Understanding the Importance of Material Selection in CNC Component Production
When it comes to producing quality precision CNC components, one of the most crucial factors to consider is material selection. The choice of material can greatly impact the performance, durability, and overall quality of the finished product. In this article, we will explore the significance of material selection in CNC component production and provide some top tips to help you make informed decisions.
The Impact of Materials on Producing Quality Precision CNC Components
First and foremost, it is essential to understand that different materials possess varying properties and characteristics. These properties can significantly influence the behavior of the component during machining, as well as its performance in the final application. For instance, some materials may be more prone to warping or distortion under high temperatures, while others may offer superior strength or corrosion resistance. By carefully selecting the appropriate material, you can ensure that your precision CNC components meet the desired specifications and perform optimally in their intended applications.
When selecting materials for CNC part production, a key consideration is compatibility between the material and the machining process. Because different materials have different machining characteristics, this means they may require specific cutting tools, speeds, feeds and coolant strategies to achieve the desired results. Failure to consider these factors can result in poor surface finish, excessive tool wear, or even component failure. Therefore, it is critical to consult with a materials supplier or machining expert to determine which materials are best suited for your specific CNC machining process.
Another important aspect to consider is the cost-effectiveness of the chosen material. While some materials may offer superior performance, they may also come with a higher price tag. It is essential to strike a balance between performance and cost to ensure that your precision CNC components are both high-quality and economically viable. Conducting a thorough cost analysis, including material costs, machining costs, and potential savings in downstream processes, can help you make informed decisions and optimize your production processes.
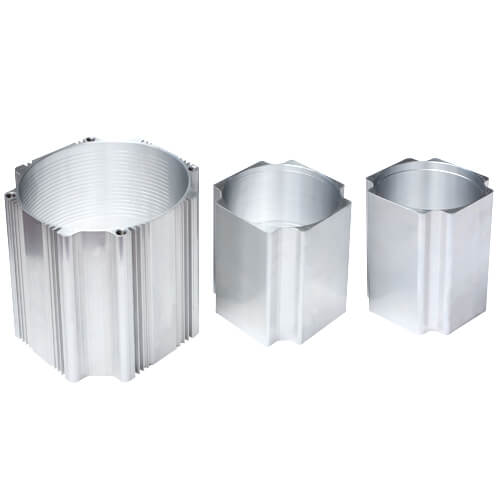
Furthermore, it is crucial to consider the environmental and regulatory implications of the chosen material. Some materials may contain hazardous substances or have adverse environmental impacts during production, use, or disposal. By selecting materials that are environmentally friendly and comply with relevant regulations, you can contribute to sustainable manufacturing practices and enhance your company’s reputation.
To aid in the material selection process, it is advisable to establish strong relationships with material suppliers and machining experts. These professionals can provide valuable insights and recommendations based on their expertise and experience. They can also help you stay updated on the latest advancements in materials and machining technologies, ensuring that you are always using the most suitable materials for your CNC component production.
In conclusion, material selection plays a critical role in producing quality precision CNC components. By carefully considering the properties, machinability, cost-effectiveness, and environmental implications of different materials, you can ensure that your components meet the desired specifications and perform optimally in their intended applications. Establishing strong relationships with material suppliers and machining experts can also provide valuable guidance and support throughout the material selection process. By following these top tips, you can enhance the quality and performance of your precision CNC components, ultimately leading to greater customer satisfaction and business success.