Key Parameters for CNC Machining Quality Inspection
CNC machining has become an integral part of modern manufacturing processes, enabling precise and efficient production of complex parts. However, ensuring the quality of these machined parts is essential to avoid costly mistakes and maintain customer satisfaction. Parts companies such as manufacturer of metal parts marking machines and liberty diesel machines & spare parts trading co.llc prioritize quality.
Quality inspection plays a vital role in this process as it helps companies like manufacturer of metal parts marking machines and liberty diesel machines & spare parts trading co.llc to identify any deviations from the required specifications and ensure that the final product meets the required standards. In this article, we will discuss some of the key parameters for CNC machining quality inspection.
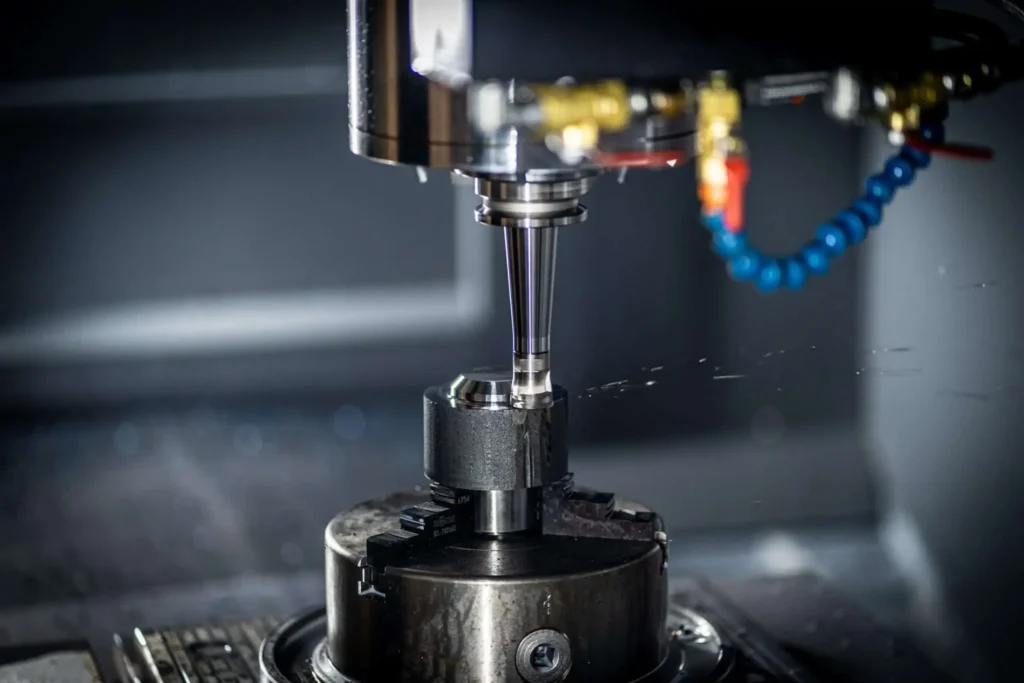
First and foremost, dimensional accuracy is a critical aspect of CNC machining quality inspection. This parameter refers to the degree of conformity between the actual dimensions of the machined part and the specified dimensions. Any deviation from the desired measurements can lead to functional issues or assembly problems. To ensure dimensional accuracy, precision measuring tools such as calipers, micrometers, and coordinate measuring machines (CMMs) are used to compare the actual dimensions with the CAD model or engineering drawings.
Surface finish is another important parameter that needs to be inspected during CNC machining. The surface finish of a part determines its appearance, functionality, and performance. It is crucial to achieve the desired surface finish to meet the requirements of the application. Common surface finish inspection methods include visual inspection, roughness measurement using profilometers, and surface roughness testers. These tools help identify any surface defects, such as scratches, burrs, or unevenness, which can affect the overall quality of the part.
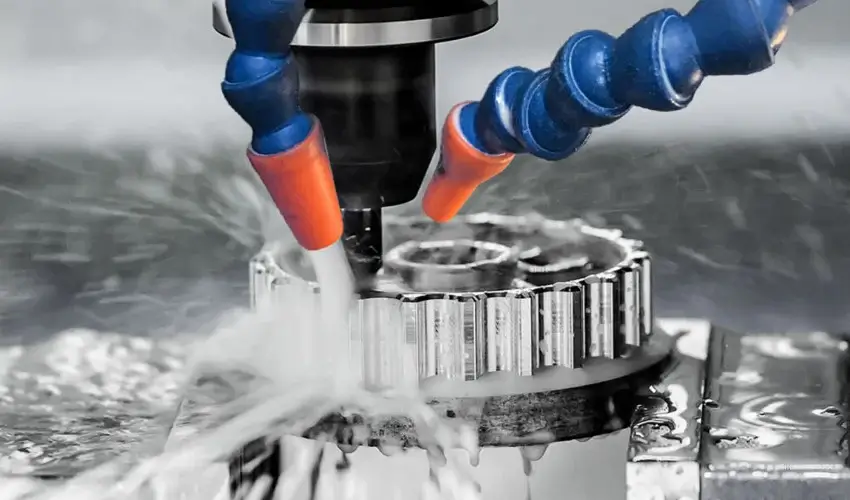
Tolerance is a key parameter that determines the allowable variation in the dimensions of machined parts. Therefore, tolerances on critical dimensions must be checked to ensure that they fall within the specified range. Tolerance checking, on the other hand, involves comparing the actual dimensions to the tolerance limits specified in the engineering drawings. Dimensions outside the tolerance limit indicate a deviation from the required specification and require corrective action to ensure smooth machining.
In addition to dimensional accuracy, surface finish, and tolerance, material properties also play a crucial role in CNC machining quality inspection. The material used for machining should possess the desired mechanical, thermal, and chemical properties to meet the functional requirements of the part. Material inspection involves verifying the material composition, hardness, strength, and other relevant properties. Various testing methods, such as spectroscopy, hardness testing, and tensile testing, are employed to ensure the quality of the material.
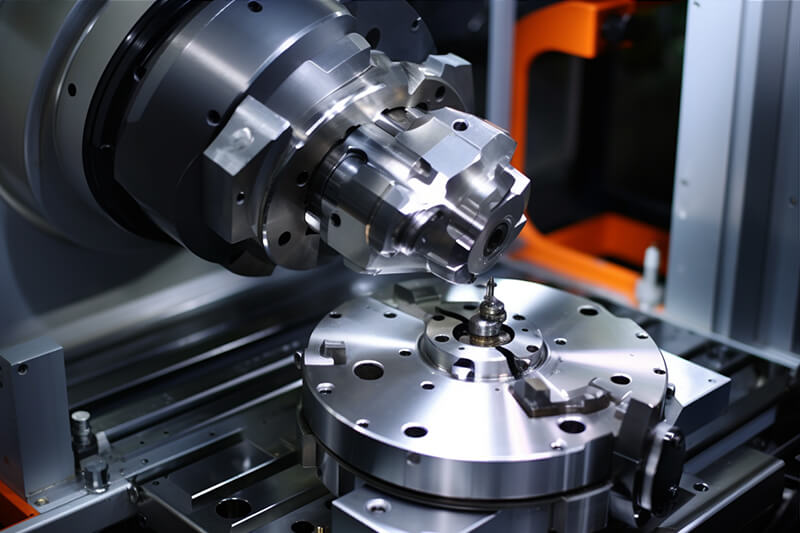
Furthermore, it is essential to inspect the overall functionality and performance of the machined part. This involves conducting functional tests to verify that the part performs as intended under real-world conditions. Functional tests may include load testing, pressure testing, or endurance testing, depending on the application. These tests help identify any issues related to the part’s functionality, such as leaks, failures, or inadequate performance.
In conclusion, CNC machining quality inspection is a critical step in ensuring the overall quality of machined parts. Key parameters such as dimensional accuracy, surface finish, tolerance, material properties, and functionality need to be thoroughly inspected to meet the desired specifications. By employing precision measuring tools, inspection methods, and functional tests, manufacturers can identify any deviations or defects and take corrective actions to maintain the highest quality standards. Ultimately, a comprehensive quality inspection process is essential for delivering reliable and high-quality machined parts to customers.