Widely used metal surface treatment process
Metal surface treatment processes are essential to improving the appearance, durability and functionality of metal products. These processes involve a variety of technologies that change the properties of the metal surface, such as its texture, corrosion resistance and adhesion, and they play a role in improving parts. This article will introduce several common metal surface treatment processes in detail to help users have a deeper understanding.
electroplating
One of the most widely used metal surface treatment processes is electroplating. Electroplating involves depositing a thin layer of metal onto the surface of another metal object. This process is often used to enhance the appearance of metal products by giving them a shiny reflective finish. It also improves the metal’s corrosion resistance and increases its hardness.
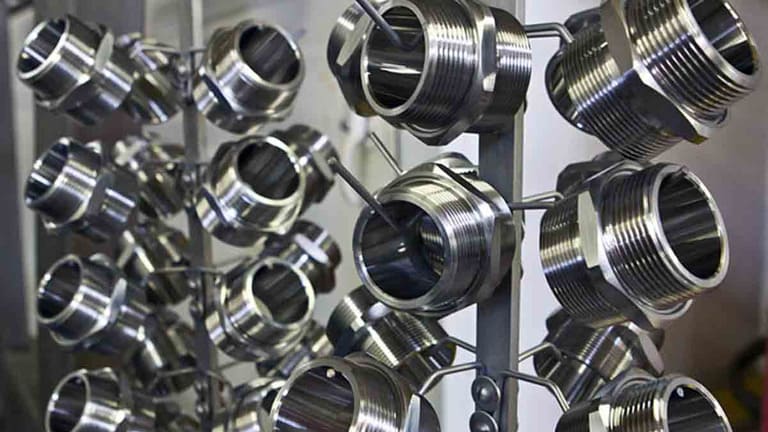
anodizing
Another popular metal surface treatment process is anodizing. Anodizing is mainly used for aluminum and its alloys. It involves the formation of a thick oxide layer on the metal surface through an electrochemical process. Anodizing gives aluminum excellent resistance to corrosion and can also create decorative finishes by staining the oxide layer.
Chemical conversion coating
Chemical conversion coating is another commonly used metal surface treatment process. The process also involves forming a thin protective layer on the metal surface through a chemical reaction. Therefore, the coating not only improves the corrosion resistance of the metal, but also provides a good base for paint or other coatings. So phosphate and chromate coatings are examples of chemical conversion coatings that are widely used in various industries.
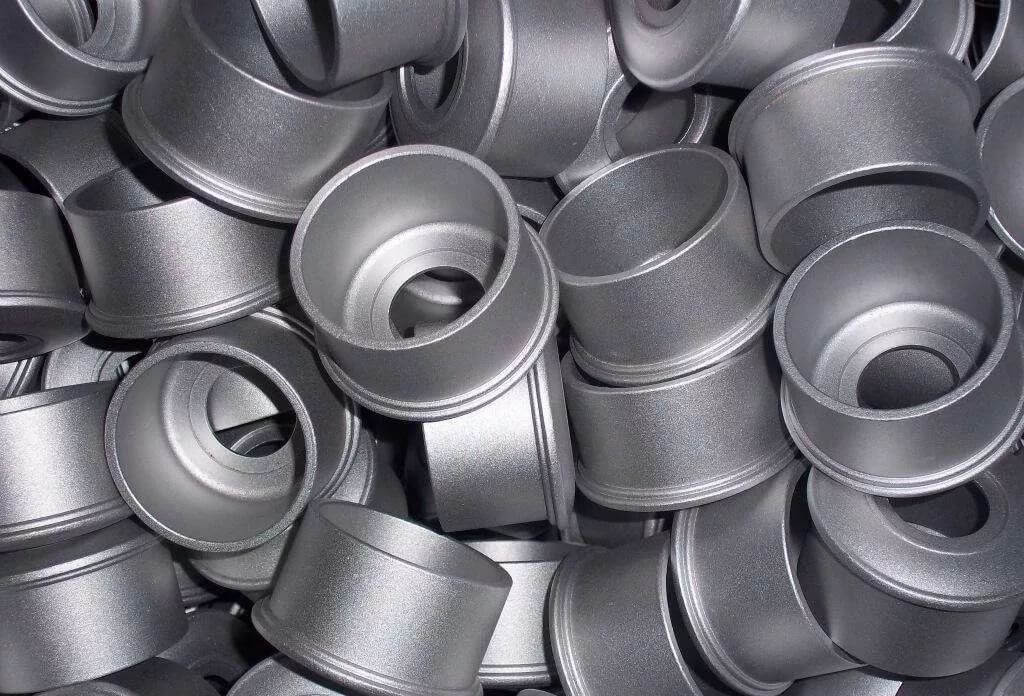
Shot peening
Shot peening is a mechanical metal surface treatment process that involves bombarding the metal surface with fine abrasive particles. This process is used to remove rust, scale, and other contaminants from the surface, leaving it clean and ready for further processing or coating. Shot peening can also be used to create textured surfaces or improve coating adhesion.
Passivation
Passivation is a metal surface treatment process used primarily on stainless steel. It involves removing free iron and other contaminants from the surface, which improves the metal’s corrosion resistance. Passivation is usually accomplished by using an acid solution or immersing the metal in a passivation bath.
Powder coating
Powder coating is a popular metal finishing process that involves applying dry powder to the metal surface. The powder is then heated, causing it to melt and form a protective coating. Powder coating offers excellent corrosion resistance, durability and a variety of color options. It is commonly used in industries such as automobiles, furniture and appliances.
galvanizing
galvanizing is a metal surface treatment process used primarily on steel. Galvanizing involves applying a layer of zinc to the surface of steel through a hot-dip plating or electroplating process. This process gives the steel excellent corrosion resistance and significantly extends its service life. Galvanized steel is commonly used in construction, automotive and other industries.
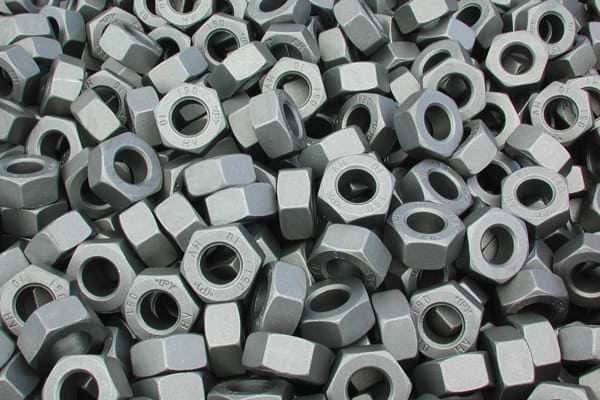
conclusion
metal surface treatment processes play a vital role in enhancing the appearance, durability and functionality of metal products. Electroplating, anodizing, chemical conversion coatings, shot peening, passivation, powder coating, and galvanizing are some of the common processes used to modify the properties of metal surfaces. Each process has its own advantages and applications, and the selection of the appropriate treatment method depends on the specific requirements of the metal product.