Essential Considerations for Effective Sheet Metal Parts Design
Sheet metal part design is a critical aspect of many industries, including automotive, aerospace, and construction. The ability to create effective sheet metal designs is essential to ensure the structural integrity and functionality of a variety of products.
In this article, we will discuss some basic considerations for effective sheet metal design.
1.Material Selection
One of the first things to consider when designing a sheet metal part is the choice of material. Different materials have different properties, such as strength, ductility, and corrosion resistance. It is essential to select a material that meets the specific requirements of the application. For example, if the part will be exposed to harsh environmental conditions, a corrosion-resistant material such as stainless steel may be the best choice.
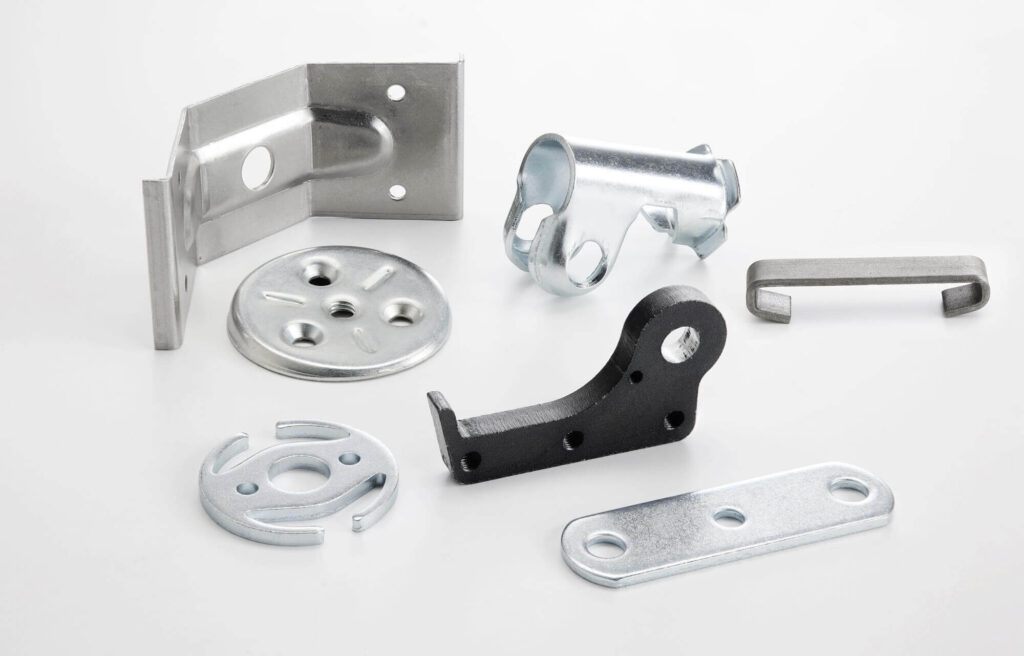
2.Sheet Metal Thickness
An important consideration is the thickness of the sheet metal. This is because thickness affects the strength and rigidity of the part. Thicker sheet metal is stronger but may be more challenging to form and manipulate.
On the other hand, thinner sheet metal is more flexible but may lack the strength required for certain applications. Therefore, it is important to strike a balance between strength and formability when selecting sheet metal thickness.
3.Manufacturing Process
When designing sheet metal parts, it is essential to consider the manufacturing process. Sheet metal parts are typically manufactured through processes such as bending, cutting, and welding. Each manufacturing process has its limitations and requirements. For example, a bending operation may require the use of specific tools or equipment.
By considering the manufacturing process during the design phase, potential problems can be identified and resolved early, saving time and resources.
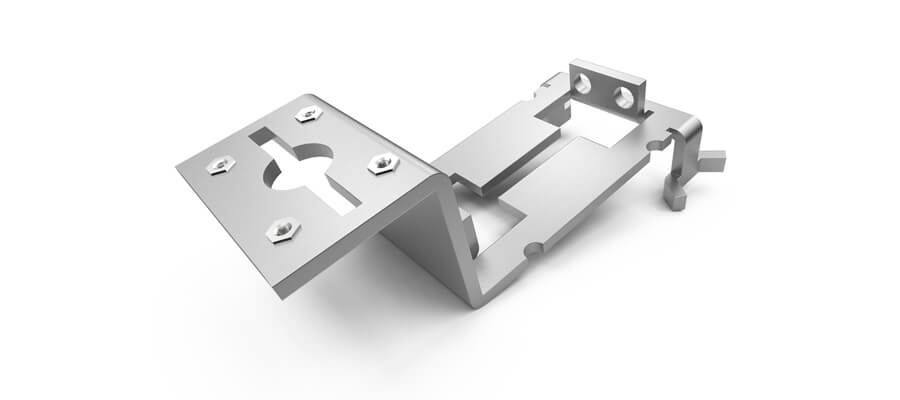
4.Reduce Defects
A common challenge in sheet metal design is minimizing the occurrence of defects, such as cracks, wrinkles, or warping. These defects can compromise the structural integrity and functionality of the part.
To minimize defects, it is important to design parts with smooth, gradual curves and avoid sharp corners or abrupt changes in geometry. In addition, using the proper tools and equipment during the manufacturing process helps reduce the likelihood of defects.
5.Joining Methods
Another consideration for effective sheet metal design is using the proper joining methods. Sheet metal parts often need to be joined to create complex assemblies.
Common joining methods include welding, riveting, and bonding. The choice of joining method depends on factors such as the material, part geometry, and required strength. It is important to choose a joining method that provides adequate strength while minimizing deformation or damage to the sheet metal.
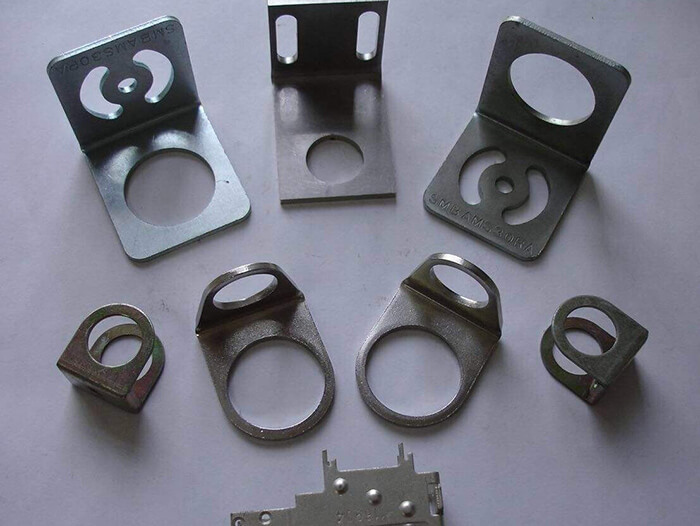
6.Tolerances of Sheet Metal Parts
In addition to these considerations, it is critical to design sheet metal parts with the proper tolerances. Tolerances define the permissible variation in dimensions and ensure that parts fit correctly.
For parts that require precise alignment or fit, tight tolerances may be required, while for less critical applications, looser tolerances may be acceptable. By specifying appropriate tolerances, the functionality and performance of the final product can be ensured.
In summary, effective sheet metal design requires careful consideration of a variety of factors. Material selection, sheet metal thickness, manufacturing processes, defect prevention, joining methods, and tolerances all play a vital role in creating functional and structurally sound sheet metal parts. By considering these factors during the design phase, engineers can optimize the performance and reliability of their products.