Advantages of Wire EDM Machining in the Aerospace Industry
Wire EDM, also known as Electro-Discharge Machining, is a high-precision, high-efficiency machining method that is widely used in various industries, including the aerospace industry.
This article will explore the advantages of wire EDM in the aerospace industry and explain its applications.
1.High-precision production of complex shapes
Aerospace components often require complex designs and tight tolerances, and wire EDM excels in meeting these requirements. The process uses a fine wire electrode to cut the workpiece, which can achieve precise and complex cuts that are difficult to achieve with traditional machining methods.
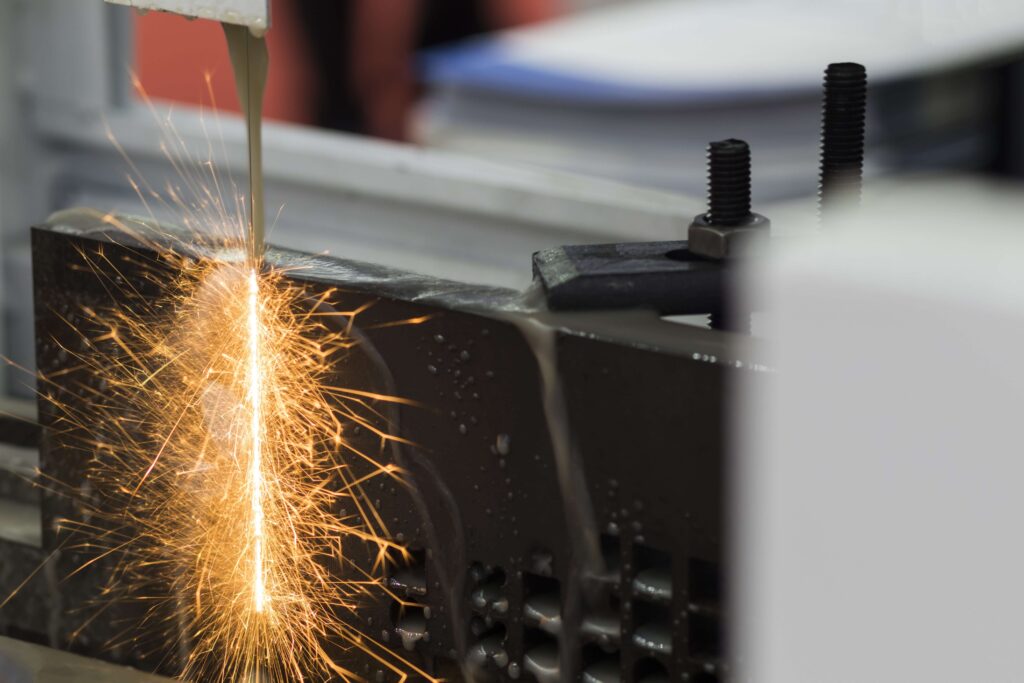
2.Machining a variety of materials
Aerospace components are often made of exotic materials such as titanium, Inconel, and composites, which can be challenging to machine.
However, the process can easily handle these materials due to its non-contact cutting method. This makes it a versatile choice for aerospace manufacturers, as they can use wire EDM for a variety of components.
3.Excellent surface finish and accuracy
This is critical in the aerospace industry. Aerospace components need to meet strict quality standards, and any flaws or inaccuracies can affect their performance and safety.
The process produces smooth and precise cuts, resulting in high-quality surface finish and dimensional accuracy. This ensures that aerospace components meet required specifications and perform at their best.
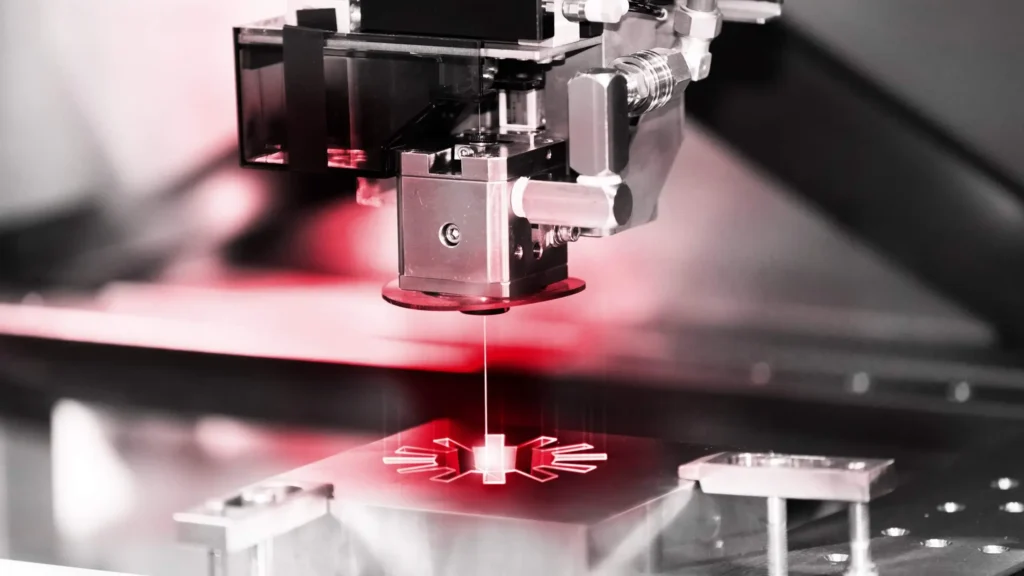
4.Saves Time and Cost
In addition to its high accuracy and versatility, the process also saves time and money for the aerospace industry. The process is highly automated, allowing for efficient, continuous production. Once the initial setup is complete, the wire EDM machine can run unattended, allowing the operator to focus on other tasks.
This automation reduces labor costs and increases productivity, making the process an affordable option for aerospace manufacturers.
5.Reduces Material Waste
Wire EDM also reduces material waste in the aerospace industry. Conventional machining methods typically result in a large amount of material waste due to the cutting process. However, wire EDM is a non-contact cutting method, which means that material waste is minimized.
At the same time, the fine wire electrodes used in the process also produce narrower kerf widths, which reduces the amount of material removed. This not only reduces material costs, but also contributes to a more sustainable manufacturing process.
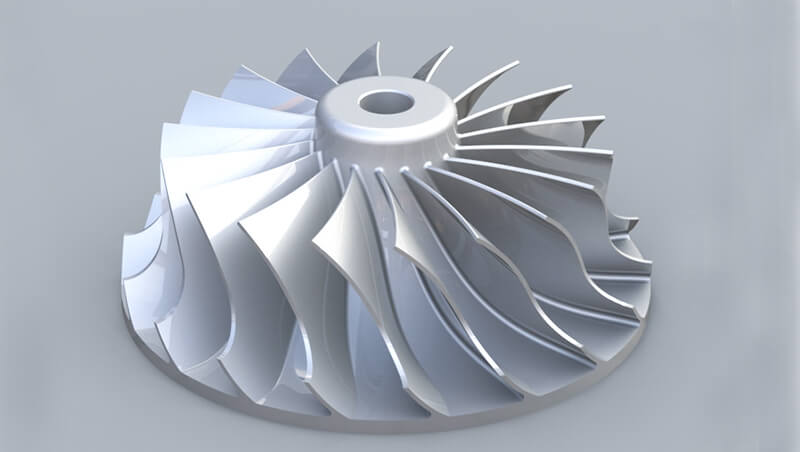
In summary, wire EDM offers a variety of benefits in the aerospace industry. Its ability to produce complex shapes with high accuracy, process a variety of materials, and provide excellent surface finish and precision makes it a valuable tool for aerospace manufacturers.
Additionally, its ability to save time and money, as well as reduce material waste, further enhances its appeal in the aerospace industry. As technology continues to advance, wire EDM is likely to play a more important role in the production of aerospace components.