexavalent chromium | 120 | √ |
Plating environment for each film thickness
Classification number and conversion coating suffix | Minimum thickness of plating(μm) | Condition |
Fe/Zn 25 | 25 | SC4-Very harsh:exposure to harsh conditions or frequent exposure to moisture,detergents and salt water solutions,plus possible damage feom dents,scratches or abrasion. |
Fe/Zn 12 | 12 | SC3-Harsh: Exposure to condensation, sweat, rain and detergents. |
Fe/Zn 8 | 8 | SC2-Moderate, exposed to dry indoor environments, but occasional condensation, wear and tear. |
Fe/Zn 5 | 5 | SC1-Mild, exposed to indoor atmosphere, with rare condensation and minimal wear. |
Critical items
Non standard requests
* We provide ASTM B633 electro-galvanized standard. Test methods: X-ray spectrometry film thickness test, zinc layer adhesion test, salt spray test, hydrogen embrittlement test. If you have special needs, please contact sales@xavier-parts.com
**Zinc can protect more precious metals from corrosion, and by adding organic substances, the glossiness of the surface can be adjusted from matte to shiny.
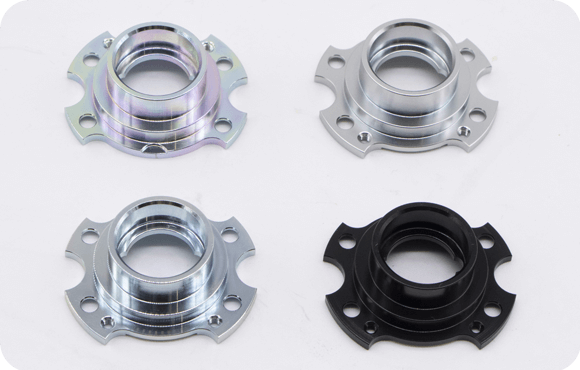
Xavier Zinc Plating Capability
Base material: steel, copper alloy, zinc alloy, stainless steel, aluminum alloy
Reference standard: ASTM B633;
Film thickness grade :5μm、8μm、12μm、25μm
Passivation methods: environmentally friendly: blue and white zinc, colored zinc, yellow zinc, black zinc.
Non-environmental: military green zinc, white zinc, black zinc.
Test methods: X-ray spectrometry film thickness test, zinc layer adhesion test, salt spray test, hydrogen embrittlement test.
Base material Steel, copper alloy, zinc alloy, stainless steel Aluminum alloy Maximum processing size(cm) 230*50*100 50*45*80 Unit price maximum weight(kg) 100 40
Quality
We have high standards for Part surface treatment
We manufacture your custom parts according to strict manufacturing standards and ensure all parts and processes adhere to the Xavier Standard. A thorough verification of these requirements is included in our inspection report that we ship with every order.
-
Standard 1
PO consistent
We ensure that every part after machining is as specified in the PO as customer requirements.
-
Standard 2
Quality check
Prior to MP shipment to ensure that each part meets order specifications and Xavier standards.
-
Standard 3
Require consistent
Ensure conformance of parts and any required documentation prior to dispatching the order.