Key Benefits of Oxide Coatings
Precision machining projects require the highest levels of accuracy and precision to achieve the desired results. One way to improve the performance and durability of precision machined parts is to apply an oxide coating. This is sometimes applied to parts such as walker turner bandsaw parts, zero turn toro mower parts, advance auto parts lem turner, bad boy zero turn parts, and bobcat zero turn mowers parts.
These coatings offer a range of benefits that can significantly improve the overall quality and efficiency of precision machining projects, ensuring the quality of all parts such as walker turner bandsaw parts, zero turn toro mower parts, advance auto parts lem turner, bad boy zero turn parts, and bobcat zero turn mowers parts.
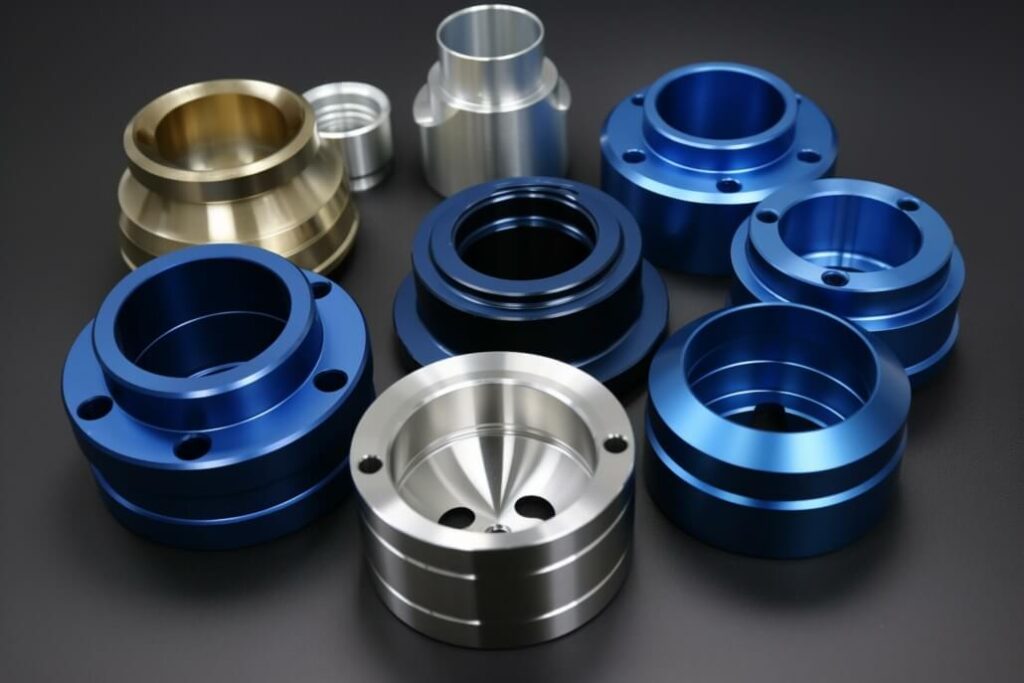
1.Enhanced Wear Resistance of Machined Components
Precision machining involves removing material from a workpiece to create the desired shape or surface finish. This process can subject machined components to significant wear, especially when working with hard materials or high-speed applications. By applying an oxide coating, the surface hardness of machined components can be significantly increased.
This helps reduce wear from friction and abrasion, making the component more durable. Oxide coatings improve wear resistance and also reduce the need for frequent replacement or repairs, saving time and money on precision machining projects.
2.Excellent Corrosion Protection
Machinery components are often exposed to harsh environments such as moisture, chemicals or extreme temperatures, which can cause corrosion and performance degradation over time. Oxide coatings act as a barrier, preventing corrosive agents from reaching the underlying material and causing damage.
The corrosion resistance provided by oxide coatings ensures that machined components maintain their integrity and functionality even under demanding operating conditions. This is particularly important in industries such as aerospace, automotive or medical, where precision machined components can support long-term reliable operation even in harsh environments.
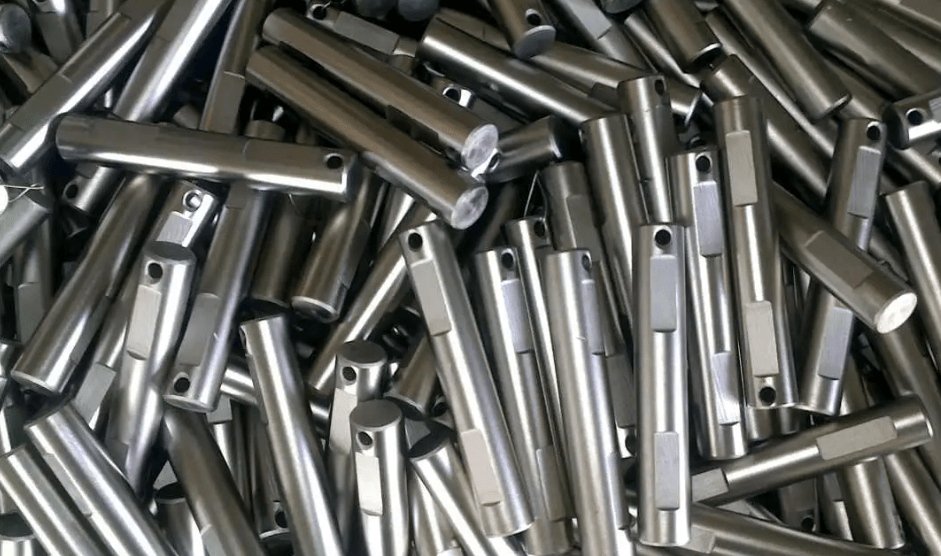
3.Improved Lubricity of Machined Components
Lubrication plays a vital role in precision machining as it reduces friction and heat generation during machining. Inadequate lubrication can lead to increased tool wear, poor surface finish, and even component failure. Oxide coatings can be designed to have self-lubricating properties, reducing the need for external lubricants.
These coatings create a low-friction surface that minimizes contact between the machined component and the cutting tool, which improves machining efficiency and reduces tool wear. The enhanced lubricity provided by oxide coatings also helps achieve superior surface finish and dimensional accuracy in precision machining projects.
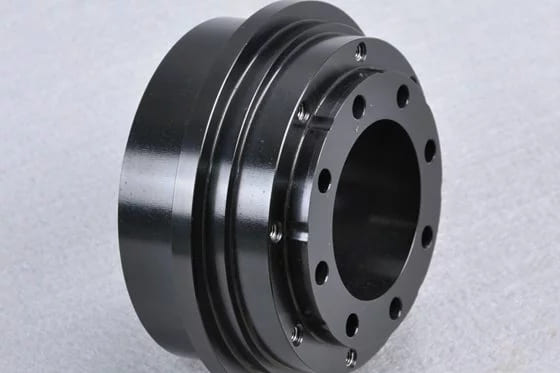
https://en.wikipedia.org/wiki/Thermal_insulation4.Provides Thermal Insulation
This is a great benefit to precision machining projects. Heating is a common problem in machining operations, especially when using high-speed cutting tools or performing long machining processes. Excessive heat can cause thermal expansion, deformation, and even material failure.
By applying an oxide coating with thermal insulation properties, the heat generated during machining can be effectively dissipated and the risk of heat damage to machined components can be reduced. This makes the machining process more stable and predictable, ensuring consistent quality and dimensional accuracy for precision machining projects.