The Basics of High Speed Cutting
High speed cutting is a machining process that uses a cutting tool that rotates at high speeds to remove material from a workpiece. CNC machining services birmingham provides CNC machining services including cutting, milling and turning to a wide range of industries. The process is commonly used in industries such as aerospace, automotive and manufacturing where precision and efficiency are critical.
The concept of high speed cutting revolves around the idea of increasing the cutting speed while maintaining the same feed rate. By doing so, the cutting tool can remove material at a faster rate, resulting in reduced machining time and increased productivity. However, it is important to note that high speed cutting is not simply about increasing the rotational speed of the cutting tool. It also involves various other factors that need to be considered for optimal results.
One of the key factors in high-speed cutting is the selection of the cutting tool. High-speed cutting requires tools that are specifically designed to withstand the increased cutting forces and temperatures associated with the process. These tools are typically made from materials such as carbide or ceramic, which have high hardness and heat resistance. Additionally, the geometry of the cutting tool plays a crucial role in high speed cutting. Tools with sharp cutting edges and low cutting forces are preferred to minimize tool wear and improve surface finish.
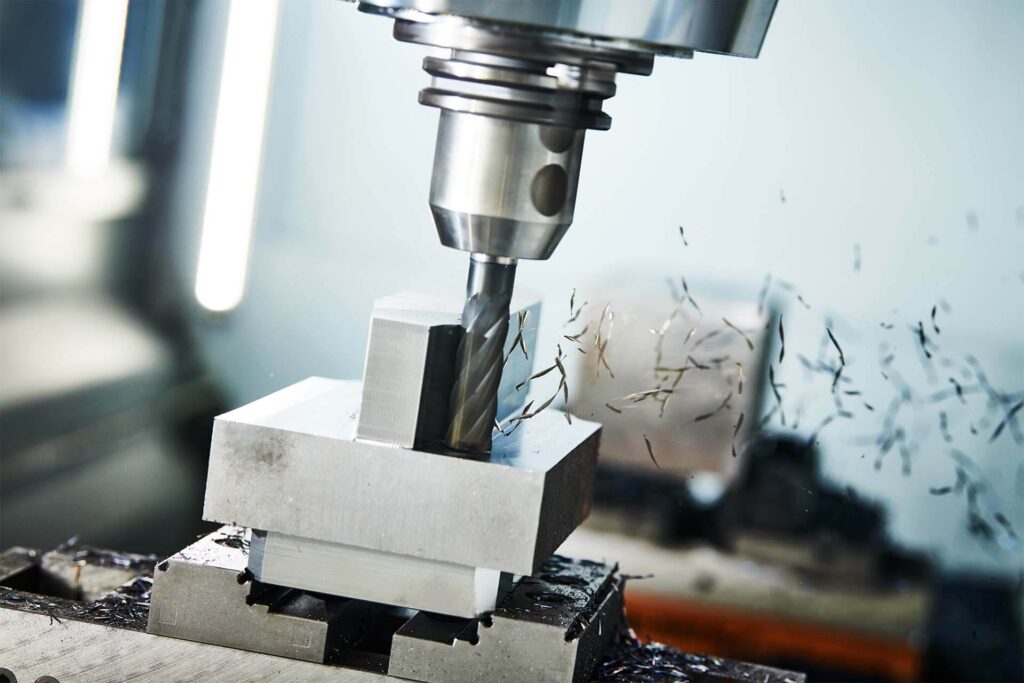
Another important aspect of high speed cutting is the use of coolant or lubricant. The high cutting speeds generate a significant amount of heat, which can lead to thermal damage to the workpiece and the cutting tool. Coolant or lubricant is used to dissipate this heat and reduce the risk of thermal damage. It also helps in chip evacuation, preventing the chips from interfering with the cutting process.
In addition to tool selection and the use of coolant or lubricant, the stability of the machining process is also crucial in high-speed cutting. This is because an increase in cutting speed can cause vibration and chatter, which can negatively impact the surface finish and dimensional accuracy of the workpiece. So to ensure stability, a rigid machine setup, correct tool holder design and an effective damping system are important. In addition, stability can be further enhanced and machining performance improved using advanced cutting strategies such as trochoidal milling or high-speed peel milling.
High speed cutting offers several advantages over conventional machining processes. Firstly, it allows for faster material removal rates, resulting in reduced cycle times and increased productivity. Secondly, it can improve surface finish and dimensional accuracy, as the high cutting speeds minimize the occurrence of built-up edge and work hardening. Lastly, high-speed cutting can also lead to longer tool life, as the reduced cutting forces and optimized tool geometry result in less tool wear.
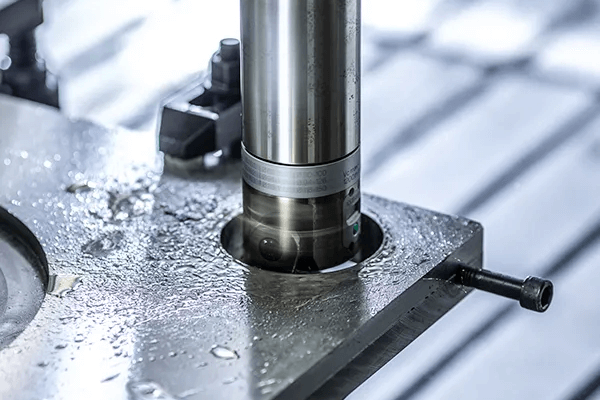
In conclusion, high speed cutting is a machining process that involves the removal of material at high cutting speeds. It requires the selection of appropriate cutting tools, the use of coolant or lubricant, and the maintenance of stability during the machining process. High-speed cutting offers several advantages, including increased productivity, improved surface finish, and longer tool life. By understanding the basics of high-speed cutting and implementing the necessary measures, manufacturers can achieve efficient and precise machining operations.