Key Benefits of Thermoset Powder Coatings
Thermoset powder coatings are a popular choice in the powder coating world due to their many benefits. These coatings offer a range of benefits that make them ideal for a wide range of applications. Even parts like used zero turn mower parts are sometimes used.
In this article, we will look at some of the benefits of thermoset powder coatings and why they are the preferred choice for many industries, as well as options in the used market such as used zero turn mower parts.
1.Durability
These coatings are known for their excellent resistance to abrasion, corrosion, and chemicals. They provide a protective layer that can withstand harsh environments and maintain their appearance for a long time. This durability makes them ideal for applications where the coated surface is exposed to heavy use or extreme conditions.
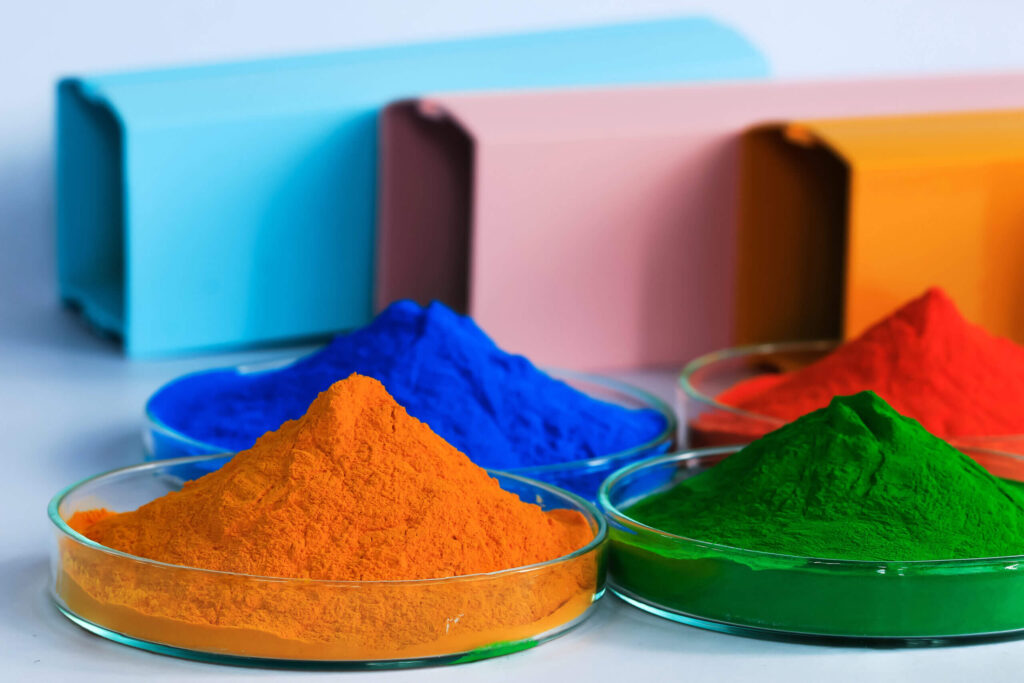
2.Versatility
These coatings are formulated to achieve a variety of surface effects, including smooth, textured, metallic, and even special effects. This versatility provides endless design possibilities and customization options. Whether it is a stylish glossy finish for high-end products or a textured finish for added grip, thermosetting powder coatings can provide the desired aesthetic.
3.Excellent Adhesion
When applied correctly, these coatings adhere tightly to the substrate, forming a strong bond. This adhesion ensures that the coating remains intact and is not prone to peeling or chipping. At the same time, it also enhances the overall performance of the coated surface, providing additional protection against impact and wear.
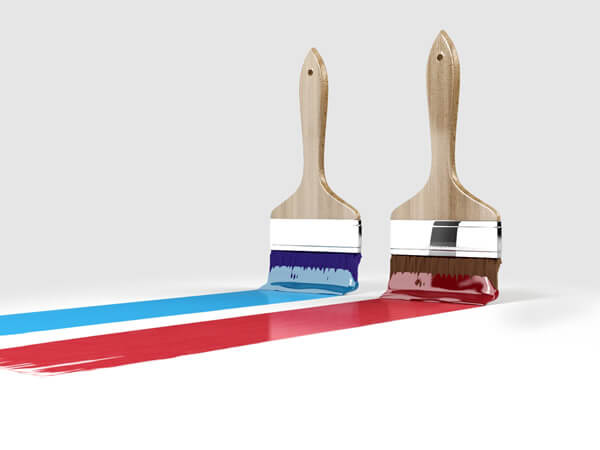
4.Environmentally friendly
Unlike liquid coatings, which often contain volatile organic compounds (VOCs), thermosetting powder coatings contain no solvents and release negligible amounts of VOCs during the curing process. This makes them a safer, more sustainable choice for the environment and painters. In addition, powder coating overspray can be collected and reused, minimizing waste and reducing overall material consumption.
5.Excellent coverage and efficiency
These coatings can be applied in a single coat, eliminating the need for multiple coats. This not only saves time and labor, but also reduces material costs. The high transfer efficiency of powder coatings ensures that most of the coating ends up on the substrate, minimizing waste and maximizing the effectiveness of the coating.
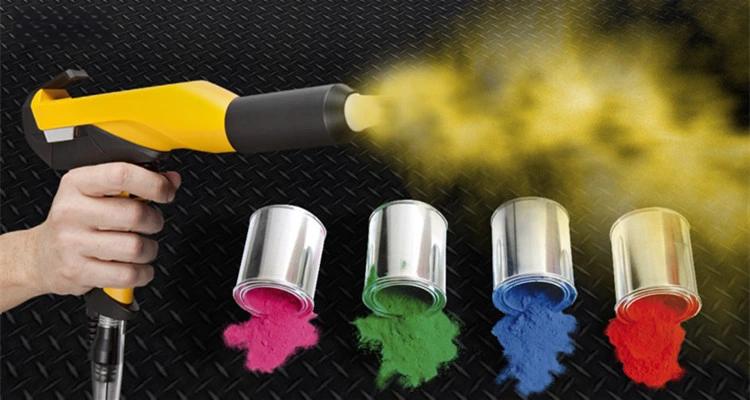
6.Relatively fast curing process
After coating, the coated parts are placed in an oven and heated, causing the powder to melt and flow into a continuous film. This curing process is typically completed within a few minutes, resulting in faster turnaround times and increased productivity. Rapid curing also means that the coated parts can be handled and packaged immediately after coating, reducing the risk of damage or contamination.