The Rise of 3D Printing in Custom Metal Parts Manufacturing
The manufacturing industry has seen significant advancements in recent years, particularly in the field of custom metal parts manufacturing. One of the most notable innovations in this industry is the rise of 3D printing technology. 3D printing, also known as additive manufacturing, has revolutionized the way custom metal parts are produced.
Traditionally, custom metal parts manufacturing involved a lengthy and complex process. It typically required the use of specialized machinery and skilled labor to shape and mold metal into the desired form. This process often resulted in high costs and long lead times, making it difficult for manufacturers to meet the demands of their customers.
However, with the advent of 3D printing technology, the landscape of custom metal parts manufacturing has changed dramatically. 3D printing allows manufacturers to create complex metal parts directly from a digital design, eliminating the need for traditional manufacturing methods. This not only reduces costs but also significantly shortens the production time.
Advantages of 3D Printing in Custom Metal Parts Manufacturing
One of the main advantages of 3D printing in the manufacturing of custom metal parts is its ability to produce highly complex designs. In traditional manufacturing methods, it is difficult to create complex geometries because they require multiple steps and processes. With 3D printing, manufacturers can easily produce complex designs with minimal effort. This opens up new possibilities for designers and engineers, allowing them to create innovative and unique metal parts that were previously impossible to manufacture.
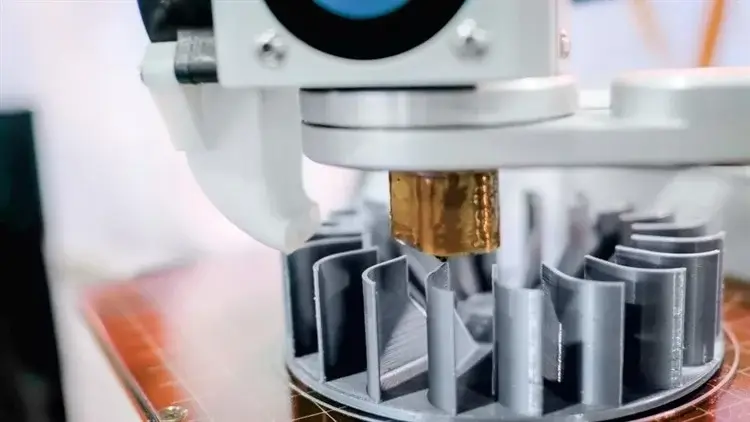
Another advantage of 3D printing in custom metal parts manufacturing is its ability to reduce material waste. Traditional manufacturing methods often result in a significant amount of material being wasted during the production process. This not only adds to the cost but also has a negative impact on the environment. 3D printing, on the other hand, is an additive process, meaning that it only uses the necessary amount of material to create the desired part. This not only reduces waste but also makes the manufacturing process more sustainable.
Furthermore, 3D printing technology offers manufacturers the flexibility to produce small batch sizes or even individual parts on demand. Traditional manufacturing methods often require manufacturers to produce large quantities of parts to make the process cost-effective. This can lead to excess inventory and storage costs. With 3D printing, manufacturers can easily produce small quantities of custom metal parts without incurring additional costs. This allows for greater customization and personalization, as manufacturers can quickly respond to customer demands and produce parts as needed.
Despite its numerous advantages, 3D printing in custom metal parts manufacturing is not without its challenges. One of the main challenges is the limited range of materials that can be used in 3D printing. While there have been advancements in the availability of metal powders for 3D printing, the range of materials is still relatively limited compared to traditional manufacturing methods. This can be a constraint for manufacturers who require specific material properties for their custom metal parts.
In conclusion, the rise of 3D printing technology has revolutionized the field of custom metal parts manufacturing. It offers numerous advantages, including the ability to produce highly intricate designs, reduce material waste, and provide flexibility in production quantities. However, there are still challenges to overcome, such as the limited range of materials available for 3D printing. Nonetheless, 3D printing has undoubtedly opened up new possibilities and opportunities for manufacturers in the custom metal parts industry.