Understanding Tool Deformation in CNC Machining
CNC machining is a widely used manufacturing process that involves the use of computer-controlled machines to shape and cut a variety of materials. One of the key challenges of CNC machining is tool deformation, which can have a significant impact on the quality and accuracy of the final product. Aeg washing machine parts, arcade machine parts, archway doner machine parts and beko parts washing machine are particularly careful in this regard when machining.
In this article, we will explore the causes of tool deformation and discuss some strategies to minimize its effects when machining parts such as Aeg washing machine parts, arcade machine parts, archway doner machine parts and beko parts washing machine.
Tool deformation refers to the changes in shape and dimensions that occur in cutting tools during the CNC machining process. This deformation can be caused by a variety of factors, including the cutting forces exerted on the tool, the temperature generated during cutting, and the material properties of the tool itself. Understanding these factors is crucial for optimizing the machining process and ensuring the desired outcome.
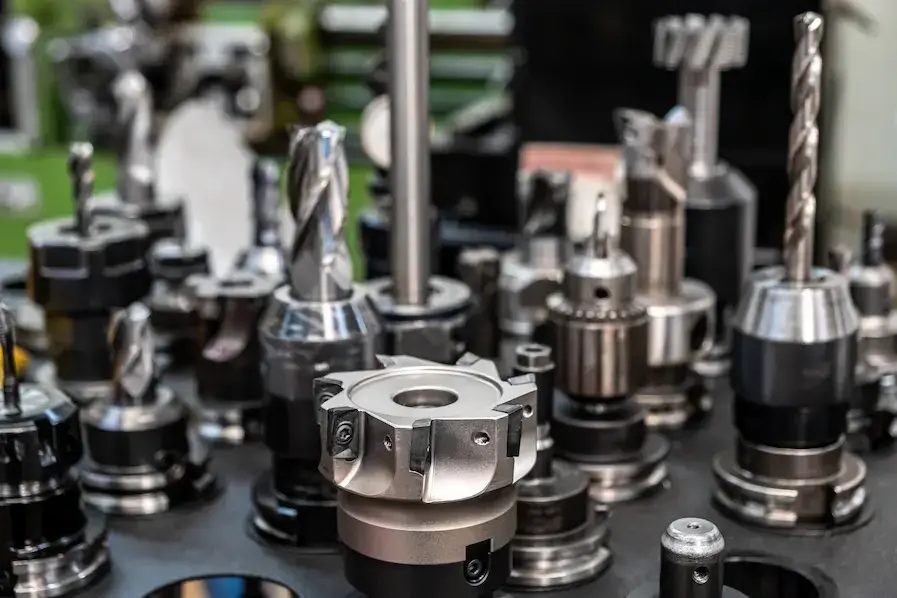
One of the main causes of tool deformation is the cutting forces acting on the tool during CNC machining. Because these forces can be very strong, especially when machining hard materials or removing large amounts of material. So when the tool cuts the workpiece, it bends and deflects due to compressive and tensile forces. Ultimately, this bending can lead to dimensional inaccuracies and a poor surface finish.
Another factor that causes tool deformation is the temperature generated during the cutting process. This is because the heat generated by the friction between the tool and the workpiece causes the tool to expand, causing thermal deformation. This expansion will further aggravate the bending and deflection of the tool, resulting in greater dimensional errors. Additionally, high temperatures can cause tool materials to soften or even melt, reducing their overall strength and durability.
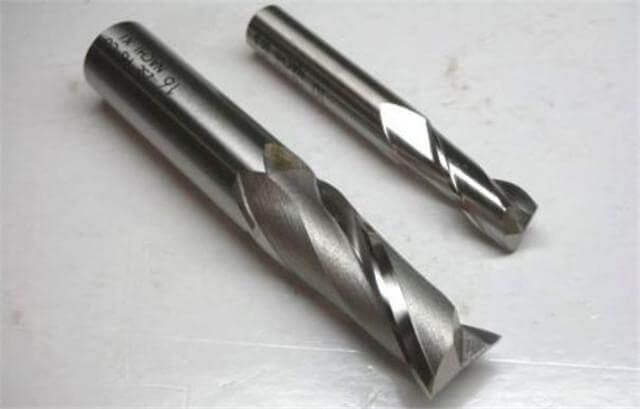
The material properties of the tool itself also play a significant role in tool deformation. Different tool materials have different levels of hardness, strength, and thermal conductivity, which can affect their resistance to deformation. For example, tools made from high-speed steel are generally more resistant to deformation than those made from carbide. However, high-speed steel tools may not be suitable for machining certain materials, such as stainless steel or titanium, which require the use of more specialized tool materials.
To minimize tool deformation and ensure accurate machining, several strategies can be employed. One approach is to select the appropriate tool material for the specific machining operation. This involves considering factors such as the material being machined, the cutting forces involved, and the desired surface finish. By choosing a tool material with the right combination of hardness, strength, and thermal conductivity, the risk of deformation can be significantly reduced.
Another strategy is to optimize the cutting parameters, such as the cutting speed, feed rate, and depth of cut. By carefully adjusting these parameters, it is possible to minimize the cutting forces and the heat generated during machining, thereby reducing the risk of tool deformation. Additionally, using coolant or lubricant during cutting can help dissipate the heat and improve the overall machining performance.
In conclusion, tool deformation is a common challenge in CNC machining that can affect the quality and accuracy of the final product. Understanding the causes of tool deformation, such as cutting forces, temperature, and tool material properties, is essential for minimizing its effects. By selecting the appropriate tool material, optimizing cutting parameters, and using coolant or lubricant, the risk of tool deformation can be effectively managed. Ultimately, by addressing tool deformation, manufacturers can achieve higher precision and better quality in their CNC machining processes.