Introduction to Swiss Machining
Swiss machining, also known as Swiss turning or Swiss threading, is a method for manufacturing small, complex parts with high precision and high efficiency. It is widely used in industries such as medical, aerospace, and electronics where precision and quality are critical.
In this article, we will introduce the basic principles and applications of Swiss machining, illustrate its advantages, and highlight its main features.
1.Main Features of Swiss Machining
1) Cutting Tools
At its core, Swiss machining is a type of CNC (computer numerical control) machining that uses a sliding headstock lathe. Unlike conventional lathes, where the workpiece rotates while the cutting tool remains stationary, Swiss machining involves the opposite motion. The cutting tool remains stationary while the workpiece moves in a controlled manner. This allows for greater precision and control of the machining process.
2) High Precision
Ability to process long and slender components with high accuracy. The sliding headstock lathe used in Swiss machining allows the workpiece to be supported close to the cutting tool, thereby minimizing deflection and ensuring precise machining. This makes Swiss machining particularly suitable for applications that require tight tolerances and complex geometries.
3) Versatility
Ability to perform multiple operations in a single setup. Sliding headstock lathes are equipped with a variety of tools, such as drills, milling cutters, and taps, that can be used to perform a variety of machining operations.
This feature not only eliminates the need for multiple machines and setups, but also reduces production time and costs. In addition, the process allows machining on multiple axes simultaneously, further improving efficiency and productivity.
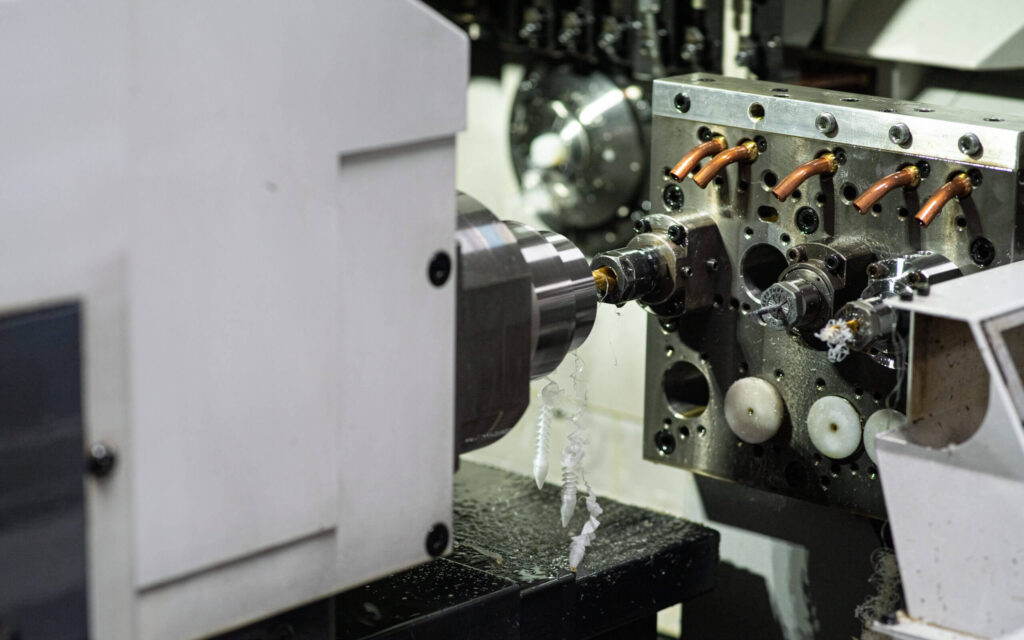
2.Application scope of Swiss machining
1) Medical industry
Used in the production of surgical instruments, implants, and other medical devices. The high precision and tight tolerances achieved by the process are essential to ensure the safety and effectiveness of these critical components.
In addition, the ability to machine complex geometries makes it possible to produce complex medical devices that are difficult or impossible to manufacture using traditional machining methods.
2) Aerospace industry
The production of aircraft components such as turbine blades and fuel system components requires high precision and reliability. The process provides the necessary accuracy and repeatability to meet the stringent requirements of the aerospace industry.
In addition, the ability to machine difficult-to-cut materials such as titanium alloys and nickel alloys makes the process ideal for aerospace applications.
3) Electronics industry
The process is used to produce connectors, pins, and other small components. The small size and complex geometry of these parts require high precision and tight tolerances, which the process can achieve.
In addition, the process is able to process a wide range of materials, including plastics and metals, making it versatile and suitable for a variety of electronic applications.
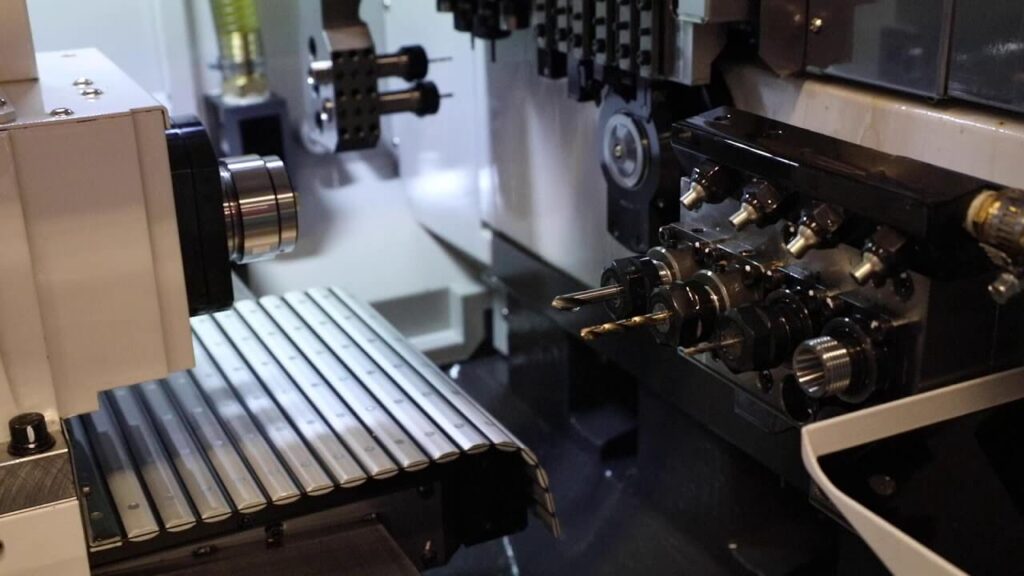
In summary, Swiss machining is a high-precision, efficient method for manufacturing small, complex parts. Its ability to process long and thin parts with high accuracy, perform multiple operations in a single setup, and process a wide range of materials makes it a valuable tool in industries such as medical, aerospace, and electronics.
With its many advantages and applications, Swiss machining continues to play a vital role in the manufacturing industry.