Advances in Ultra Precision Machining Technology: A Comprehensive Overview
Ultra-precision machining technology has made significant progress in recent years, revolutionizing various industries and opening up new possibilities for precision manufacturing. Fives machining systems is able to offer a wide range of grinding tools (machines, accessories, system lines) and high-precision machines.
This comprehensive overview aims to shed light on the latest developments in the field and explore cutting-edge technologies and their applications.
Key advances in ultra precision machining technology and related applications
One of the key advancements in ultra precision machining technology is the use of diamond turning. This technique involves the use of a single-point diamond tool to shape and finish the surface of a workpiece with exceptional precision. Diamond turning has gained popularity due to its ability to achieve sub-micron level accuracy, making it ideal for manufacturing optical components, such as lenses and mirrors.
Another notable development in ultra precision machining is the advent of micro milling. Micro milling involves the use of miniature cutting tools to create intricate features on small workpieces. This technique has found applications in the production of microelectromechanical systems (MEMS), where precise and complex structures are required. Micro milling has also been utilized in the fabrication of microfluidic devices, enabling the precise control of fluid flow at the microscale.
In addition to diamond turning and micro milling, advancements in ultra precision machining have also been driven by the development of advanced control systems. These systems utilize real-time feedback and adaptive control algorithms to compensate for errors and improve machining accuracy. By continuously monitoring and adjusting machining parameters, these control systems enable the production of high-quality components with minimal errors.
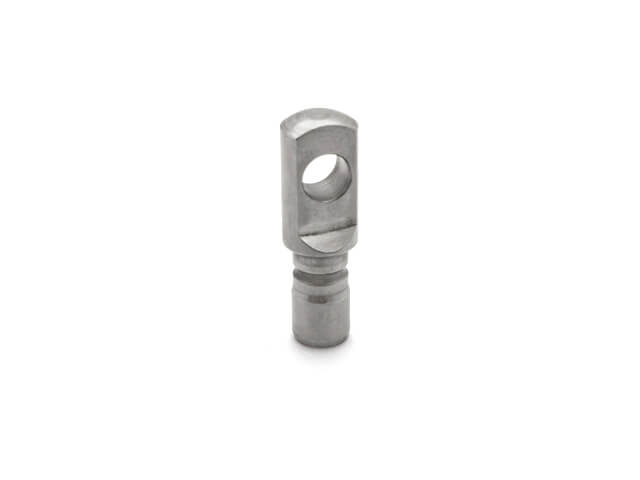
Furthermore, the integration of advanced metrology techniques has played a crucial role in enhancing the accuracy and reliability of ultra precision machining. Metrology techniques, such as interferometry and coordinate measuring machines, enable the measurement of surface profiles and dimensional accuracy with nanometer-level precision. This ensures that the machined components meet the stringent requirements of various industries, including aerospace, medical, and electronics.
The applications of ultra precision machining technology are vast and diverse. In the aerospace industry, ultra-precision machining is used to manufacture critical components such as turbine blades and fuel nozzles, as these components require high dimensional accuracy and surface finish. Also in the medical field, ultra-precision machining is used in the production of surgical instruments, implants and prostheses, where precision and biocompatibility are crucial.
Moreover, ultra precision machining has found applications in the electronics industry, particularly in the fabrication of microelectronics and nanoelectronics. The ability to create intricate features and high-density circuits has enabled the miniaturization of electronic devices, leading to the development of smaller and more powerful gadgets.
In conclusion, advances in ultra precision machining technology have revolutionized precision manufacturing, enabling the production of components with unprecedented accuracy and surface finish. Diamond turning, micro milling, advanced control systems, and metrology techniques have all contributed to the progress in this field. The applications of ultra precision machining are diverse, spanning industries such as aerospace, medical, and electronics. As technology continues to evolve, it is expected that ultra precision machining will play an even more significant role in shaping the future of manufacturing.