Benefits of CNC Aluminum Prototyping
CNC aluminum prototyping is becoming increasingly popular across industries due to its many benefits. These include parts in beko washing machine parts diagram, blade beer machine spare parts, brother sewing machine parts uk and brother sewing machine replacement parts.
This quick guide aims to clarify the benefits of using CNC aluminum prototypes in projects such as parts in beko washing machine parts diagram, blade beer machine spare parts, brother sewing machine parts uk and brother sewing machine replacement parts.
Key Benefits of CNC Aluminum Prototyping
One of the primary benefits of CNC aluminum prototyping is its exceptional strength and durability. Aluminum is known for its high strength-to-weight ratio, making it an ideal material for creating prototypes that need to withstand rigorous testing and real-world conditions. Whether you are developing a new automotive component or a complex aerospace part, CNC aluminum prototyping ensures that your design can handle the demands of the application.
Another advantage of CNC aluminum prototyping is its excellent corrosion resistance. Aluminum naturally forms a protective oxide layer when exposed to air, which prevents further oxidation and corrosion. This inherent property makes CNC aluminum prototypes suitable for applications in harsh environments, such as marine or outdoor settings. By choosing CNC aluminum prototyping, you can ensure that your prototypes will maintain their integrity and functionality over time.
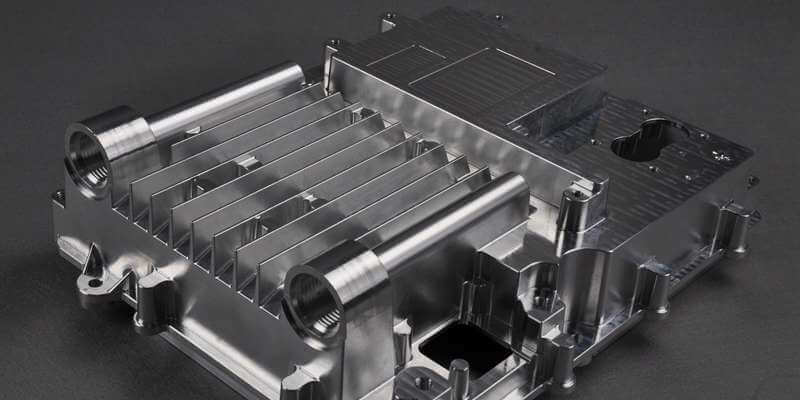
Furthermore, the process offers excellent precision and accuracy. Computer Numerical Control (CNC) machines are capable of achieving incredibly tight tolerances, allowing for the creation of intricate and complex designs. This level of precision is crucial, especially in industries where even the slightest deviation can lead to catastrophic consequences. With CNC aluminum prototyping, you can have confidence in the accuracy of your prototypes, ensuring that they meet your exact specifications.
In addition to precision, CNC aluminum prototyping also offers versatility. Aluminum is an extremely ductile material that is easy to process and manufacture. Therefore, CNC machines can easily shape aluminum into various geometric shapes, making it widely used. And, whether you need prototypes with intricate details or large assemblies, CNC aluminum prototypes can fit the bill.
Furthermore, the process offers a cost-effective solution for product development. Compared to traditional manufacturing methods, such as injection molding or casting, CNC aluminum prototyping requires minimal setup time and tooling costs. This means that you can quickly iterate and refine your designs without incurring significant expenses. Additionally, CNC machines can produce prototypes in a relatively short amount of time, allowing for faster product development cycles.

Finally, the process can be easily customized and modified. As your design evolves, you may need to make adjustments or incorporate new features. With CNC aluminum prototyping, these changes can be implemented quickly and efficiently. CNC machines can easily reprogrammed to accommodate design modifications, eliminating the need for costly and time-consuming tooling changes.
In conclusion, CNC aluminum prototyping offers a multitude of benefits for various industries. Its exceptional strength, corrosion resistance, precision, versatility, cost-effectiveness, and ease of customization make it an attractive choice for prototyping. By utilizing CNC aluminum prototyping, you can ensure that your prototypes meet the highest standards of quality and functionality, ultimately leading to successful product development.