Copper CNC Machining Best Practices Guide
Copper is a commonly used metal in CNC machining and is widely used in many fields such as electronics, automotive, aerospace, etc. In this guide, we will take a deep look at the relevant technologies of copper in CNC.
Introduction to Copper CNC Machining
Copper CNC machining is a process that uses computer numerical control (CNC) machines to shape and cut copper materials into desired shapes. The process is widely used in various industries such as electronics, automotive and aerospace due to copper’s excellent properties such as high electrical and thermal conductivity, corrosion resistance and ductility.
The CNC machining process begins with the creation of a digital design or model using computer-aided design (CAD) software. The design is then converted into a set of instructions that the CNC machine can understand and execute. These instructions control the movement of the machine’s cutting tools, allowing for precise and accurate shaping of the copper material.
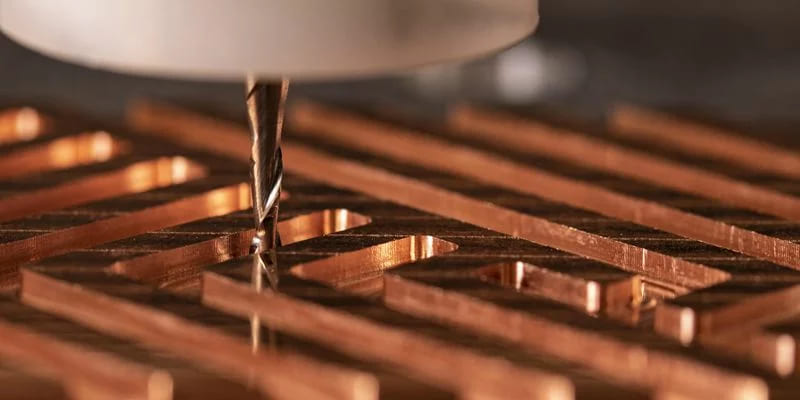
Processes Used in Copper CNC Machining
A common process is milling, which involves removing material from a copper workpiece using a rotating cutting tool. This process is ideal for creating flat surfaces, slots and holes in copper materials.
Another process is turning, which involves rotating a copper workpiece while holding the cutting tool against it. This process is used to create cylindrical shapes such as rods or tubes, and can also be used to create threads on the surface of copper materials.
In addition to milling and turning, other CNC machining processes that can be used for copper include drilling, tapping and boring. These processes are used to create holes, threads, and larger cavities in copper materials, respectively.
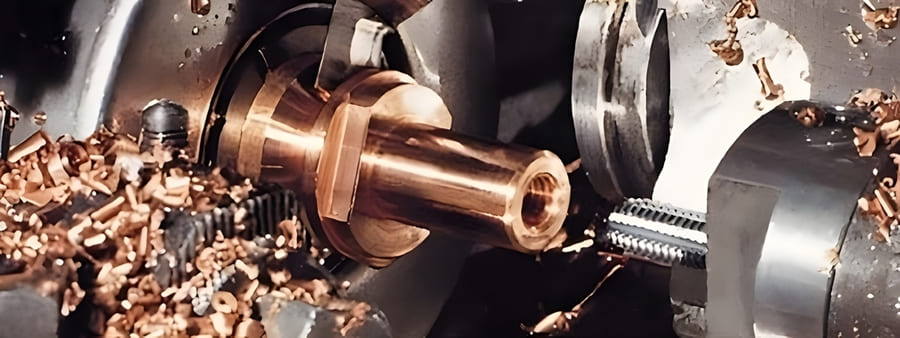
Copper CNC Machining Material Grade Selection
There are several different types of copper available for CNC machining. The most common grade is C110, which is a pure copper with excellent electrical conductivity. This grade is often used in electrical and electronic applications that require high electrical conductivity.
Other copper grades commonly used for CNC machining include C101, C102, and C122. These grades vary in the amount of impurities and alloying elements that affect their mechanical and electrical properties. It is important to select the right copper grade for a specific application to ensure optimal performance.
Copper CNC Machining Considerations
When CNC machining copper, there are a few important things to keep in mind.
First, parts must be designed with the proper tolerances to ensure a good fit and functionality. Copper is a relatively soft material, so sharp corners and thin walls must be avoided as these can cause deformation or breakage during machining.
It is also important to consider the heat generated by the part during machining. Since copper tends to deform when heated, parts must be designed to minimize the amount of heat generated during machining. This can be achieved by using the proper tools and machining techniques and incorporating features such as fillets and chamfers to more evenly distribute stress and heat.
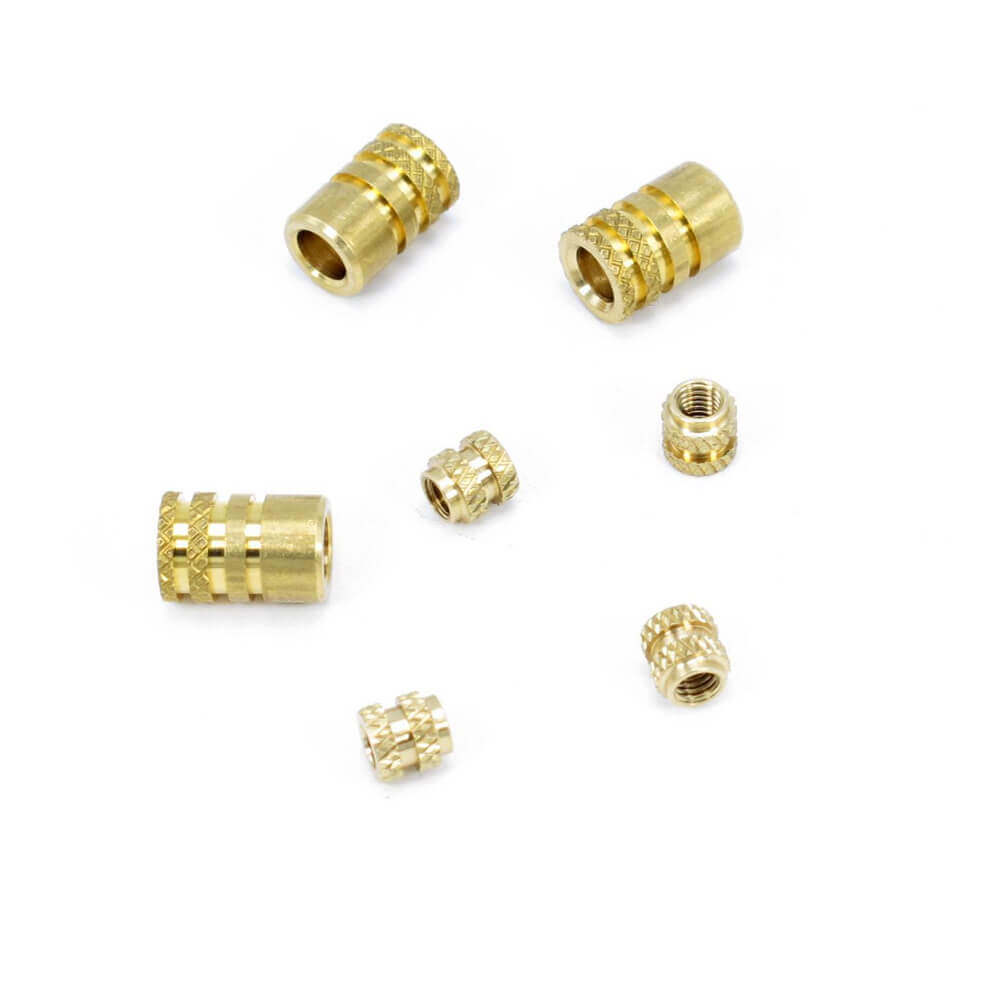
Summary
Copper CNC machining is a versatile process that allows for precise shaping and cutting of copper materials. Complex designs can be easily achieved using CNC machines, making them a popular choice for a variety of industries. By considering design factors and selecting the appropriate copper grade, high-quality parts can be produced efficiently and effectively.