Importance of Grinding Parameters for Surface Finish Enhancement
Grinding is a critical process that cannot be ignored in order to achieve a high-quality surface finish. The surface finish of a part not only affects its appearance but also plays an important role in its functionality. Singer sewing machine parts, top loading washing machine parts, toyota sewing machine parts and vintage singer sewing machine parts are some of the parts that have good grinding processes.
Therefore, it is crucial to understand the importance of grinding parameters in improving surface finish.
1.Selection
One of the key factors that influence surface finish is the choice of grinding wheel. Abrasive type, particle size and bond strength all affect the final surface quality. For example, a finer abrasive size will result in a smoother surface, while a coarser abrasive size may leave visible marks. Likewise, abrasive choice affects surface finish. For example, diamond abrasives produce superior surface finishes compared to other materials.
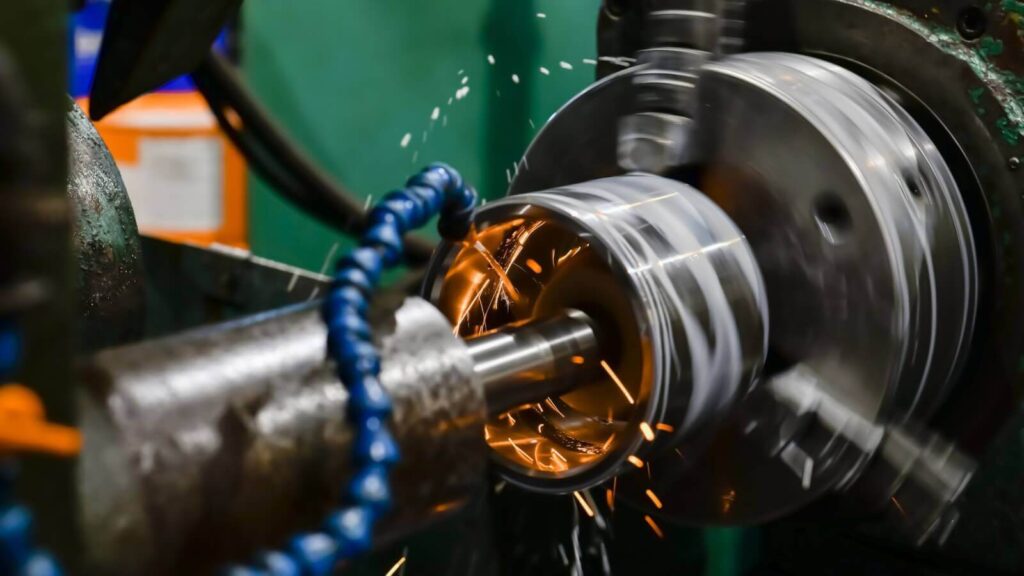
2.Rotation speed
In addition to the grinding wheel, the speed at which the wheel rotates also affects surface finish. Higher wheel speeds tend to generate more heat, resulting in thermal damage and poor surface quality. On the other hand, lower wheel speeds may also result in inadequate material removal and uneven finish.
Therefore, finding the right balance between grinding wheel speed and material removal rate is critical to achieving the desired surface finish.
3.Depth of Cut
Another critical parameter to consider is the depth of cut. The depth of cut refers to the amount of material that is removed with each pass of the grinding wheel. A shallow depth of cut may result in a smoother finish but can also prolong the grinding process. Conversely, a deeper depth of cut can remove material more quickly but may leave behind a rougher surface. Therefore, it is very important to carefully select the cutting depth according to the surface finish and production requirements of the required parts such as singer sewing machine parts, top loading washing machine parts, toyota sewing machine parts and vintage singer sewing machine parts.
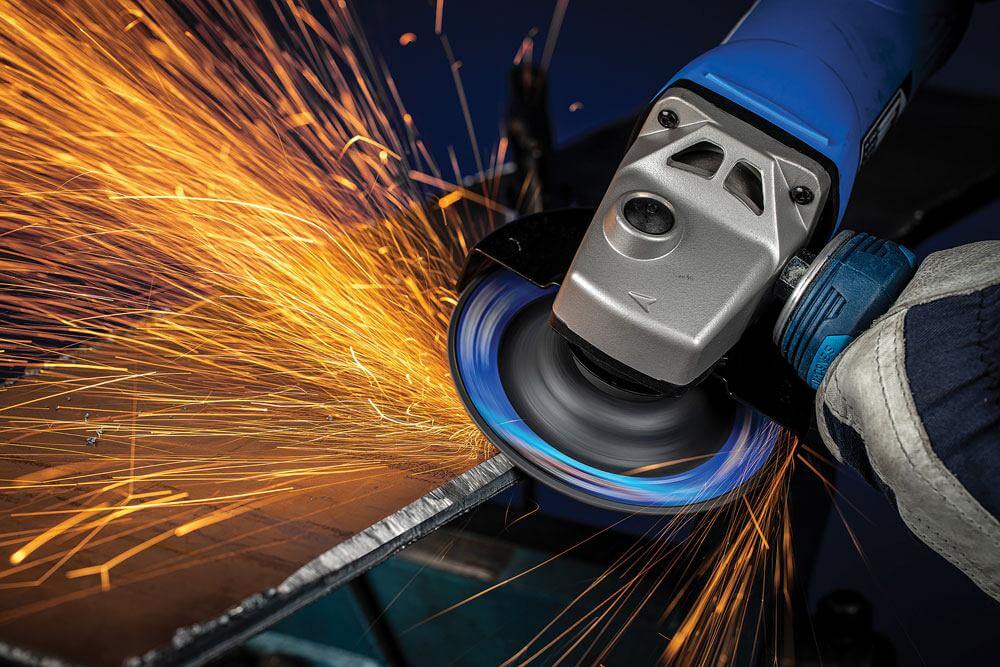
4.Feed Rate
The feed rate, or the speed at which the workpiece is moved across the grinding wheel, is another factor that affects surface finish. A higher feed rate can lead to a rougher finish, as the grinding wheel has less time to remove material. Conversely, a slower feed rate allows for more precise material removal and can result in a smoother surface.
However, it is important to note that excessively slow feed rates can lead to excessive heat generation and potential damage to the workpiece.
5.Coolant Selection and Application
In addition to these parameters, the selection and application of coolant also plays a vital role in achieving a better surface finish. Coolant helps reduce heat generation during the grinding process and also helps remove chips and debris.
The choice of coolant depends on various factors, including the material of the process and the desired surface finish. Proper coolant application, such as through the wheel or flood cooling, is also critical to ensure effective heat dissipation and chip removal.
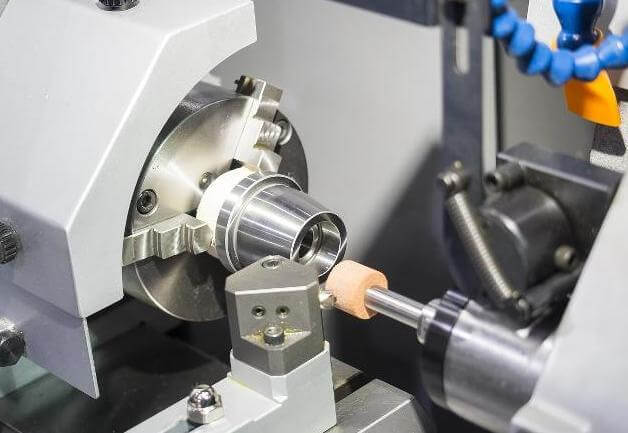
In conclusion, achieving a high-quality surface finish requires careful consideration of various grinding parameters. The choice of grinding wheel, wheel speed, depth of cut, feed rate, and coolant selection all contribute to the final surface quality. By understanding the impact of these parameters and finding the right balance, manufacturers can enhance surface finish and ensure the functionality and aesthetics of their products.