Preventing Corrosion: How to Avoid Metal Parts’ Natural Enemies
Corrosion is a natural process that occurs when metal reacts with its environment, causing it to deteriorate. It is a common problem that affects industries ranging from manufacturing to construction. However, with the right corrosion prevention techniques, the life of metal components can be significantly extended, saving time and money.
1.Common Types of Corrosion
The first step in preventing corrosion is to understand the different types of corrosion that can occur.
1) Uniform Corrosion
The most common type of corrosion is uniform corrosion, which occurs when the entire surface of a metal is exposed to a corrosive environment. This type of corrosion can be prevented by applying a protective coating such as paint or corrosion-resistant metal alloys.
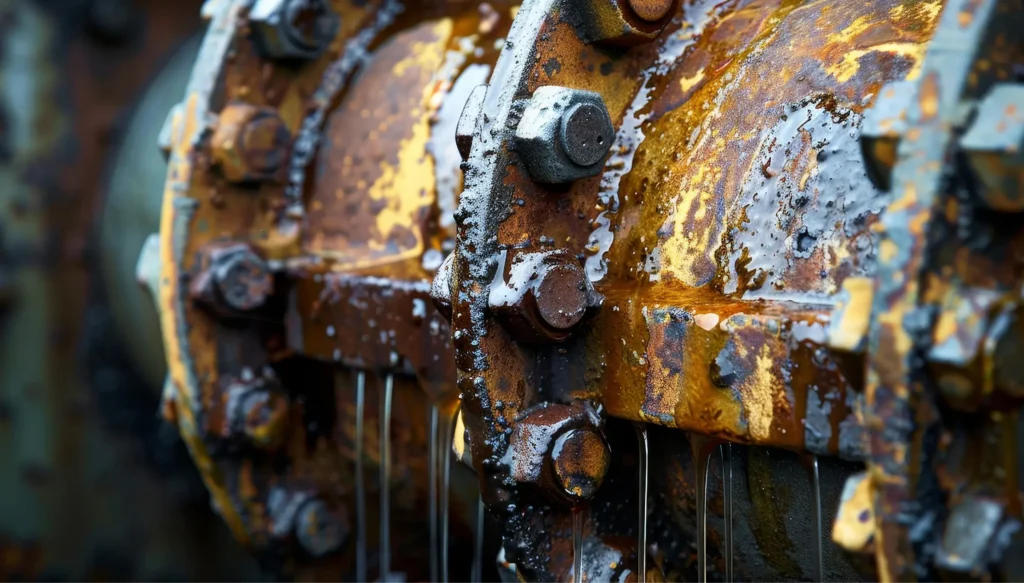
2) Localized Corrosion
Another type of corrosion is localized corrosion, which occurs in specific areas of a metal surface. Examples of localized corrosion include pitting and crevice corrosion. Pitting is characterized by small holes or pits on the metal surface, while crevice corrosion occurs in small spaces or crevices between metal components. To prevent localized corrosion, it is important to ensure proper design and construction as well as regular inspection and maintenance.
2.Methods of preventing corrosion
1) Use of protective coatings
These coatings act as a barrier between the metal surface and the corrosive environment, preventing direct contact and reducing the risk of corrosion. Common types of protective coatings include paint, epoxy, and galvanizing. The choice of coating depends on factors such as the type of metal, the environment, and the expected life of the metal part.
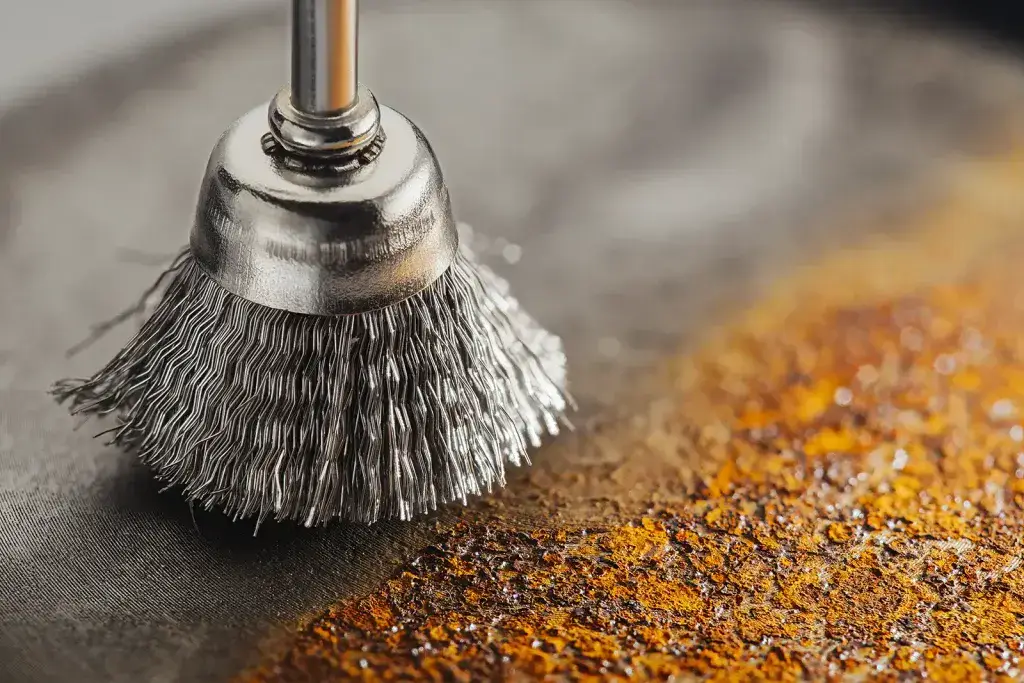
2) Cathodic Protection
In addition to protective coatings, another important aspect of preventing corrosion is cathodic protection. Cathodic protection is a technique that uses sacrificial anodes or impressed currents to protect metals from corrosion. Sacrificial anodes are made of more reactive metals, such as zinc or magnesium, which corrode in place of the protected metal.
Impressed current systems, on the other hand, use an external power source to provide a protective current to the metal surface. Cathodic protection is often used in underground pipelines, offshore structures, and marine environments.
3) Regular Inspection and Maintenance
The risk of extensive damage can be minimized by identifying and addressing potential corrosion issues early. Inspection techniques include visual inspection, nondestructive testing, and corrosion monitoring.
Regular cleaning and maintenance, such as removing dirt and debris, can also help prevent corrosion by reducing the likelihood of moisture and corrosive materials accumulating on metal surfaces.
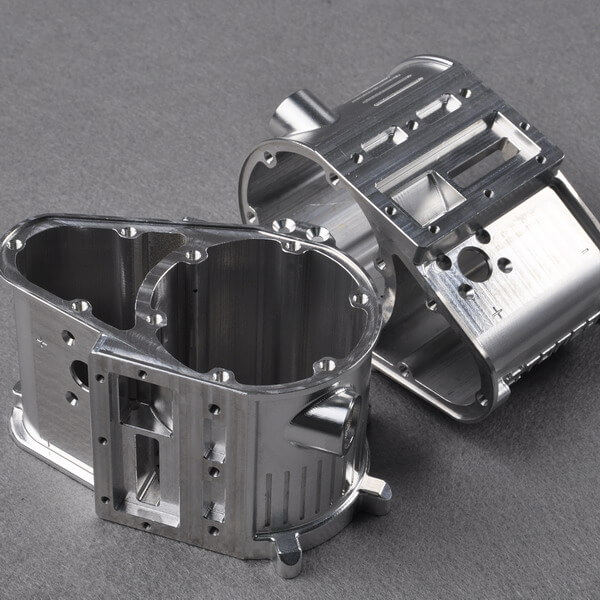
In summary, understanding the basics of preventing corrosion is essential to extending the service life of metal parts. By identifying different types of corrosion and implementing appropriate prevention techniques, such as protective coatings and cathodic protection, the risk of corrosion can be greatly reduced. Regular inspections and maintenance are also important to identify and address potential corrosion issues before they escalate.
By taking proactive measures, industries can avoid the natural enemies of metal components and ensure their longevity and performance.