Importance of Surface Finishing in CNC Machining
Surface finishing is a critical aspect of CNC machining that cannot be overlooked. It plays a vital role in enhancing the appearance, functionality, and durability of the final product.
Whether you are manufacturing parts for automotive, aerospace, or any other industry, surface finishing is an essential step that can greatly impact the overall quality of the end result.
1.Aesthetics
One of the main reasons why surface finishing is important in CNC machining is aesthetics. The appearance of a product can significantly affect its marketability and customer perception. A well-finished surface makes a product look professional and sophisticated, making it more attractive to potential buyers. In industries where aesthetics are critical, surface finish can be a determining factor in the success of a product.
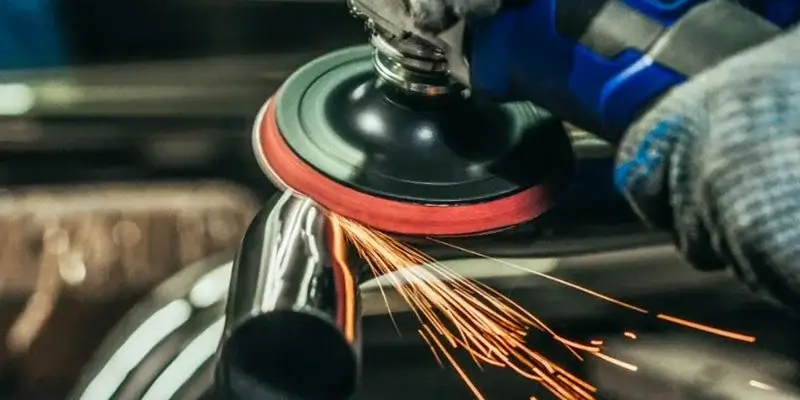
2.Functionality of CNC Machined Parts
Besides aesthetics, surface finishing also plays a vital role in improving the functionality of CNC machined parts. Depending on the application, different surface finishes can be applied to achieve specific functional properties.
For example, a smooth surface finish can reduce friction and wear, making the part more durable and efficient. On the other hand, a textured surface finish can improve grip and enhance the functionality of a part in applications that require a secure grip.
3.Corrosion Resistance of CNC Machined Parts
Surface finishing also has a significant impact on the corrosion resistance of CNC machined parts. By applying a protective coating or treatment, the surface can be made more resistant to environmental factors such as moisture, chemicals, or temperature changes.
This benefit is particularly important in industries where parts are exposed to harsh conditions, such as marine or automotive applications. This is because a finished surface prevents corrosion and degradation, which significantly extends the life of the part.
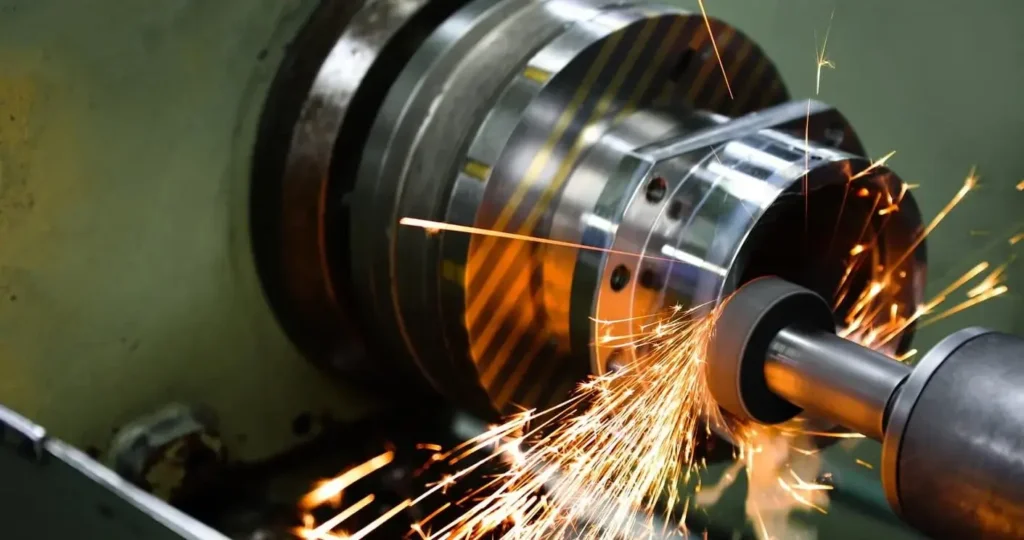
4.Post-processing Requirements for CNC Machined Parts
Depending on the complexity of the part and the required surface finish, additional steps may be required after the machining process. These steps include deburring, polishing, or coating. It is important to carefully plan and consider these post-processing requirements to ensure that the final product meets the required specifications.
5.Cost and Lead Time
Surface finishing can also affect the cost and lead time of a CNC machining project. The complexity and type of surface finish required can affect machining time, tooling requirements, and material selection. Careful evaluation of these factors is important to optimize the manufacturing process and reduce costs.
In addition, surface finishing may require specialized equipment, materials, or expertise, which should be considered when planning a project.
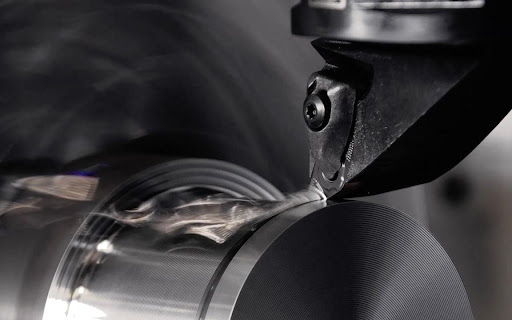
In conclusion, surface treatment is a critical aspect of CNC machining that cannot be overlooked. It plays a vital role in enhancing the appearance, functionality, and durability of the final product. Whether for aesthetics, functionality, corrosion resistance, or post-processing requirements, surface treatment is an essential step that can greatly affect the overall quality of CNC machined parts.
By carefully considering the key factors involved in surface treatment, manufacturers can ensure that their products meet the required specifications and achieve the highest quality levels.