Comparing anodizing and electrophoretic coating for aluminum profile surface treatment
Aluminum is a versatile material that is widely used in various industries due to its lightweight and corrosion-resistant properties. However, in order to enhance the appearance and protect aluminum profiles from environmental factors, aluminum profiles are usually surface treated.
Two common methods of aluminum profile surface treatment are anodizing and electrophoretic painting. In this article, we will compare these two methods to help you understand the differences between them and choose the best option for your aluminum profile.
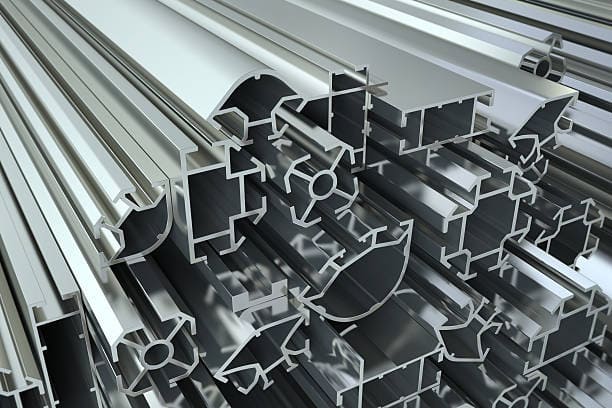
1.Introduction to Anodizing
Anodizing is a widely used surface treatment method for aluminum profiles. It involves immersing the profile in an electrolyte solution and passing electricity. The process forms a layer of oxide on the surface of aluminum, which not only improves the appearance of aluminum, but also improves its corrosion resistance and wear resistance. Anodizing can produce a variety of colors, allowing customization and aesthetics.
In addition, the anodized layer is porous, which makes it suitable for further processing, such as dyeing or sealing.
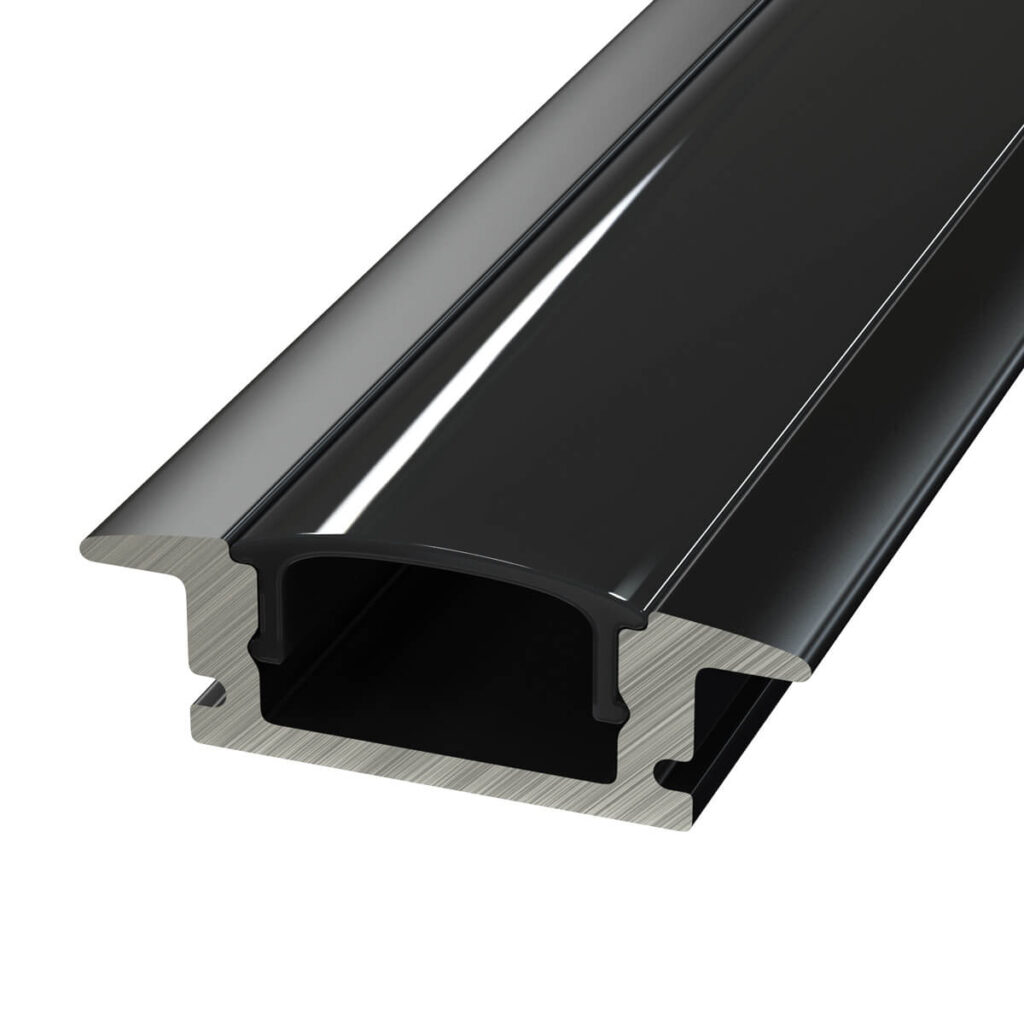
2.Introduction to Electrophoretic Painting
On the other hand, electrophoretic painting, also known as electrophoretic painting or e-painting, is a method in which aluminum profiles are immersed in a paint or coating tank and an electric current is applied. The electric current causes the coating material to migrate and adhere to the profile surface, forming a uniform and durable coating.
Meanwhile, in addition to offering excellent corrosion resistance and being able to be painted in a wide range of colors, electrophoretic coatings can also provide good coverage and reach areas that are difficult to reach with other painting methods.
3.Differences between anodizing and electrophoretic coating
When comparing anodizing and electrophoretic coating, there are several factors to consider.
1) Different Finishes
Anodizing creates a translucent layer that lets the natural beauty of aluminum show through, while electrophoretic coating provides a solid, opaque surface. The two choices depend on the desired aesthetic effect and the specific requirements of the application.
2) Different Levels of Corrosion Resistance of the Coatings
Anodizing forms a thick, dense oxide layer that provides excellent corrosion protection. On the other hand, the thin layer formed by electrophoretic coating may not provide the same level of corrosion resistance as anodizing. However, with proper pretreatment and the use of high-quality coating materials, electrophoretic coatings can still provide satisfactory corrosion protection.
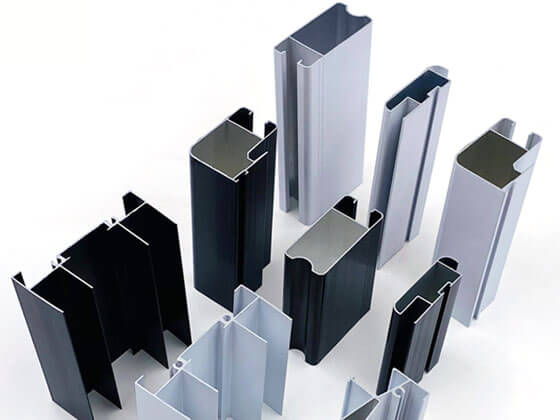
3) Cost and Complexity
Another important consideration is the cost and complexity of the surface preparation process. Anodizing is generally more cost-effective and easier to implement than electrophoretic coating. Anodizing does not require the use of expensive coating materials or complex equipment.
On the other hand, electrophoretic painting involves more complex equipment and requires a controlled environment to ensure the quality of the coating. Therefore, the choice between the two methods may depend on the available budget and resources.
In summary, anodizing and electrophoretic painting are two common methods of surface treatment for aluminum extrusions. Anodizing provides a translucent and corrosion-resistant surface, while electrophoretic painting provides a strong and durable coating.
The choice between the two methods depends on factors such as the desired appearance, the level of corrosion resistance, and the available resources. By understanding the differences between anodizing and electrophoretic painting, you can make an informed decision and ensure the best results for your aluminum extrusions.