Solution to deformation of aluminum parts processing
Aluminum is a widely used material in various industries due to its lightweight, corrosion resistance, and excellent thermal conductivity. However, one common challenge in aluminum parts machining is the occurrence of machining deformation. Machining deformation refers to the distortion or warping of aluminum parts during the machining process. This can lead to dimensional inaccuracies, poor surface finish, and even functional issues in the final product. Understanding the causes of machining deformation in aluminum parts is crucial in order to implement effective solutions.
1.Causes of aluminum part processing deformation
One of the main reasons for the deformation of aluminum parts during processing is the inherent material properties of aluminum itself. Because aluminum has a relatively low melting point and high thermal conductivity, it means that it easily generates and dissipates heat during processing. At the same time, this can also cause thermal expansion and contraction, which can lead to part dimensional changes and warping. In addition, aluminum has a lower elastic modulus, making it more susceptible to elastic deformation under processing forces.
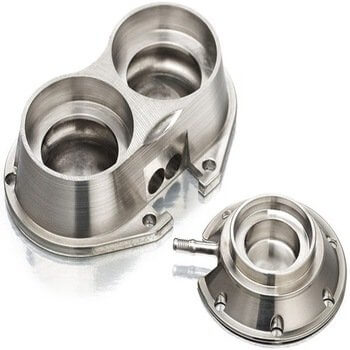
Another factor that contributes to machining deformation in aluminum parts is the cutting forces applied during the machining process. Aluminum is a relatively soft material, and excessive cutting forces can cause the material to deform. This is especially true for processes such as milling or turning, where the cutting tool exerts significant forces on the workpiece. The deformation caused by cutting forces can result in bending, twisting, or even buckling of the aluminum part.
Furthermore, the machining process itself can introduce stress into the aluminum part, leading to deformation. For example, during milling or drilling, the cutting tool creates localized stress concentrations on the surface of the part. This can cause the material to yield or deform plastically, resulting in dimensional inaccuracies. Additionally, the use of improper machining parameters, such as high cutting speeds or feed rates, can exacerbate the stress-induced deformation.
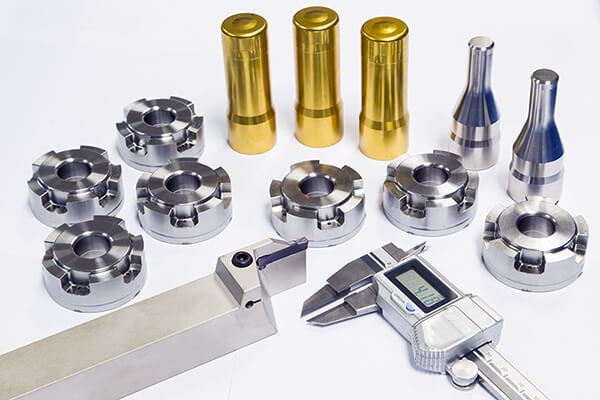
In addition to the material properties and machining forces, the design of the aluminum part can also contribute to machining deformation. Parts with complex geometries or thin walls are more prone to deformation due to the uneven distribution of cutting forces. The lack of rigidity in these areas can cause the part to bend or warp during machining. Moreover, improper fixturing or clamping of the part can also lead to deformation, as it may restrict the natural movement of the material during machining.
2.Common methods to reduce machining deformation of aluminum parts
To mitigate the machining deformation of aluminum parts, several common methods can be employed. One approach is to optimize the machining parameters, such as cutting speed, feed rate, and depth of cut. By selecting appropriate parameters, the cutting forces can be minimized, reducing the risk of deformation. Additionally, using cutting tools with sharp edges and proper geometries can help to reduce cutting forces and improve the surface finish.
Another method to prevent machining deformation is to implement proper fixturing and clamping techniques. This ensures that the part is securely held in place during machining, while still allowing for the necessary material movement. Using fixtures that distribute the clamping forces evenly across the part can help to minimize deformation.
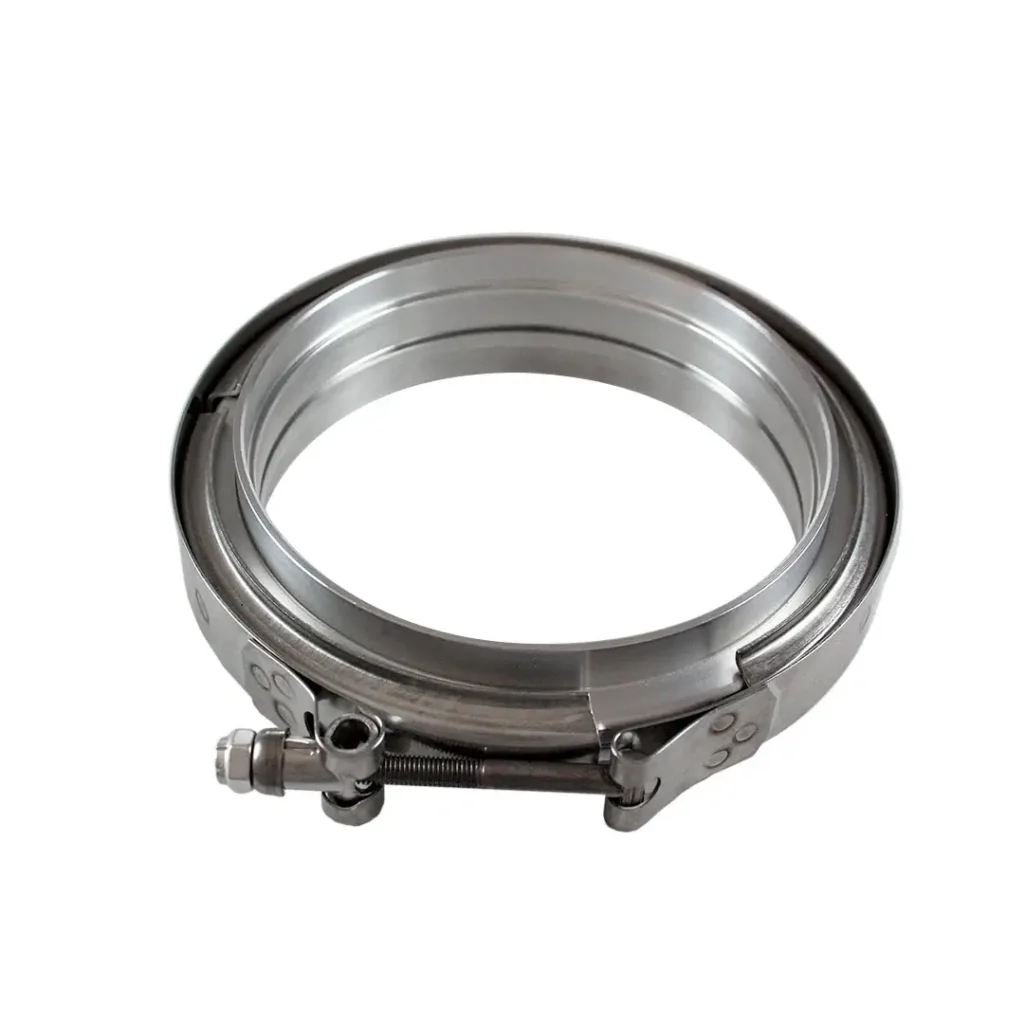
Furthermore, pre-machining operations, such as stress relieving or annealing, can be performed on the aluminum part to reduce internal stresses. This can help to stabilize the material and minimize the risk of deformation during subsequent machining processes.
3.Conclusion
In conclusion, understanding the causes of machining deformation in aluminum parts is essential for implementing effective solutions. Factors such as material properties, cutting forces, part design, and fixturing techniques all contribute to the deformation of aluminum parts during machining. By optimizing machining parameters, using proper fixturing techniques, and performing pre-machining operations, the risk of deformation can be minimized, resulting in high-quality aluminum parts.