The Benefits of VMC Machined Components in Manufacturing
In the manufacturing industry, precision and efficiency are of utmost importance. Every component, no matter how small, such as de longhi espresso machine parts, delaval milking machine parts, and delonghi cappuccino machine parts, plays a vital role in the overall performance of the product. This is where VMC (Vertical Machining Center) machining components come into play. These components are manufactured using advanced CNC (Computer Numerical Control) technology, which allows for precise and accurate machining.
In this article, we will explore the advantages of VMC machining parts in manufacturing industries such as de longhi espresso machine parts, delaval milking machine parts, and delonghi cappuccino machine parts.
Advantages of VMC Machined Components in the Manufacturing Industry
One of the key advantages of VMC machined components is their ability to produce complex shapes and designs with high precision. The CNC technology used in VMC machining allows for intricate detailing and tight tolerances, ensuring that each component is manufactured to exact specifications. This level of precision is crucial in industries such as aerospace, automotive, and medical, where even the slightest deviation can have serious consequences.
Another benefit of VMC machined components is their versatility. These components can be manufactured from a wide range of materials, including metals, plastics, and composites. This flexibility allows manufacturers to choose the most suitable material for their specific application, taking into consideration factors such as strength, durability, and cost. In addition, VMC machining can be used to manufacture parts of various sizes, including de longhi espresso machine parts, delaval milking machine parts, and delonghi cappuccino machine parts, from small complex parts to large structural components.
In addition to precision and versatility, VMC machined components offer improved efficiency in the manufacturing process. The use of CNC technology eliminates the need for manual labor, reducing the risk of human error and increasing productivity. With VMC machining, manufacturers can produce components at a faster rate, meeting tight deadlines and increasing overall production capacity. This efficiency not only saves time but also reduces costs, making VMC machined components a cost-effective solution for manufacturers.
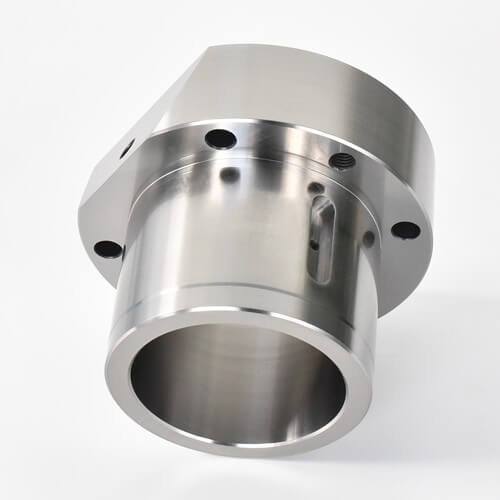
Furthermore, VMC machined components are known for their superior surface finish. The CNC technology used in VMC machining ensures that every part machined has a smooth, consistent surface without defects such as burrs or rough edges. This high-quality surface treatment not only enhances the aesthetics of the component, but also improves performance and extends its service life, among other functions, because parts with a smooth surface have the advantage of less friction.
In terms of sustainability, VMC machined components offer several advantages. The precision and accuracy of VMC machining reduce material waste, as components are manufactured to exact specifications, minimizing the need for additional machining or modifications. Additionally, the use of CNC technology allows for efficient use of energy and resources, further reducing the environmental impact of the manufacturing process. By choosing VMC machined components, manufacturers can contribute to a more sustainable and eco-friendly manufacturing industry.
In conclusion, VMC machined components offer numerous benefits in the manufacturing industry. From their precision and versatility to their efficiency and sustainability, these components are revolutionizing the way products are made. With VMC machining, manufacturers can achieve higher levels of quality, productivity, and cost-effectiveness. Whether it’s in aerospace, automotive, or medical applications, VMC machined components are unleashing the power of advanced manufacturing technology.