Key Considerations for Testing and Inspection of Custom Machined Components
For custom machined parts, ensuring their quality and reliability is of utmost importance. These parts are often used in critical applications such as aerospace, automotive and medical, where any failure can have serious consequences. They can also be used in cat machine parts, cater wash 18kg washing machine parts, caterpillar machine parts, cda washing machine parts, centec milling machine parts and centre lathe machine parts, etc.
Therefore, thorough testing and inspection practices are essential to ensure the performance and safety of these parts such as cat machine parts, cater wash 18kg washing machine parts, caterpillar machine parts, cda washing machine parts, centec milling machine parts and centre lathe machine parts.
A Key Factor in Custom Machined Components
One key consideration in testing and inspection is dimensional accuracy. Custom machined components must meet precise specifications to function properly within a larger system. Any deviation from these specifications may result in compatibility issues or even complete failure. Therefore, to ensure dimensional accuracy, various measurement technologies such as coordinate measuring machines (CMM), optical comparators and laser scanning are used. These tools allow precise measurements to be taken and compared to required specifications.
Another crucial aspect of testing and inspection is material verification. Custom machined components are often made from specific materials with unique properties. It is essential to verify that the correct material has been used and that it meets the required standards. This can be done through various methods, including spectroscopy, hardness testing, and microstructure analysis. These techniques help identify any material inconsistencies or defects that could compromise the component’s performance.
In addition to dimensional accuracy and material verification, surface finish is also a critical factor in custom machined components. The surface finish affects not only the component’s aesthetics but also its functionality. A rough surface can lead to increased friction, wear, and potential failure. Therefore, thorough inspection of the surface finish is necessary. This can be achieved through visual inspection, profilometers, or surface roughness testers. By ensuring the desired surface finish, the component’s performance and longevity can be significantly improved.
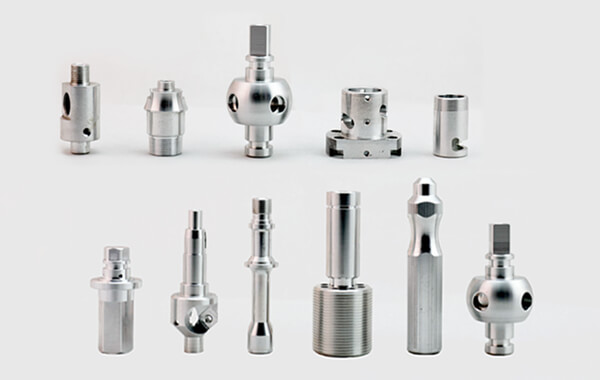
Furthermore, testing and inspection practices should also include functional testing. Custom machined components are designed to perform specific functions within a larger system. Therefore, it is crucial to verify that these components can fulfill their intended purpose. Functional testing can involve subjecting the component to simulated operating conditions, such as temperature, pressure, or vibration. This helps identify any potential issues or weaknesses that may arise during actual operation.
In addition to these specific considerations, it is essential to establish a comprehensive quality control system for custom machined components. This system should include regular inspections throughout the manufacturing process, from raw material inspection to final product testing. It should also involve documentation and traceability to ensure accountability and facilitate any necessary corrective actions. By implementing a robust quality control system, manufacturers can minimize the risk of defects and ensure consistent quality in their custom machined components.
In conclusion, testing and inspection practices play a vital role in ensuring the quality and reliability of custom machined components. Dimensional accuracy, material verification, surface finish, and functional testing are all key considerations in this process. Additionally, establishing a comprehensive quality control system is crucial for consistent quality and accountability. By adhering to these practices, manufacturers can deliver custom machined components that meet the highest standards and provide reliable performance in critical applications.