The Basics of CNC Precision Machining
The demand for CNC precision machining is growing in today’s manufacturing industry, so we’ve compiled this guide that details CNC precision machining so you don’t have to look elsewhere.
1.What is CNC Precision Machining?
CNC precision machining is a production process in which a blank or workpiece is transformed into a finished product through subtractive machining using a machine tool controlled by a CNC machine and guided by a computer-aided design of the desired shape. Subtractive machining here refers to the removal of material from the workpiece.
Precision CNC machining relies on computer-aided design (CAD) for product design and computer-aided manufacturing (CAM) to transform the part into a machinable process through CNC machine instructions. Despite the automated nature of manufacturing instructions, CNC machining still requires a skilled machinist at some stage.
High-precision CNC machining is desirable because it produces standardized parts that are almost identical, with little deviation from the required diameter, length and size. Precision machining services are utilized by automotive companies, the defense industry that manufactures aerospace vehicles and landing gear ports, and develops prototypes and custom CNC machined parts.
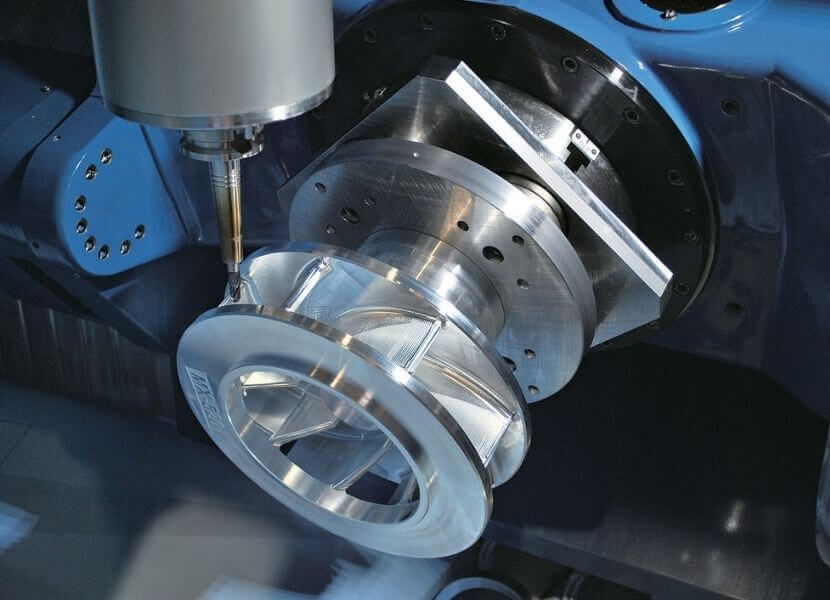
2.CNC Precision Machining Tolerances
CNC machining tolerances define the most feasible CNC technology for machining parts. Precision CNC machining equipment can achieve very tight tolerances up to 0.0025 mm. However, CNC machining for such tolerances is expensive, time consuming, and often not required.
Most precision machining services can provide tolerances of ± 0.051 mm to ± 0.005 mm. Precision machining processes are able to maintain this tolerance, or achieve closer tolerances for tiny parts depending on the desired shape and raw material.
There is no specific tolerance for precision machining processes, the variations come from the type of manufacturing process, CNC machine, and tolerance measurement system.
The most common tolerance measurement systems for machined parts are:
- Limit Tolerance: Limit tolerance specifies the range of values a dimension can take. It is usually between two numbers with its precision defined by decimal places.
- Unilateral Tolerance: Tolerance is specified for only one side of the dimension. This means that it can exceed the nominal dimension on one side but stay within the exact tolerance on the other side.
- Bilateral Tolerance: This is the most common tolerance and you will see it as a value with a ± sign. The dimension can deviate on both sides.
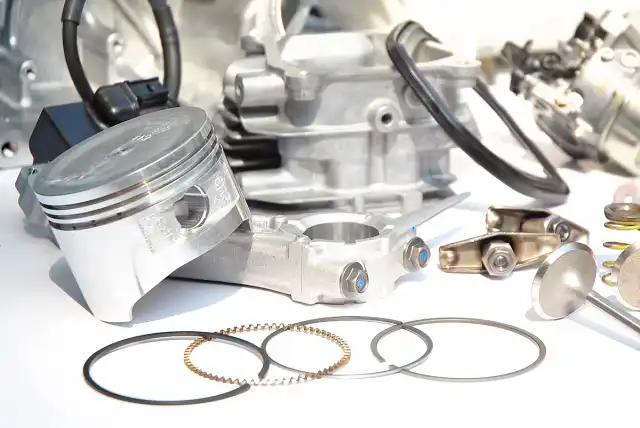
3.Common Types of Precision Machining Equipment
Precision machining is not a new process, but not all machines are capable of it. The most common type of precision machining equipment relies on CAM software to control computer numerical control (CNC) machines.
Although these machines are capable of completing most processes, some tasks are better done with certain machines in terms of cost minimization and productivity.
1) CNC Milling Machines
CNC milling machines have a spindle that holds a cylindrical tool that moves along the axis of the machine. CNC milling machines have a variety of multi-tooth cutting tools. CNC milling machines are used for rectangular blanks and can be used for a variety of operations from drilling holes to carving slots. They are also used to shape surface features and match common tolerances before surface finishing.
Milling machines are generally used to shape flat surfaces. CNC milling machines can do face milling or perimeter milling. Perimeter milling features are cut by placing the tool parallel to the workpiece.
2) CNC Lathes and Turning Machines
CNC lathes are able to shape cylindrical blanks by rotating the part at high speeds and driving it on a predetermined axis. The tool remains stationary and the chuck rotates.
Another type of CNC lathe is the Swiss-type lathe. A relatively modern addition to the main CNC machine tool, the Swiss-type lathe uses a sliding headstock and guide bushings to support long cylindrical parts. In addition to this, Swiss-type lathes also have milling capabilities.
CNC lathes are specialized to provide a few standard turning operations such as reaming, drilling, spherical balls, pins, grooves or tapping and tapers. Keep in mind that CNC lathes are strictly used to produce machined components for cylindrical parts.
3) CNC Drilling Machines
Drilling holes does not usually require high precision, and most vertical drilling machines are manually operated. However, when producing holes of close tolerances and the same size, it is important to have an automated CNC machine.
In addition to cylindrical holes of the required diameter, CNC drilling machines include broaching machines, drill presses, spiral drilling machines, and clamping reamers.
These holes are often used for screws, automotive parts, and plastic components. For example, the speaker holes in the metal chassis of a mobile phone are made by a precision CNC drilling machine.
4) Electrical Discharge Machine (EDM)
Electrical discharge machines remove metal by continuously creating sparks on the metal and generating heat. This process is called spark machining, and it works by applying a direct current to an electrode and the metal part below, forming an electric field.
Tiny metal parts suspended in the electrode are formed at the center of this field, and because they are conductive, these tiny metal impurities heat up, and the plasma burns the material, removing the metal.
EDM uses a wire or sinker die. Wire EDM machines use the principle of burning away material with an electrode wire, while sinker die EDM machines use an electrode that is a positive image of the desired cavity.
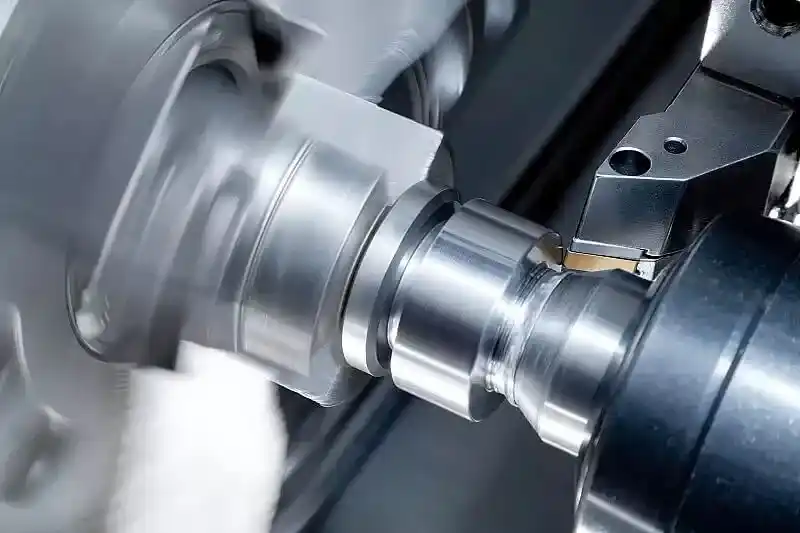
4.Application Areas CNC Precision Machining
1) Aerospace
CNC precision machining is widely used in the aerospace industry to manufacture critical components with high precision and close tolerances. It is used to produce engine parts, turbine blades, landing gear components, structural components, etc.
2) Automotive Industry
CNC precision machining plays a vital role in the automotive industry and is used to manufacture engine components, gearbox components, suspension systems, brake components, and other critical components. It ensures high accuracy and repeatability, thereby improving the performance and reliability of automotive systems.
3) Medical Devices
CNC precision machining produces complex components for medical devices such as surgical instruments, implants, prostheses, orthopedic instruments, dental components, and diagnostic equipment. Its high precision ensures the safety and functionality of these devices.
4) Electronics
CNC precision machining involves the production of electronic components such as connectors, housings, heat sinks, and PCBs (printed circuit boards). CNC machines are capable of creating precise features, complex patterns, and fine details required in the electronics industry.
5) Defense and Military
CNC precision machining is essential for manufacturing components used in defense and military applications. It is used to produce firearms, weapon systems, optics, armored vehicle components, and other defense-related equipment that require high precision, reliability, and durability.
6) Industrial Equipment
CNC precision machining is widely used in the production of a wide range of industrial equipment, including pumps, valves, gears, bearings, shafts, and machine tool components. CNC machines are capable of creating complex geometries that ensure efficient and reliable operation of industrial machinery.
5.Summary
CNC precision machining uses milling machines, lathes, drills, and some other precision machines such as EDM to shape the workpiece into the final design. The added advantage of achieving tighter tolerances in any manufacturing process makes it a premium product and has a higher quality grade.
They are mainly used in applications that require high precision and small tolerances, ranging from defense system applications to watch component housings. The process of precision machining is similar to standard CNC, but there is a huge difference in the quality of the final CNC precision machining parts.