The Basics of Heat Treatment
Heat treatment is a key process used in a variety of industries to alter the properties of metals and alloys. By subjecting these materials to controlled cycles of heating and cooling, their mechanical, physical, and chemical characteristics can be altered to improve their performance. This is equally true for parts in brother sewing machine parts diagram and coffee machine parts diagram.
Understanding the basics of heat treatment is essential for engineers, metallurgists, and manufacturers to ensure that the desired results are achieved.
Heat treatment process:
The first step in heat treatment is heating the material to a specific temperature. This temperature is determined based on the material’s composition and the desired outcome. Heating can be done using various methods, including furnaces, induction heating, and flame heating. The material is heated slowly and uniformly to avoid thermal shock, which can lead to cracking or distortion.
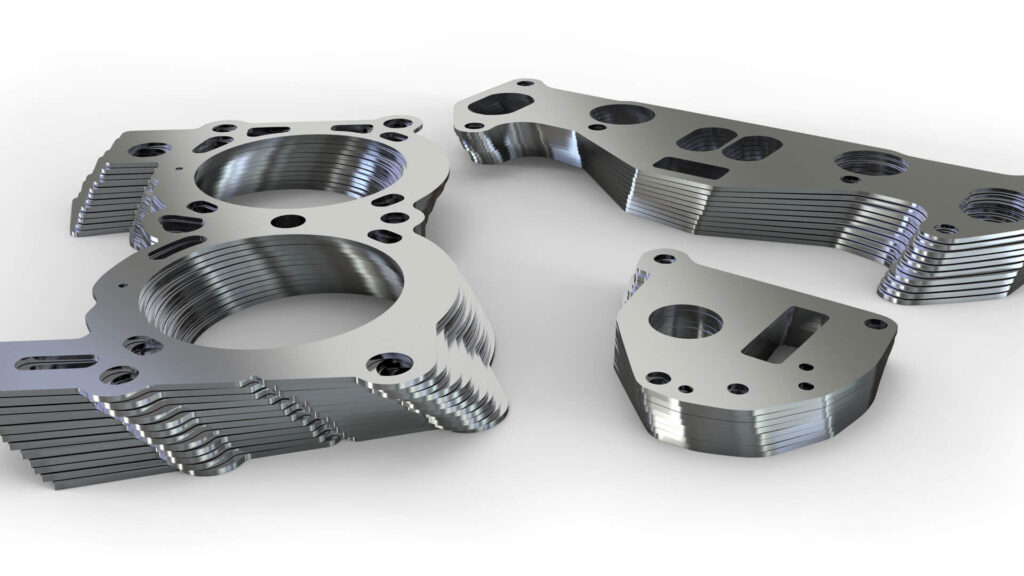
Once the material reaches the desired temperature, it is held at that temperature for a specific period of time, a process called soaking time. This step distributes heat evenly throughout the material, ensuring that all areas reach the desired temperature. Soaking time can also vary depending on the material and its thickness, so it’s crucial to keep the temperature within a narrow range to get the desired results.
After the soaking period, the material is cooled. Moreover, the cooling rate is a key factor in determining the final properties of the material. Different cooling rates can be achieved by different methods such as air cooling, oil quenching or water quenching, the specific choice depends on the material and the desired results. At the same time, rapid cooling (called quenching) also increases hardness, while slower cooling increases toughness.
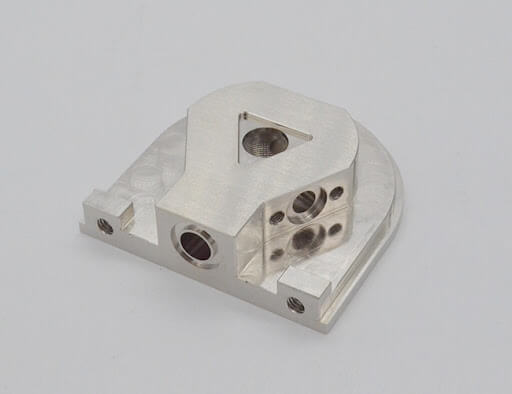
One common heat treatment process is known as annealing. Annealing involves heating the material to a specific temperature and then slowly cooling it down. This process is used to relieve internal stresses, improve machinability, and enhance the material’s ductility. Annealing is often performed after extensive cold working or to prepare the material for further processing.
Another widely used heat treatment process is tempering. Tempering involves reheating the material to a specific temperature below its critical point and then cooling it down. This process is used to reduce the hardness and brittleness that may have been introduced during quenching. Tempering improves the material’s toughness and ductility, making it more suitable for applications that require resistance to impact or vibration.
Hardening is a heat treatment process that involves heating the material to a temperature above its critical point and then rapidly cooling it. This rapid cooling, usually through quenching, results in increased hardness and wear resistance. Hardening is commonly used for tool steels, where high hardness is essential for cutting, shaping, or forming operations.
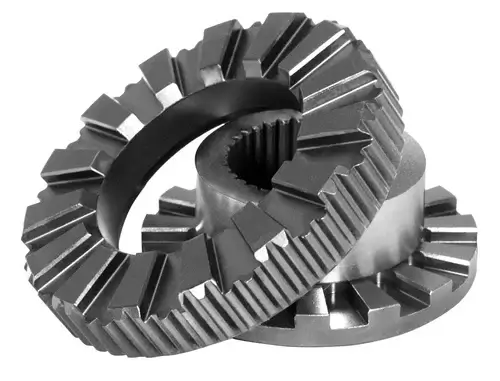
In conclusion, heat treatment is a fundamental process used to modify the properties of metals and alloys. By carefully controlling the heating, soaking, and cooling cycles, engineers and metallurgists can achieve desired outcomes such as increased hardness, improved toughness, or enhanced machinability. Understanding the basics of heat treatment is essential to ensure the successful application of this process in various industries, including parts in brother sewing machine parts diagram and coffee machine parts diagram. Whether it is annealing, tempering, or hardening, each heat treatment process has its unique purpose and can significantly impact the performance of materials.