Introduction to Electrical Discharge Machining (EDM)
Electrical discharge machining (EDM) is a widely used manufacturing process that involves the use of electrical sparks to remove material from a workpiece. The process is commonly used in industries such as aerospace, automotive, and medical, where precision and accuracy are critical. It is equally effective when faced with espresso machine parts, ice cream machine parts, parts for sewing machines, and parts of an elliptical machine.
In this article, we will discuss the anatomy and working principles of EDM to gain a comprehensive understanding of this fascinating technology.
At its core, electrical discharge machining consists of three main components: the power supply, the electrode, and the workpiece. The power supply generates a high-frequency electrical discharge, which is then directed towards the workpiece through the electrode. The workpiece, typically made of conductive materials such as steel or aluminum, is positioned in close proximity to the electrode. As the electrical discharge occurs, tiny sparks are generated, causing the material to erode from the workpiece.
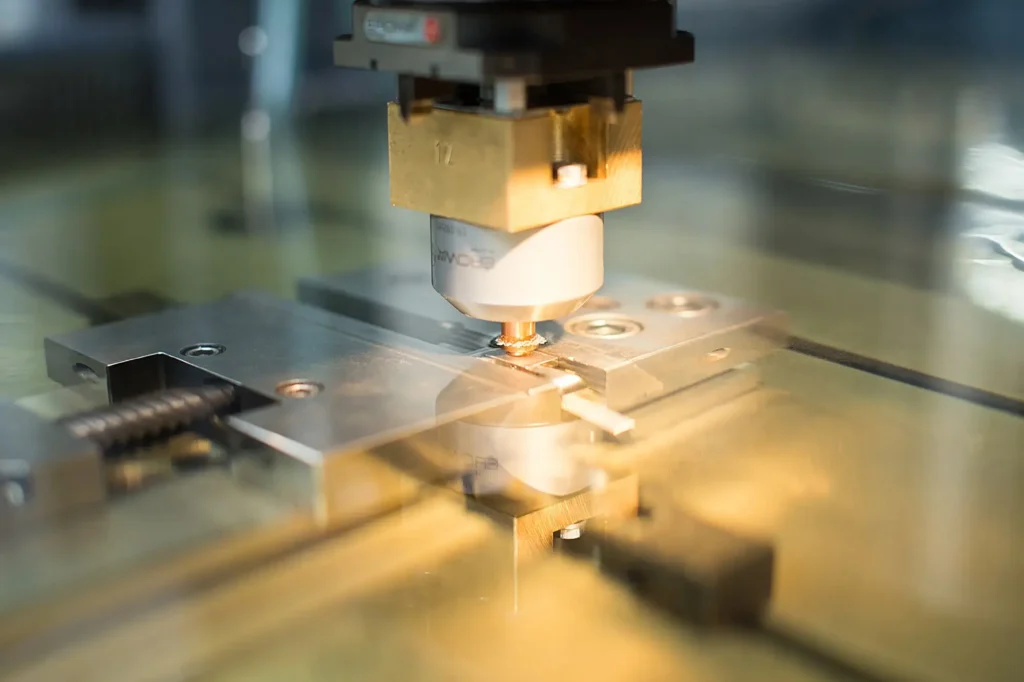
The working principles of electrical discharge machining can be explained by the phenomenon of electrical discharge. When a voltage is applied between the electrode and the workpiece, a spark is created due to the difference in electrical potential. This spark generates intense heat, melting and vaporizing the material in its path. The molten material is then flushed away by a dielectric fluid, which also acts as a coolant, preventing the workpiece from overheating.
One of the key advantages of electrical discharge machining is its ability to machine complex shapes and intricate details that are difficult to achieve using conventional machining methods. This is due to the fact that EDM does not rely on physical contact between the electrode and the workpiece. Instead, the electrical discharge erodes the material, allowing for precise and intricate cuts. Additionally, EDM can be used to machine materials that are considered difficult to machine, such as hardened steel or exotic alloys.
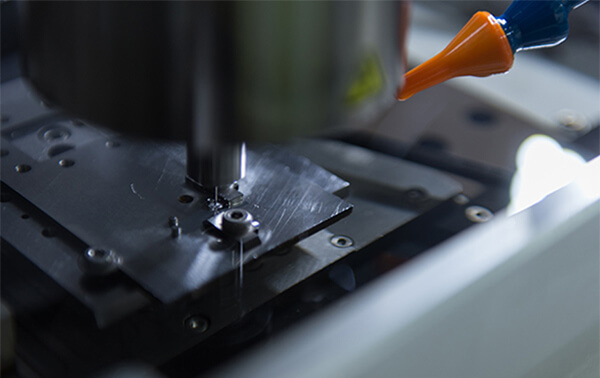
There are two main types of electrical discharge machining: sinker EDM and wire EDM. Sinker EDM, also known as ram EDM or conventional EDM, uses a specially shaped electrode to create a cavity in the workpiece. This process is commonly used for creating molds and dies. On the other hand, wire EDM uses a thin, electrically conductive wire as the electrode. The wire is guided through the workpiece, creating a cut along the desired path. This method is often used for cutting intricate shapes and contours.
In order to achieve optimal results, several factors must be considered when using electrical discharge machining. For example, the choice of dielectric fluid can greatly affect the machining process. Because while dielectric fluids act as coolants and wash away eroded material, they also help prevent sparks from forming and maintain a stable discharge. In addition, the choice of electrode material and its shape also affects the accuracy and efficiency of the machining process.
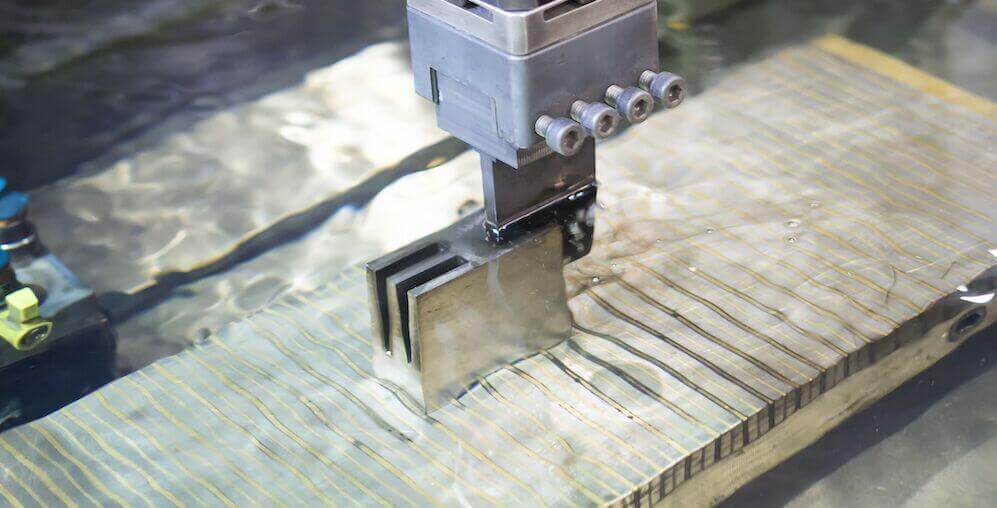
In summary, electrical discharge machining (EDM) is a versatile and precise manufacturing process that is widely used in various industries, including but not limited to espresso machine parts, ice cream machine parts, parts for sewing machines, and parts of an elliptical machine. By harnessing the power of electrical discharges, EDM allows for the machining of complex shapes and difficult-to-machine materials. Understanding the structure and working principles of EDM is crucial for achieving optimal results and harnessing the full potential of this remarkable technology.