Stainless Steel CNC Machining vs. Casting: A Comprehensive Comparison
Stainless steel is favored in various industries for its excellent durability, excellent corrosion resistance and pleasing aesthetics. When manufacturing stainless steel parts, stainless steel CNC machining and stainless steel casting are two common methods. So, what are the differences between these two processing methods? In this article, I will lead you to explore these two processing processes in depth.
1.Advantages and Disadvantages of Stainless Steel CNC Machining
1) High Precision and Accuracy
First and foremost, CNC machining offers high precision and accuracy, ensuring that the final product meets the required specifications. This is especially important for industries that require tight tolerances, such as aerospace and medical.
2) Wide Range of Design Possibilities
Furthermore, CNC machining offers a wide range of design possibilities. Complex shapes and intricate details can be easily achieved with this method, making it suitable for manufacturing customized, unique stainless steel parts.
3) Versatility
Furthermore, CNC machining is a versatile process that can be used for both small-scale and large-scale production, making it suitable for a variety of manufacturing needs.
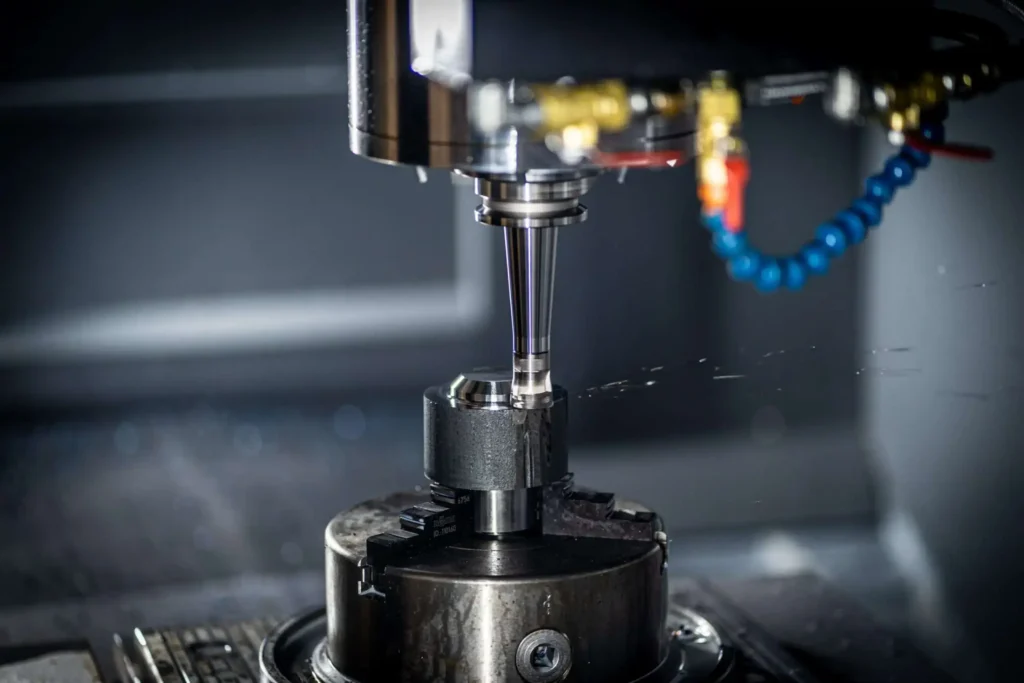
However, there are also some disadvantages to stainless steel CNC machining.
1) High Cost
One of the main disadvantages is the high cost of this method. Because CNC machines are expensive to purchase and maintain, and the process itself requires skilled operators to accurately produce parts that meet standards. This can significantly increase the overall production cost, especially for smaller projects.
2) Time-consuming
In addition, CNC machining is a time-consuming process. Each part needs to be programmed and set up individually, which can take quite a while. This can be a disadvantage for industries that require fast turnaround times or have high production demands.
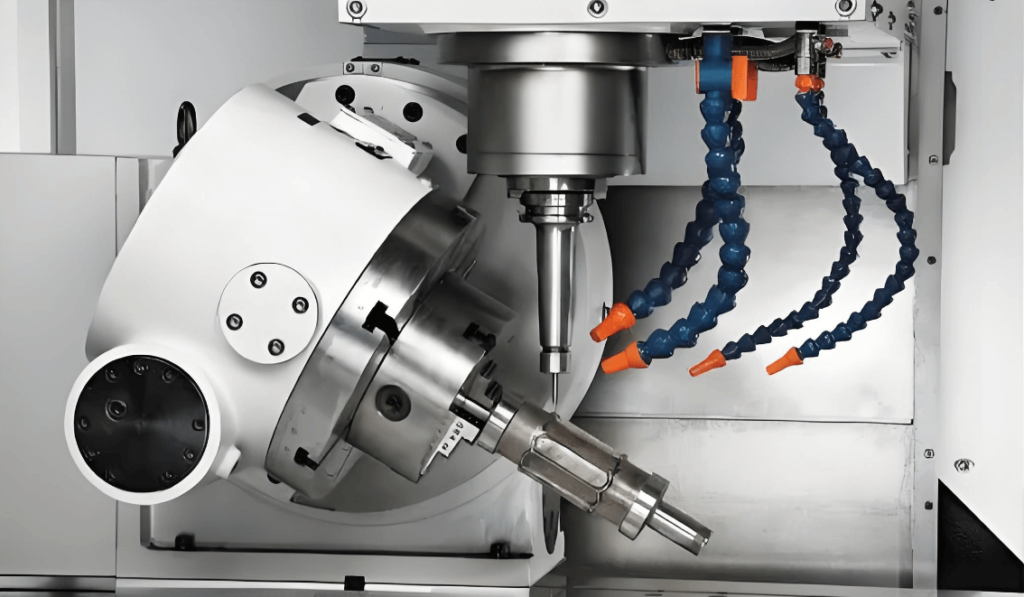
2.Advantages and Disadvantages of Stainless Steel Casting
Stainless steel casting involves pouring molten stainless steel into a mold to form the desired shape. This method has its own set of advantages.
1) Producing Complex Parts
First, casting can produce complex and delicate shapes that may be difficult or impossible to achieve through CNC machining. This makes it suitable for industries that require unique and customized parts.
2) Cost Savings
Stainless steel casting is a cost-effective method, especially for large-scale production. Compared to CNC machining, casting has a relatively low initial setup cost, and the process itself is less labor-intensive. This can result in significant cost savings, especially for industries with high production volumes.
3) Saves on production time
In addition, casting has a faster production time compared to CNC machining. Once the mold is ready, multiple parts can be produced simultaneously, reducing overall production time. This is very beneficial for industries that require fast turnaround times or time-sensitive projects.
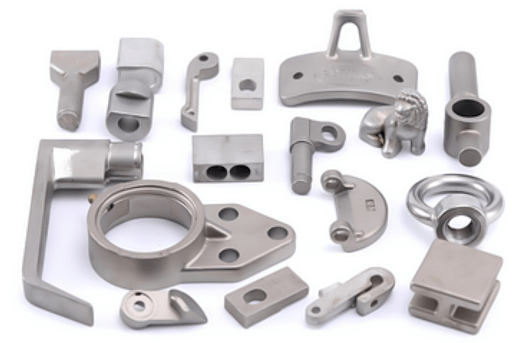
However, stainless steel casting also has some disadvantages.
1) Limited precision
One of the main disadvantages is limited precision and accuracy compared to CNC machining. The casting process can cause slight variations in size and surface finish, which may not be suitable for industries that require high-precision parts.
2) Low flexibility
In addition, casting may not be suitable for small-scale production or projects that require frequent design changes. The initial setup of casting can be time-consuming and costly, and it has low flexibility compared to CNC machining.
In summary, both stainless steel CNC machining and stainless steel casting have their own advantages and disadvantages. CNC machining offers high precision and design flexibility, but is more expensive and has longer production times.
Casting, on the other hand, is cost-effective and has faster production speeds, but may lack precision and flexibility. Ultimately, the choice between the two methods depends on the specific requirements of the project and the industry in which it is used.
But both can be used to manufacture grinder welder parts, CNC milling machine parts, vertical milling machine parts, pepper grinder replacement parts, and Peugeot pepper grinder replacement parts.