Standard technical guide for CNC non-standard customized precision parts processing
1.Tool selection
First of all, non-standard precision parts CNC machining has extremely strict requirements on precision. If you want to achieve ultra-high precision and smooth surface, then the choice of tool is very important. A to Z machining can produce industry-specific finished products with extremely high precision and efficiency.
If the tool is worn, the surface finish quality of the machined parts will be significantly reduced, and when performing ultra-precision machining, the cutting speed is not limited by the tool speed.
2.Speed
Secondly, when machining non-standard precision parts, it is preferred to select the one with the smallest speed, which is determined according to the transmission and cutting characteristics of the machine tool, because the smallest speed can ensure the minimum surface roughness and ensure the quality of processing.
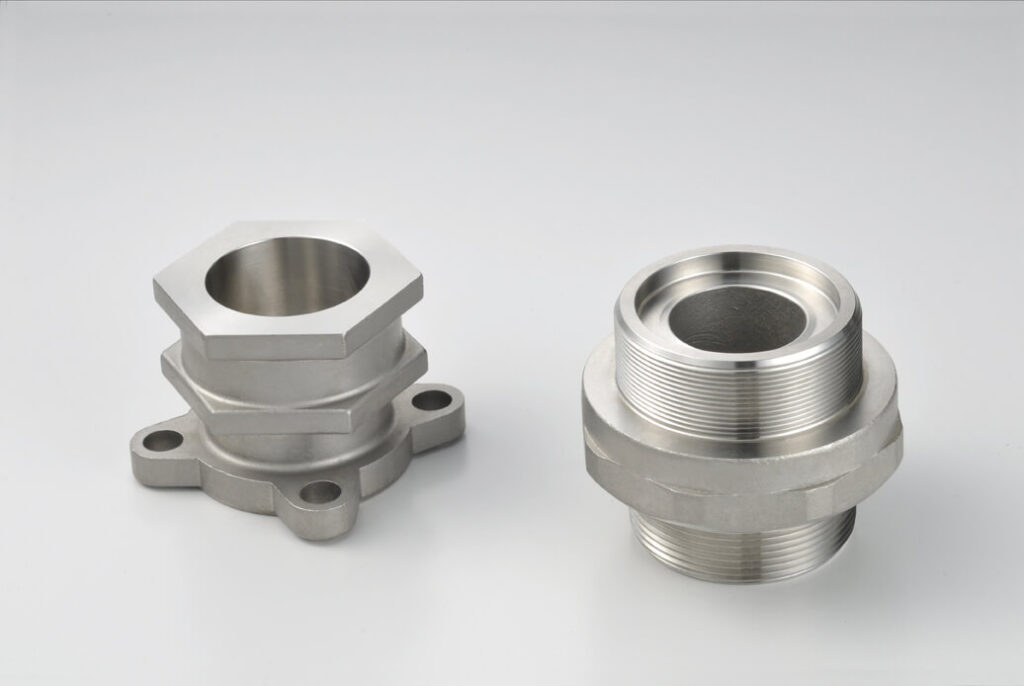
3.Parameters
Finally, let me tell you that the CNC machining of non-standard precision parts is selected according to the parameters of the cutting tool, speed, depth and other parameters. Past experience tells us that selecting a tool with a relatively large rake angle can reduce the cutting force and reduce the deformation. If it is reduced, the length of the contact time between the tool and the chip will gradually become shorter, reducing the basis of the built-up edge.