The Evolution of Wire-Cut Machining in Auto Parts Manufacturing
In the world of auto parts manufacturing, precision and efficiency are paramount. As technology has advanced, so too have the methods used to create these vital components. One such method that has become a dominant force in the industry is wire-cut machining. This article will explore the evolution of wire-cut machining in auto parts manufacturing, from its humble beginnings to its current status as a go-to technology.
Wire-cut machining, also known as electrical discharge machining (EDM), was first developed in the 1940s as a way to shape hardened steel. At the time, traditional machining methods struggled to work with this tough material, leading to slow production times and high costs. Wire-cut machining offered a solution by using electrical sparks to erode the steel, allowing for precise and efficient shaping.
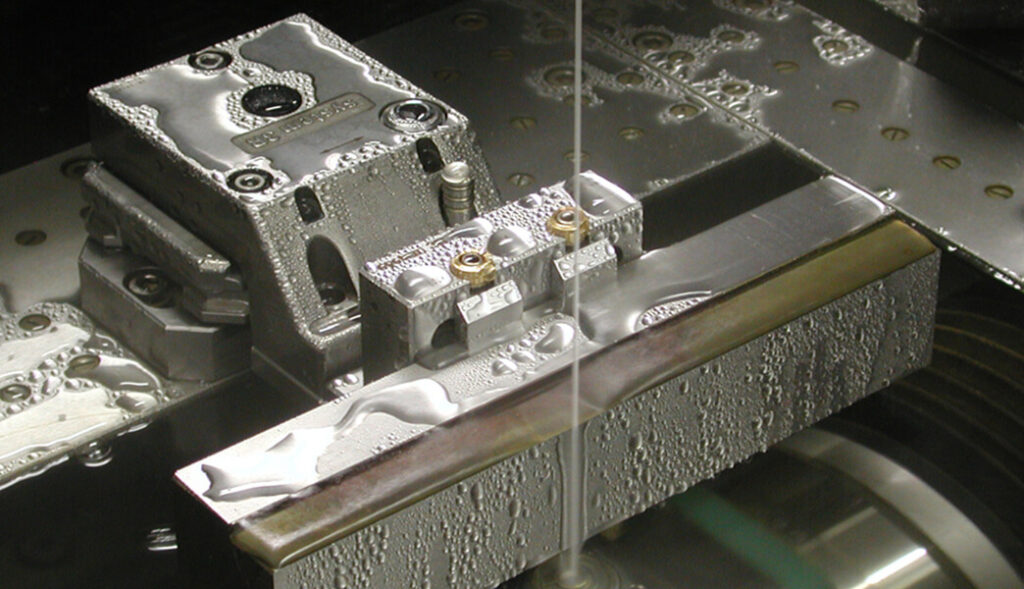
In the early days, wire-cut machining was a slow and labor-intensive process. The wires used to generate the discharge must be passed manually through the workpiece, so this is a very time-consuming task. However, as technology continues to advance, the capabilities of wire cutting machines continue to improve. The introduction of an automatic threading system not only eliminates the need for manual intervention but also significantly speeds up the process.
Another major advancement in wire-cut machining came with the introduction of computer numerical control (CNC) technology. This allowed for greater precision and control over the machining process, as well as the ability to program complex shapes and patterns. With CNC wire cut machines, auto parts manufacturers could produce intricate components with ease, meeting the ever-increasing demands of the industry.
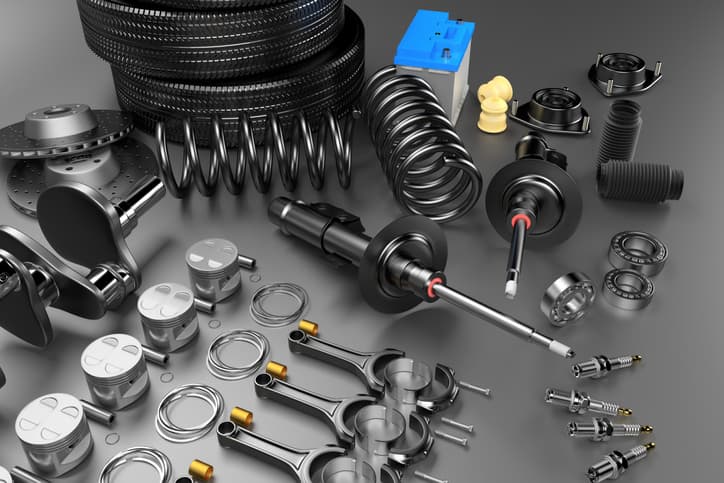
As wire-cut machining continued to evolve, so did the materials it could work with. Initially limited to hardened steel, advancements in EDM technology allowed for the machining of a wide range of materials, including aluminum, titanium, and even exotic alloys. This opened up new possibilities for auto parts manufacturers, who could now create lightweight and durable components that were previously unattainable.
In addition to its versatility, wire cut machining also offered significant cost savings for auto parts manufacturers. Traditional machining methods often resulted in a significant amount of material waste, as excess material had to be removed to achieve the desired shape. Wire cut machining, on the other hand, is a non-contact process, meaning there is no physical contact between the tool and the workpiece. This eliminates the need for material removal, resulting in minimal waste and lower production costs.
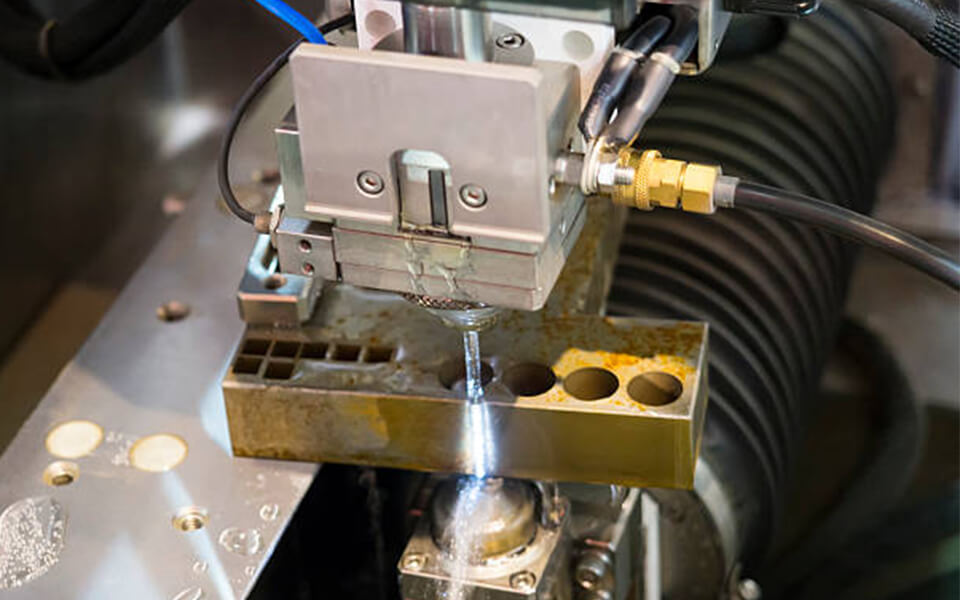
Today, wire-cut machining has become a dominant technology in auto parts manufacturing. Its precision, efficiency, and versatility make it an ideal choice for producing complex components with tight tolerances. From engine parts to transmission components, wire-cut machining plays a crucial role in the production of high-quality auto parts.
In conclusion, the evolution of wire-cut machining in auto parts manufacturing has been a remarkable journey. From its humble beginnings as a solution for shaping hardened steel to its current status as a dominant force in the industry, wire-cut machining has revolutionized the way auto parts are produced. With its precision, efficiency, and cost savings, it is no wonder that wire-cut machining has become the go-to technology for auto parts manufacturers worldwide.