Limitations of CNC laser cutting technology
While CNC laser cutting technology offers many advantages, it also has limitations. Understanding these limitations is critical for businesses and manufacturers considering implementing the technology. This is especially true for plastic turned parts, yazoo kees zero turn mower parts, yazoo kees zero turn mowers parts, zero turn toro parts, and zt7000 craftsman zero-turn parts.
In this section, we will explore some of the key limitations of CNC laser cutting, such as on parts such as plastic turned parts, yazoo kees zero turn mower parts, yazoo kees zero turn mowers parts, zero turn toro parts, and zt7000 craftsman zero-turn parts.
1.CNC laser cutting cannot cut thick materials
Laser cutting is most effective with relatively thin materials, such as metals that are not thicker than a certain thickness. This is because when thicker materials are involved, the energy of the laser is dispersed over a larger area, resulting in less efficient cutting. Therefore, this limitation is particularly problematic for industries that need to cut thick materials regularly.
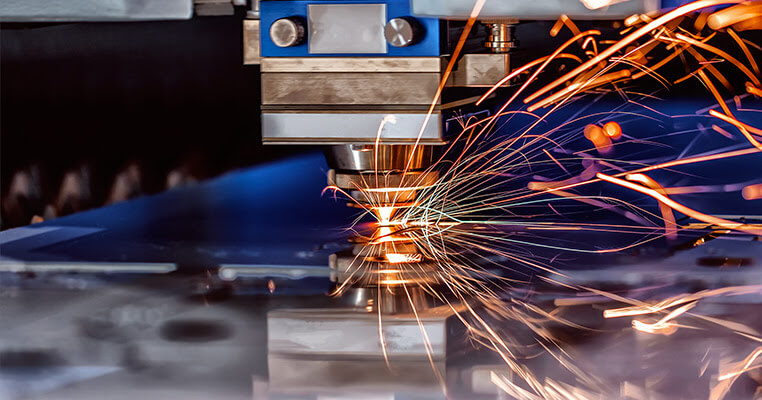
2.CNC laser cutting cannot effectively cut reflective materials
Reflective materials, such as copper or brass, tend to reflect the laser beam instead of absorbing it. Therefore, the energy of the laser is not fully utilized, resulting in poor cut quality and slow cutting speeds. For industries that often work with reflective materials, this limitation can be a significant disadvantage.
3.Material limitations
CNC laser cutting technology is not suitable for all types of materials. Some materials, such as PVC or polycarbonate, release toxic fumes when laser cut. These fumes can be harmful to the environment and the health of the operator. Therefore, industries that work with these materials may need to explore alternative cutting methods to ensure the safety of workers and the environment.
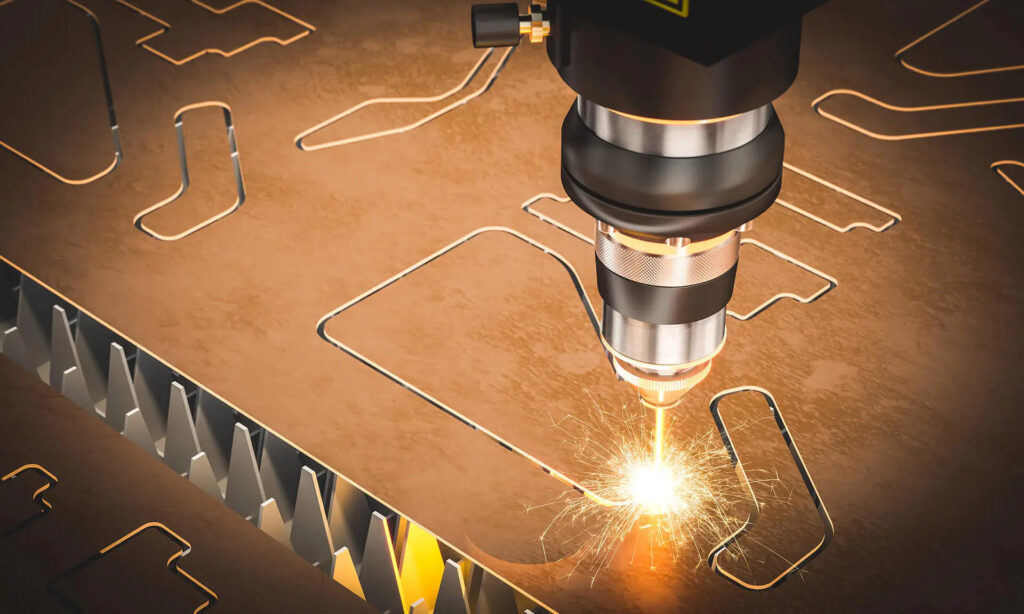
4.Cutting complexity
In addition to material limitations, CNC laser cutting technology also has limitations in terms of the complexity of the cuts that can be achieved. While laser cutting is very precise, it can be difficult to handle complex designs or shapes that require multiple passes. The beam width of the laser and the heat generated during the cutting process can cause fine areas to deform or melt, affecting the overall quality of the cut. This limitation can be a significant issue for industries that require complex cuts.
5.Cost-effectiveness
In addition, CNC laser cutting technology is not suitable for all outputs. While it is very effective for small to medium-sized production, it may not be cost-effective for large-scale production. The initial investment in CNC laser cutting equipment can be large, and operating costs such as electricity and maintenance can also increase. Therefore, businesses that require large-scale production may need to consider alternative cutting methods that provide better cost-effectiveness.
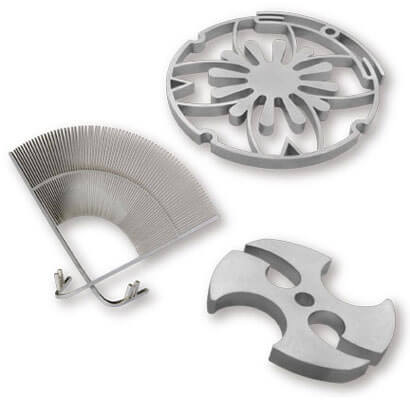
6.Skilled Operator Required
To ensure optimal performance. Operating a CNC laser cutting machine requires technical expertise as well as specific software and programming knowledge. Without a skilled operator, the risk of errors or accidents increases, which can result in costly mistakes or equipment damage. This limitation highlights the importance of investing in proper training and hiring qualified personnel to operate a CNC laser cutting machine.
7.Summary
While CNC laser cutting technology offers many advantages, it is important to be aware of its limitations. These limitations include the difficulty of cutting thick and reflective materials, limitations on certain types of materials, limitations in achieving complex cuts, cost-effectiveness of large-scale production, and the need for skilled operators. By understanding these limitations, businesses and manufacturers can make informed decisions about whether CNC laser cutting technology is suitable for their specific needs and requirements.