The Basics of CNC Precision Machining
Automotive components, medical implants, defense equipment parts, and many other applications require tight tolerances to function, often down to ±0.001 inches. This level of precision cannot be achieved with standard machining methods. This is where CNC precision machining comes into play. Different precision machines and tools perform machining operations to manufacture precision parts and products across various industries.
To take full advantage of this manufacturing precision, you need to understand its nuances. So, let’s discuss the processes, equipment, materials, benefits, and applications of precision CNC machining.
1.What is CNC precision machining?
First let’s understand what CNC machining is. It is a computer-controlled machining process that automatically removes material based on uploaded designs and digital instructions. The automation of tool movement provides tighter tolerances compared to traditional machining methods.
At the same time, precision machining usually involves tolerances of ± 0.1 to 0.2 mm. Therefore, specialized machining tools, optimized parameters, and expert processing are the main strategies to achieve this precision.
The main importance of CNC precision manufacturing lies in producing identical parts for automotive, medical, defense, and other industries. Manufacturers use several pieces of equipment, such as milling machines, EDM units, and lathes, to produce precision-machined parts.
In addition, CAD and CAM also play a vital role in this process. CAM converts the 3D model of the part into machining instructions for the CNC machine. The machine then instructs the movement of all cutting tools along a predetermined path until the desired shape is formed.
2.A step-by-step guide to the CNC precision machining process
1) Design and CAD modeling
After final requirements are determined, engineers or designers create a detailed 3D engineering design with dimensions, tolerances, features, proportions, and other information. Typically, computer software such as AutoCAD or Solidworks helps in CAD modeling of the intended part or product. In addition, design for manufacturability (DMF) is an important consideration at this stage. The model must be compatible with precision CNC machining technology.
2) CAM and CNC programming
Next, the CAM system software generates tool movement instructions, known as G&M codes, based on the CAD model. This process is also known as CNC programming; these codes are readable by CNC precision machines. CAM can also simulate the best tool paths for removing material, which helps minimize rounding errors and improve accuracy.
3) CNC machine setup
Precise CNC machine setup involves two main tasks: tool setup and workpiece clamping. First, the operator mounts the tool in a collet or tool holder and the workpiece on the machine bed or chuck. However, the machine can also have an automatic tool change (ATC) mechanism.
At this stage, choosing the right tool (end mill, face mill, drill, etc.) and stably holding the workpiece and tool are critical to the final accuracy. Improper machining tools or misalignment between the tool and the workpiece can cause serious quality defects in precision machined parts.
4) Machining parts
The machine tool establishes a connection with the control system to process the operating instructions. This is the actual machining stage, and the CNC operator manually sets parameters such as spindle speed, depth, feed rate, etc. Next, the machine executes the instructions and the tool moves to machine the workpiece. At the same time, testing and fine-tuning parameters can help produce parts according to accuracy requirements.
5) Post-processing and finishing
This is the last and most important step of CNC precision machining. The machined parts may contain tool marks, burrs or notches, which affect dimensional accuracy and aesthetics. Post-processing methods such as grinding and deburring can accurately obtain the required dimensions by removing trace materials from the surface. Subsequently, finishing strategies such as sandblasting, electroplating or polishing can improve surface quality and aesthetics. At the same time, some low-friction applications such as hydraulic rods or rotating parts require finishing to perform their functions and performance.
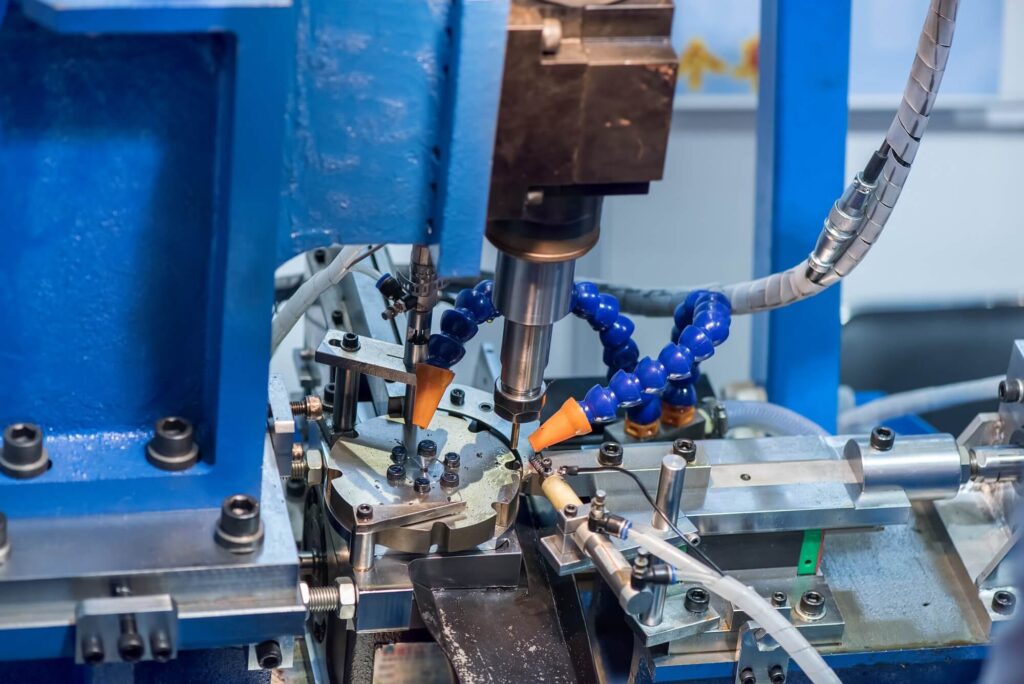
3.Types of precision CNC machine tools
Milling machines, lathes, EDM machines, drilling machines, and many other machines have brought precision to the manufacturing industry. Each machine has some specific functions and is suitable for specific machining tasks. For example, CNC lathes are ideal for symmetrical items, while milling machines are best suited for flat surfaces. Therefore, which CNC machine is right for you depends on the 3D design and required functions.
1) CNC milling machine
CNC milling machines involve rotating cutting tools that can move along multi-axis linear and rotational motions and feed the workpiece linearly. The spindle can rotate at high speeds (up to 2400 rpm) without compromising accuracy and quality down to +/-0.0025mm. CNC precision milling can manufacture complex parts from flat and planar workpieces. In addition, the spindle can be positioned horizontally or vertically. At the same time, some advanced milling machines can have both spindle positioning functions.
2) CNC Lathes and Turning Centers
Lathes and turning centers are also part of CNC precision manufacturing. CNC lathes or turning centers rotate the workpiece and the tool moves linearly (along and through the workpiece) to remove and shape the material. Therefore, they are used to manufacture axisymmetric items such as cylindrical products.
In addition, precision CNC turning methods can machine complex details and shapes because the workpiece rotates instead of the cutting tool. The fixed tool can move across the workpiece, allowing for a precise material removal process.
3) CNC Drilling Machines
The principle of CNC drilling is to rotate the drill bit and fix the workpiece. When the drill penetrates the surface, it cuts and shaves away the material in the drilling area to form a hole. The size of the drill bit is the same as the diameter of the desired hole.
Precision CNC drilling techniques include:
- Spot drilling: Drilling a shallow hole at a precise location followed by immersion of the drill, particularly for hard materials.
- Peck drilling: For deep holes, the drill is periodically retracted during the drilling process to clear chips and reduce heat buildup.
4) Electrical discharge machining (EDM)
This is a non-contact machining process that creates a cut by eroding the material by generating an electrical spark (discharge). Here, the workpiece and tool act as electrodes and the discharge is generated by the immersed piezoelectric fluid.
This CNC precision machining process produces minimal mechanical stress and can cut hard metals and alloys such as titanium and tungsten. In addition, EDM machines are known for their ability to create complex shapes and details with high precision and repeatability, such as molds.
5) CNC plasma cutting machine
Plasma refers to an ionized gas beam produced when air or gas is heated to 10,000°c. In CNC precision machining, CNC plasma cutting machines use this gas beam to cut heat-conductive materials. The power supply unit provides high voltage to ionize the gas flowing in the plasma torch. The torch then focuses the plasma on the workpiece through the nozzle, melting the material and cutting it. Unlike traditional shearing or water jet cutting, it provides superior machining accuracy. Plasma cutting tolerances can be as low as 0.001 inches.
6) CNC precision grinder
CNC grinders are post-processing equipment used for high-precision manufacturing. They contain a rotating grinding wheel with an abrasive layer of specific thickness and grit. The machined parts are fed into the grinding wheel to eliminate surface defects and smooth the surface by cutting tiny materials and irregularities with abrasives.
These machines are not only able to process dimensions, but also provide polished or even mirror-like surfaces. Precision grinders can produce smooth surfaces with roughness (Ra) values of 3.2 to 0.8 μm.
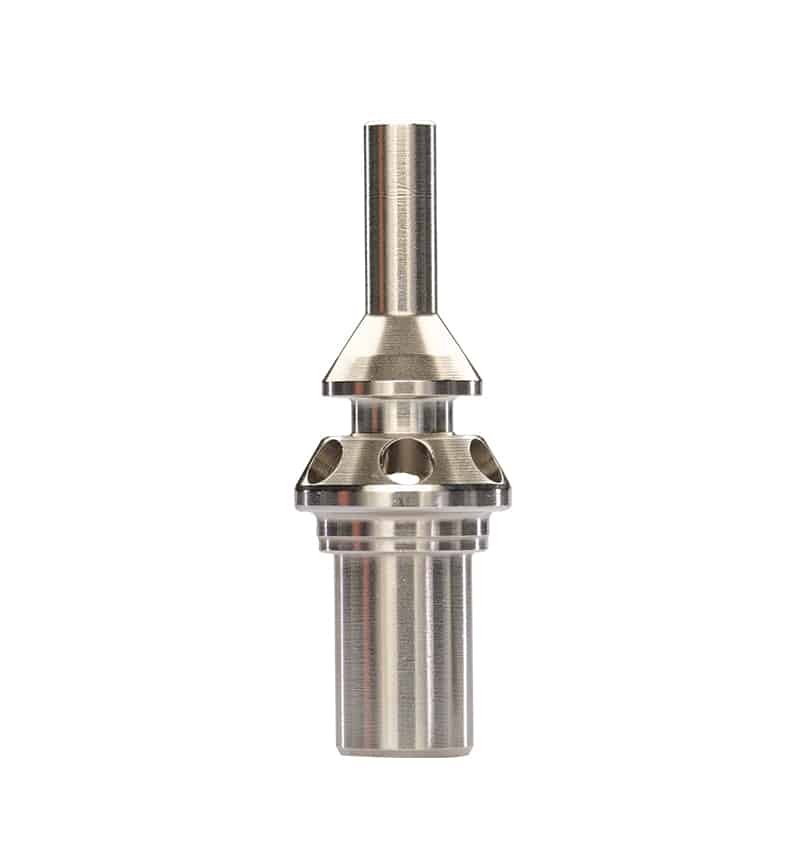
4.Materials suitable for CNC precision machining
Plastics, metals, composites, and some other materials can be processed with CNC machines. However, CNC precision manufacturing mainly involves metals and plastics. The tools and parameters for each CNC material differ based on its characteristics and machinability level.
In addition, the material suitable for CNC precision machining parts should be selected based on the function required by the part and the operating environment.
1) Metals
The hardness of metals and alloys requires hard precision tools made of diamond-coated carbides. At the same time, considering thermal expansion and effective cooling systems to offset heat buildup are essential for metal machining.
Metal selection also affects the total cost of the machining project because material cost is a significant cost factor. Therefore, balance material performance needs and expenses. In addition, you can read more about economical metals for CNC precision machining here.
CNC precision machining metals are as follows:
- Aluminum 6061, 7075, 2024
- Steel 1018, 4140, 1045, A2, D2,
- Stainless steel 304, 316 and 17-4 PH
- Titanium Ti-6Al-4V
- Copper: C101 and C110
- Brass C360 C260
- Bronze C932 and C954
- Inconel 718
- Monel 400
2) Plastics
One of the main challenges of plastic machining is its sensitivity to heat. Therefore, production speed is slower than metal machining. However, plastic CNC precision machining still provides dimensional accuracy and smooth machining results. At the same time, plastic machining tools are standard carbide cutting tools.
Here is a list of plastics commonly used in CNC precision machining projects:
- Acrylic (PMMA)
- Nylon 6, Nylon 6/6, Oil-filled Nylon
- Anti-lock Braking Systems
- Polycarbonate (PC)
- Polyethylene
- Polyoxymethylene (POM) or Acetal
- PTFF and Filled PTFE (Glass, Carbon, Bronze)
- Polyetheretherketone (PEEK)
5.Main Applications and Industries for CNC Precision Machining Parts
Now, let’s discuss the uses of CNC precision machining parts or finished products. These applications can be seen in areas where tolerances and surface finish are critical, such as aircraft components and medical implants. In addition, plastics are also popular in precision prototyping and the production of industrial parts in various industries.
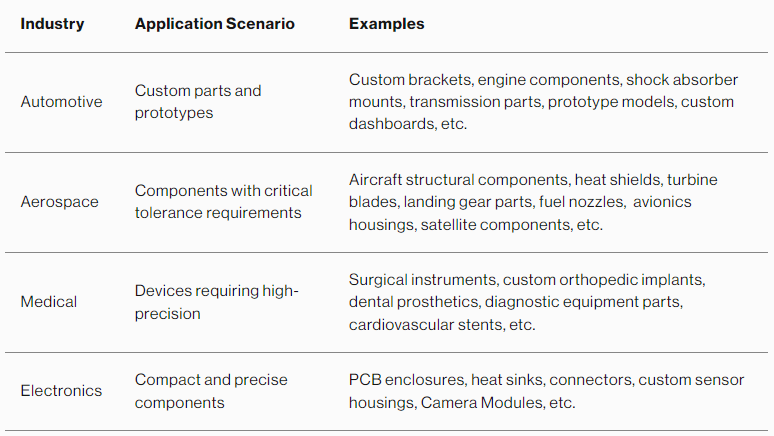
6.Advantages of High CNC Precision Machining
1) Improved Accuracy and Repeatability
The main difference between standard CNC machining and CNC precision machining is accuracy. CNC precision machining equipment can run the same set of instructions to achieve strict accuracy and consistency from batch to batch. This repeatability helps ensure that identical parts are produced in large quantities.
2) Reduced waste and increased efficiency
Optimal tools and parameters maximize the use of raw materials and minimize scrap and waste. Therefore, efficient material utilization reduces waste and reduces material costs. In addition, consistent production quality, faster processing time, and minimal defective products due to automation can significantly improve overall production efficiency.
3) Complex geometries with tight tolerances
Complex parts such as turbine blades, custom implants, and molds can also be accurately manufactured using precision machining technology. Multi-axis capabilities, computer-controlled tools, real-time monitoring and adjustments, and other features allow for the manufacture of highly complex components and precision-machined products while maintaining strict dimensional accuracy.
4) Material versatility
By adjusting CNC machining variables and tool settings, we can accommodate a wide range of materials, from hard titanium alloys to soft aluminum and plastics. In addition, some metals and thermoset composites are also compatible. The rich and diverse CNC material options help to select the most appropriate material for specific application needs.
5) Production Flexibility
CNC precision machining technologies (milling, turning, drilling, and EDM) are flexible to adapt to production volumes, whether you need a small number of prototypes or large-scale production. Therefore, a just-in-time manufacturing strategy can reduce the setup, processing, and machining time of customized parts.
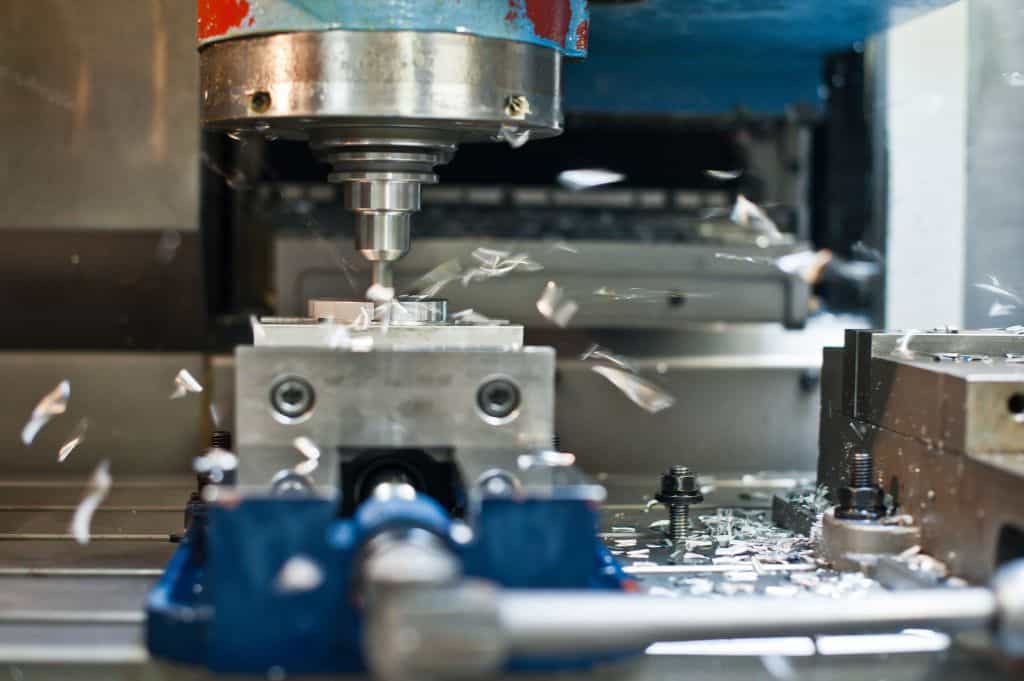
7.Conclusion
CNC precision machining solves the problems of complexity and dimensional accuracy. Automation and minimal human intervention in the operation of CNC equipment can achieve tight tolerances. In addition to accuracy, the speed, efficiency, and customization advantages of this manufacturing strategy can reduce time and save costs.
You can choose this precision manufacturing in a variety of applications, from medical components to electronics. However, considering the cost factor and the necessity of high precision for operation and durability, it is equally important to maximize the use of technology and minimize the price of the service.