The Basics of CNC Machining for Brass Parts
CNC machining has revolutionized the manufacturing industry, making the production of a wide variety of parts precise and efficient. One of the most common materials that is machined using CNC machines is brass. Brass is a versatile alloy known for its excellent machinability and aesthetics.
In this article, we will explore the basics of CNC machining of brass parts, including the benefits, considerations, and best practices.
1.Advantages of CNC Machining of Brass Parts
1) High Precision
One of the main advantages of machining brass parts using CNC machines is the high precision that can be achieved. CNC machines are computer controlled, which means that they can follow complex instructions with the utmost accuracy.
This is especially important when working with brass, as it is a relatively soft material that requires careful handling to avoid any damage or deformation. With CNC machining, you can ensure that your brass parts are machined to precise specifications for a perfect fit and optimal functionality.
2) Fast and Efficient Machining
Another advantage of CNC machining brass parts is that it can be done quickly and efficiently. CNC machines are able to perform multiple operations simultaneously, such as drilling, milling, and turning. This means you can produce brass parts in a fraction of the time compared to traditional machining methods.
In addition, CNC machines can be programmed to run continuously, allowing for uninterrupted production and increased throughput. This is particularly beneficial for large-scale manufacturing operations that require large quantities of brass parts.

2.Considerations for CNC machining of brass parts
When machining brass parts using CNC machines, there are several things to keep in mind.
1) Selecting the right cutting tool and machining parameters
Brass is a relatively soft material, which means it is easy to machine. However, it is also prone to wear and work hardening if not machined properly. Therefore, it is critical to use sharp cutting tools with appropriate geometry and coatings to minimize friction and heat generation.
In addition, optimizing cutting speeds, feed rates, and depth of cut can help prevent work hardening and ensure a smooth machining process.
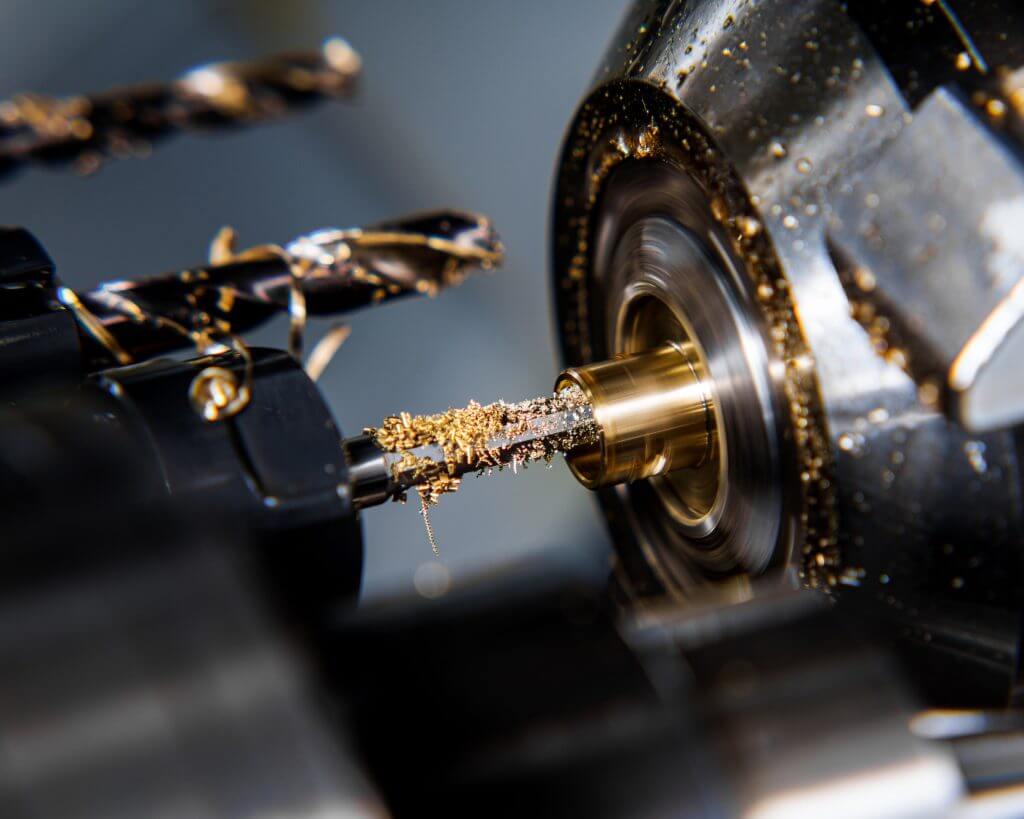
2) Choice of coolant or lubricant
Another issue to consider when machining brass parts is the choice of coolant or lubricant. Although brass has excellent thermal conductivity, it is still important to use the right coolant or lubricant to dissipate heat and reduce friction during machining.
This helps extend the life of the cutting tool and improve the surface finish of the brass part. It is recommended to use a water-soluble coolant or lubricant specifically formulated for machining brass for best results.
3.Practices for CNC Machining of Brass Parts
In terms of best practices, it is critical to properly secure the brass parts during machining to prevent any movement or vibration. This step can be accomplished by using clamps, fixtures, or vises that provide a stable and sturdy setup.
Additionally, regular inspection and maintenance of CNC machines and cutting tools is essential to ensure optimal performance and accuracy. This step includes checking for any signs of wear or damage and that machine parts are cleaned and lubricated as recommended by the manufacturer.
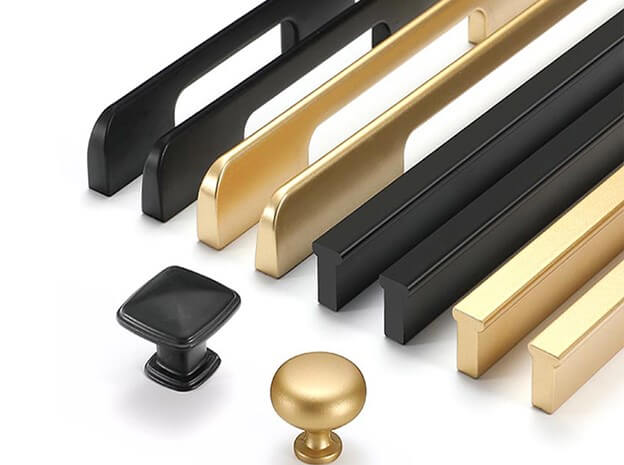
In summary, CNC machining is an excellent way to produce brass parts accurately and efficiently. By understanding the benefits, considerations, and best practices for machining brass with CNC machines, you can optimize your process and achieve high-quality results.
Whether you are manufacturing small components or large-scale production, CNC machining offers a reliable and cost-effective solution for machining brass parts.