Optimizing CNC Machining Techniques for Small Aluminum Parts
Aluminum Parts Processing: Common Methods to Solve the Deformation of Aluminum Parts ProcessingCNC machining has revolutionized the manufacturing industry, allowing for precise and efficient production of various components. When it comes to small aluminum parts, finding the most efficient way to machine them is crucial for maximizing productivity and minimizing costs. In this article, we will explore some techniques that can help optimize CNC machining for small aluminum parts.
One of the key factors to consider when machining small aluminum parts is the choice of cutting tools. High-speed steel (HSS) and carbide tools are commonly used in CNC machining, but for aluminum, carbide tools are often preferred due to their superior heat resistance and durability. Carbide tools can withstand the high cutting speeds required for aluminum machining, resulting in faster production rates and longer tool life.
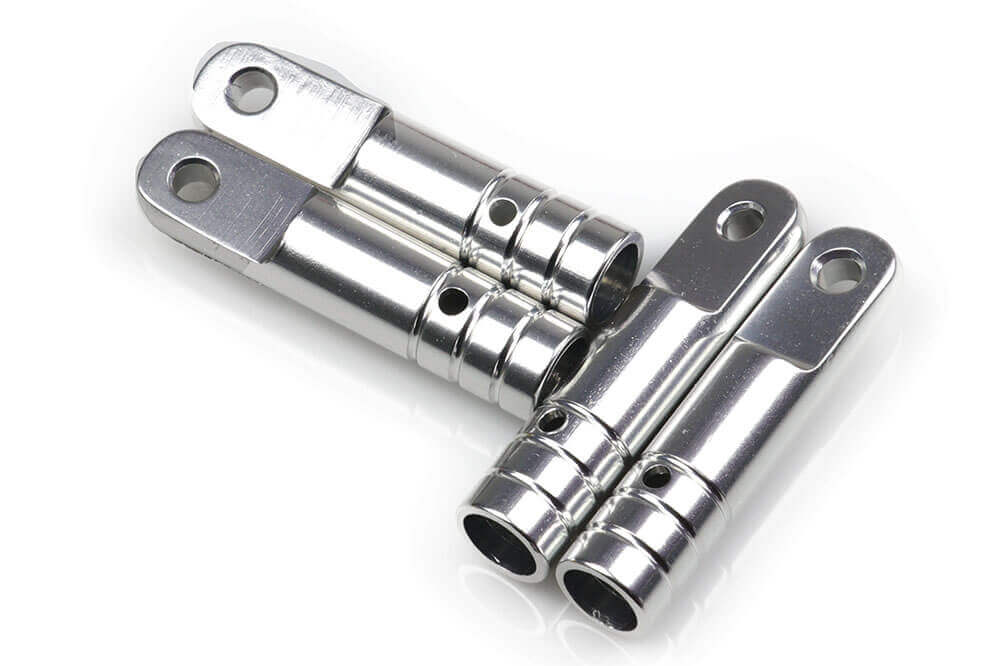
Another important aspect to consider is the selection of cutting parameters. Cutting speed, feed rate, and depth of cut all play a significant role in the efficiency of CNC machining. For small aluminum parts, higher cutting speeds can be used to achieve faster material removal rates. However, it is essential to strike a balance between speed and tool life, as excessive cutting speeds can lead to tool wear and premature failure.
In addition to cutting parameters, coolant selection also affects machining efficiency. Because coolant serves multiple purposes, including lubrication, chip removal, and heat dissipation. For small aluminum parts, water-soluble coolants are usually recommended. Because water-soluble coolants have excellent lubrication and chip evacuation properties, they ensure smooth machining operations. In addition, they effectively dissipate heat and prevent workpieces and cutting tools from overheating.
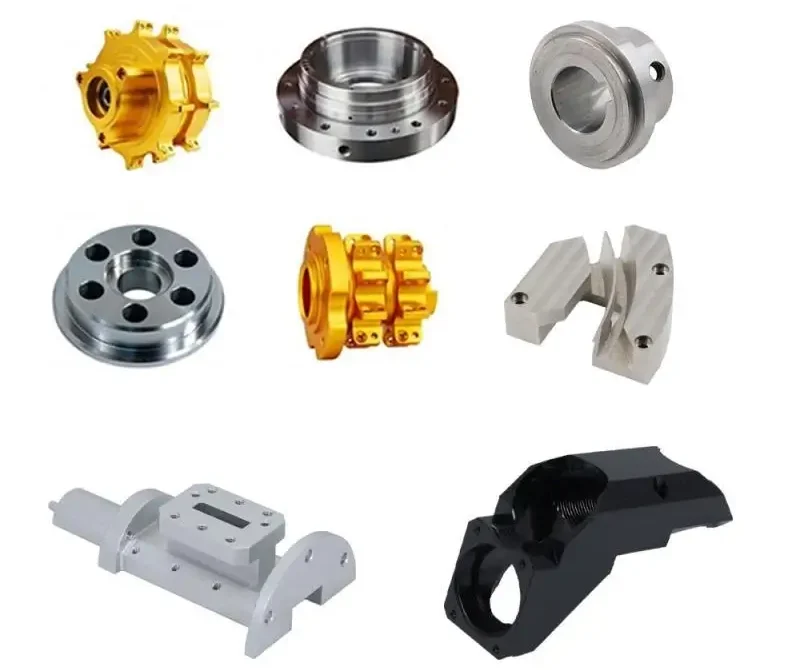
When it comes to fixturing small aluminum parts, precision and stability are crucial. Proper fixturing ensures accurate positioning of the workpiece, minimizing the risk of errors and rework. One effective fixturing technique for small aluminum parts is using soft jaws. Soft jaws are custom-made to match the shape of the workpiece, providing a secure grip without causing any damage. This allows for precise machining without the need for additional clamping devices.
Furthermore, employing advanced machining strategies can significantly enhance efficiency. One such strategy is high-speed machining (HSM), which involves using higher cutting speeds and lighter depths of cut. HSM reduces machining time and improves surface finish, making it ideal for small aluminum parts. Additionally, using trochoidal milling techniques can further optimize machining efficiency. Trochoidal milling involves using circular tool paths, which reduce cutting forces and improve chip evacuation, resulting in faster and more efficient machining.
Lastly, post-processing operations should not be overlooked when aiming for optimal efficiency. Deburring, chamfering, and surface finishing are essential steps to ensure the final product meets the required specifications. Implementing automated post-processing techniques, such as vibratory finishing or tumbling, can save time and labor while achieving consistent and high-quality results.
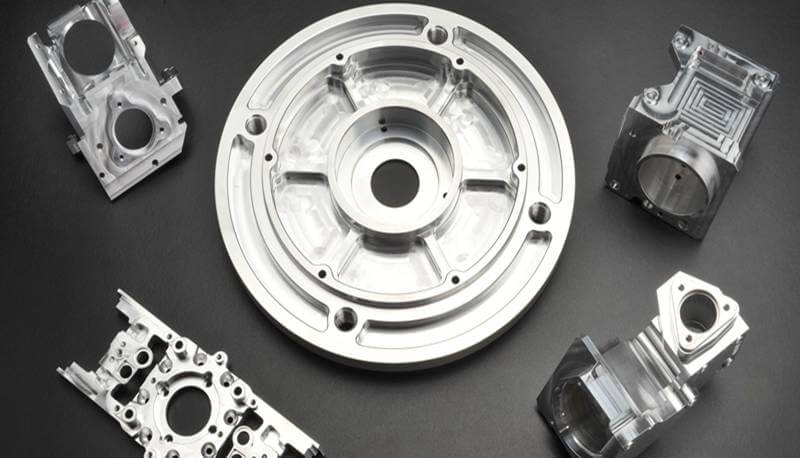
In conclusion, optimizing CNC machining techniques for small aluminum parts requires careful consideration of various factors. Choosing the right cutting tools, selecting appropriate cutting parameters, using suitable coolant, and employing effective fixturing techniques are all essential for maximizing efficiency. Additionally, implementing advanced machining strategies and automating post-processing operations can further enhance productivity. By following these guidelines, manufacturers can achieve the most efficient way to machine small aluminum parts, resulting in improved productivity, reduced costs, and high-quality end products.