Introduction to Machined Components
Machined parts, such as drilling machine parts, dry cleaning machine parts, dry cleaning machine spare parts and dryer machine parts, play a vital role in various industries ranging from automotive to aerospace. These parts are manufactured through a process called machining, which involves using cutting tools to remove material from the workpiece.
Known for their precision, durability and versatility, machined parts such as drilling machine parts, dry cleaning machine parts, dry cleaning machine spare parts and dryer machine parts are an essential component of many products and systems.
Types of Machined Components
There are several types of machined components, each with its own unique characteristics and applications. One common type is a shaft, which is a cylindrical component used to transmit power or motion and is typically found in engines, pumps, and other rotating machinery. Another type is gears, which are used to transmit torque and change the speed or direction of rotation, often found in transmissions, engines, and industrial machinery.
In addition to shafts and gears, there are many other types of machined components, including bearings, valves, pistons, and connectors. Each of these components serves a specific purpose and is designed to meet specific requirements. For example, bearings are used to reduce friction and support rotating shafts, while valves control the flow of fluids or gases. Piston components are used in engines to convert pressure into mechanical motion, and connectors are used to join different parts together.
One of the main advantages of using machined components is their high level of precision. Machining processes can achieve tight tolerances, ensuring that components fit together perfectly and function as intended. This precision is crucial in industries where even the smallest deviation can lead to catastrophic failures or performance issues. Additionally, machined components are known for their durability and strength. They can withstand high loads, extreme temperatures, and harsh environments, making them suitable for demanding applications.
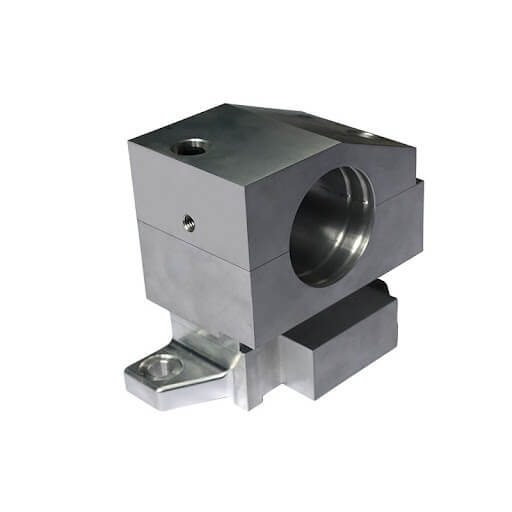
Designing machined components requires careful consideration of various factors, including material selection, geometry, and manufacturing processes. The choice of material depends on the specific application and requirements of the component. Common materials used for machined components include metals such as steel, aluminum, and titanium, as well as engineering plastics. The geometry of the component is also important, as it affects its functionality, strength, and manufacturability. Designers must consider factors such as stress distribution, weight, and ease of assembly.
When it comes to manufacturing machined components, there are several processes to choose from. The most common machining processes include turning, milling, drilling and grinding. Where turning is the removal of material using a cutting tool while involving rotating the workpiece to form a cylindrical shape, milling is the removal of material from the workpiece in a controlled manner using a rotating cutting tool, drilling uses a rotating cutting tool to make holes in the workpiece, and grinding Abrasive particles are used to remove material and achieve a smooth surface finish.
In conclusion, machined components are essential in various industries due to their precision, durability, and versatility. They come in different types, each serving a specific purpose and designed to meet specific requirements. The advantages of using machined components include their high level of precision, durability, and strength. Designing and manufacturing machined components require careful consideration of factors such as material selection, geometry, and manufacturing processes. In the next section, we will explore the different types of machining processes in more detail.