Improved Precision and Accuracy
One of the main advantages of VMC machined components is its higher precision and accuracy, mainly due to the fact that VMC (Vertical Machining Center) technology has revolutionized the manufacturing industry with numerous advantages over traditional machining methods. Including small parts such as cpap machine parts near me, cretors popcorn machine parts, cricut machine parts, crown point sewing machine parts, and crrt machine parts.
In this section, we will explore how VMC machined parts offer higher precision and accuracy than other machining technologies
Why VMC machined Components have such high precision and accuracy
One of the main reasons VMC machining is known for its precision is the use of computer numerical control (CNC) technology. CNC can precisely control the machining process, ensuring that each part such as cpap machine parts near me, cretors popcorn machine parts, cricut machine parts, crown point sewing machine parts and crrt machine parts is manufactured to precise specifications. This level of control cannot be achieved through manual machining methods, which inevitably produce errors that lead to inconsistencies in the final product.
In addition, VMC machines are equipped with advanced cutting tools and high-speed spindles, allowing them to achieve tight tolerances. Tolerance refers to the allowed deviation from the required dimensions of a part, and after processing with VMC, manufacturers can achieve tolerances as low as a few microns, ensuring that each part meets the required specifications.
Another advantage of VMC machined components is the ability to produce complex geometries with ease. VMC machines are capable of performing multiple machining operations in a single setup, eliminating the need for manual intervention and reducing the chances of errors. This allows for the creation of intricate designs and shapes that would be difficult or impossible to achieve with other machining methods.
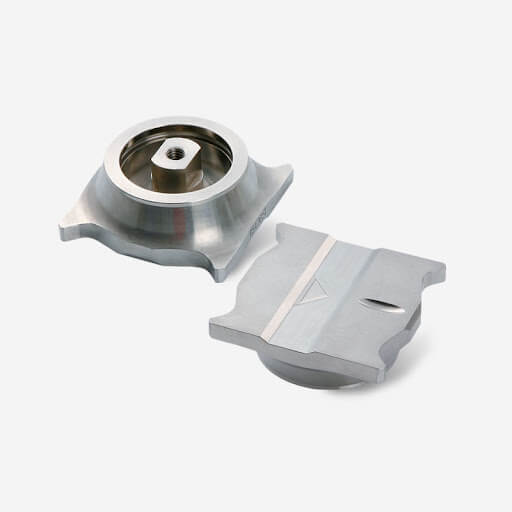
In addition to precision and complexity, VMC machined components also have a better surface finish. The high-speed spindles used by VMC machines, combined with advanced cutting tools, produce smooth, uniform surfaces. This is especially important in industries such as aerospace and medical, where components need to have a perfect finish to ensure optimal performance.
Moreover, VMC machining allows for faster production times compared to traditional machining methods. The automation provided by CNC technology eliminates the need for manual tool changes and adjustments, reducing setup times significantly. This, coupled with the ability to perform multiple operations in a single setup, enables manufacturers to produce components at a faster rate, increasing overall productivity.
In addition, VMC machines are equipped with advanced software that enables efficient programming and simulation. This means manufacturers can optimize machining processes, reduce material waste and minimize the risk of errors. The ability to simulate machining processes before actual production also enables better planning and troubleshooting, further improving the precision and accuracy of the final product of VMC machined components.
In conclusion, VMC machining offers several advantages over traditional machining methods when it comes to precision and accuracy. The use of CNC technology, advanced cutting tools, and high-speed spindles allows for tight tolerances and complex geometries. Additionally, VMC machines provide superior surface finish and faster production times, thanks to automation and efficient programming. These advantages make VMC machined components highly sought after in industries where precision and accuracy are paramount.