Aluminum CNC Machining in Detail
Aluminum is a non-ferrous metal that is commonly used for a variety of purposes. Manufacturers often use aluminum for a variety of products because it is inexpensive, non-toxic, recyclable, and machinable, making it an ideal material for CNC machining. However, understanding aluminum CNC machining is essential to realizing the full potential of aluminum.
This article discusses aluminum CNC machining, the benefits of using aluminum for CNC machining, and the different grades of aluminum used in CNC machining. You will also learn about standard aluminum CNC machining techniques and applications.
1.Introduction to Aluminum CNC Machining
Aluminum is a versatile metal material that is commonly used for different purposes across a wide range of industries. Pure aluminum is soft, non-magnetic, and ductile, and can be alloyed with various elements such as magnesium, copper, and manganese to create different alloys with different improved properties.
Due to the excellent machinability of aluminum, aluminum CNC machining is one of the top machining operations in terms of frequency of execution. Manufacturers rely on aluminum CNC machining to create different precision aluminum parts that meet the requirements of the intended application. The process involves shaping aluminum into the desired shape and size using a CNC router.
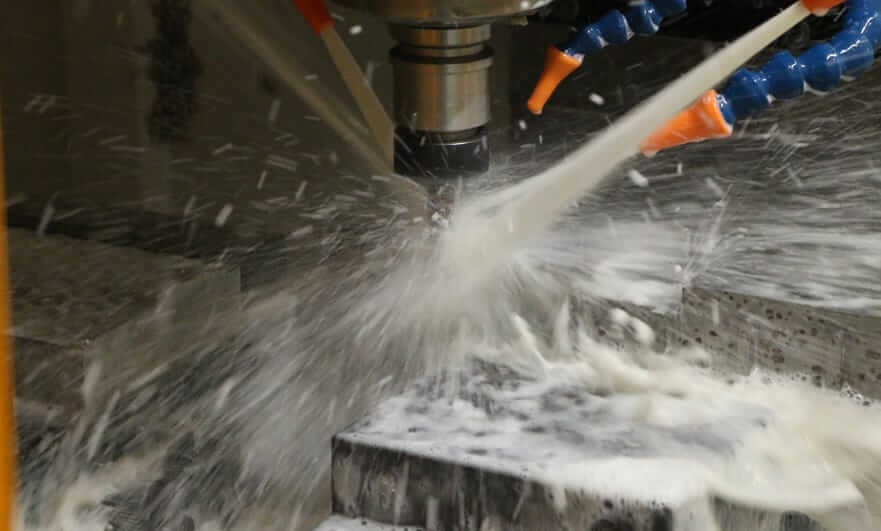
2.Advantages of aluminum that make it an ideal material for CNC machining
Aluminum alloys have various properties that make them ideal for CNC machining applications. This section discusses the advantages of aluminum CNC machining:
1) Strength-to-weight ratio
With a density of about one-third that of steel, aluminum is a relatively light metal. Although aluminum is lightweight, it has very high strength. Therefore, this high strength-to-weight ratio makes aluminum an ideal material for CNC machining automotive and aerospace applications.
2) Machinability
Compared to other metals, aluminum alloys are easier to shape and machine. You can cut aluminum easily and quickly using machine tools because aluminum is soft and easily breaks. Aluminum alloys are less expensive and require minimal power for machining.
Excellent machinability of aluminum alloys helps reduce the risk of deformation during machining. Therefore, it ensures higher precision in machining custom aluminum CNC machining parts because CNC machines can easily achieve tight tolerances.
3) Corrosion resistance
Aluminum exhibits natural corrosion resistance under different atmospheric conditions. However, you can anodize aluminum machined parts to enhance these properties. Also, it helps to know that different aluminum grades have different corrosion resistance. Nonetheless, the most widely used CNC machining grades have excellent corrosion resistance.
4) Electrical Conductivity
Pure aluminum has an electrical conductivity of about 37.7 million Siemens/meter at room temperature. Aluminum alloys provide their parts with electrical conductivity, making them suitable for electrical components, even though their conductivity may be lower than pure aluminum. However, if conductivity is not a primary requirement for machined parts, aluminum alloys will not be suitable.
5) Custom Finishing
Aluminum machined parts are compatible with a variety of surface treatments such as chromate conversion coating, anodizing, powder coating, and painting to achieve the custom look preferred by your project.
6) Recyclability
The CNC machining process produces constant chips, which are considered waste because it is a subtractive process. However, aluminum is highly recyclable; therefore, it only takes cost, effort, and minimal energy to recycle it.
Moreover, this property makes aluminum ideal for manufacturers who want to recover costs or reduce material waste. Likewise, the recyclability of aluminum makes it a more environmentally friendly metal to work with.
3.Suitable Aluminum Grades for CNC Machining
Typically, pure aluminum material contains 99% to 99.6% aluminum, with the remainder made up of other alloying elements, including zinc, magnesium, silicon, manganese, and copper. This section discusses common aluminum alloys based on their primary alloying elements:
1) 1000 Series
1xxx aluminum alloys have the highest percentage of pure aluminum, about 99% aluminum by weight. There are no specific alloying elements; most of these alloys are nearly pure aluminum. For example, 1199 aluminum alloy is 99.99% aluminum by weight, making it ideal for making aluminum foil. While these grades of aluminum alloy are the softest, you can harden them to make them stronger with continued deformation.
2) 2000 Series
The primary alloying element for 2xxx series aluminum is copper. These are heat-treatable aluminum alloys made by precipitation hardening and are nearly as hard and strong as steel. This heat treatment process increases the yield strength of these aluminum alloys by heating the aluminum material to float out the precipitates of other metals from the metal.
Aluminum alloys in this category have low corrosion resistance. However, Aluminum 2024 contains manganese and magnesium, which makes it corrosion resistant. Therefore, it is a good choice for CNC machining in aerospace.
3) 3000 Series
The main alloying element of 3xxx series aluminum is manganese. However, since these grades of aluminum cannot be heat treated, you can harden these aluminum alloys to achieve the desired hardness level. For example, 3004 aluminum contains magnesium and it is one of the commonly used aluminum alloys for making beverage cans. Similarly, 3003 is a general-purpose alloy with a wide range of uses.
4) 4000 Series
Silicon is the main alloying element of 4000 series aluminum. The silicon content results in a lower melting point for 4xxx aluminum grades. 4047 aluminum is ideal for use as building sheet and cladding, while 4043 aluminum is an ideal filler rod material for welding 6000 series alloys.
5) 5000 Series
The 5000 series contains magnesium as its main alloying element. These aluminum grades have good corrosion resistance. Therefore, they are well suited for marine or other applications that expose aluminum to extreme elements. However, aluminum 5083 is an alloy commonly used in marine applications.
6) 6000 Series
The 6xxx series contains silicon and magnesium as its main alloying elements. You can easily machine the 6000 series aluminum alloys, which are precipitation hardened. Most of the aluminum alloys in this series, especially 6061, are versatile and have good corrosion resistance and are widely used in structural parts and aerospace.
7) 7000 Series
Zinc, sometimes magnesium, chromium, and copper are the main alloying elements of these aluminum alloys. These aluminum grades reach peak strength after precipitation hardening. The 7xxx grades have typical applications in the aerospace industry due to their high strength.
7075 is a popular grade that has poorer corrosion resistance than other aluminum alloys, although it has superior corrosion resistance than the 2xxx aluminum alloys. This alloy has universal applicability, although it is primarily used in aerospace parts machining.
8) 8000 Series
The 8000 series includes aluminum alloys that do not fall into any of the categories discussed previously. These aluminum alloys may contain a variety of other elements, such as lithium and iron. For example, 8176 aluminum contains 0.1% silicon and 0.6% iron by weight, and its typical applications include wire.
4.Best aluminum grades for CNC machining
While different grades of aluminum are suitable for various CNC machining applications, some exhibit better performance than others. This section discusses the best aluminum alloys for CNC machining
1) 6061 aluminum alloy
This aluminum 6061 is widely used in general manufacturing, construction, consumer products, and aerospace industries due to its versatility and excellent weldability. This medium-strength alloy can be heat treated and has high corrosion resistance. You can process this aluminum alloy using different techniques and it exhibits excellent machinability in the annealed state.
2) 7075 Aluminum Alloy
Aluminum 7075 is one of the strongest aluminum alloys. This high-strength alloy has good fatigue resistance, making it ideal for making parts for high-stress applications. Therefore, 7075 aluminum is a popular choice for aerospace applications. It also has aerospace-grade strength, making it ideal for making complex parts.
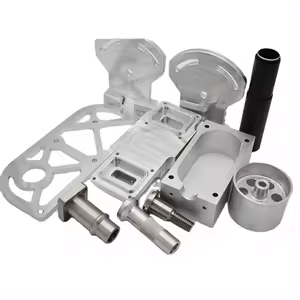
5.Aluminum CNC Machining Cost
The CNC machining cost of aluminum is made up of several main aspects.
- Raw material price
- Machining time
- Labor cost
- Tool wear
- Product complexity
The cost of aluminum has a distinct advantage over CNC machining of other metals, such as steel. The raw material cost of aluminum is generally lower than that of steel, which is reflected in the overall price. Aluminum is softer and is easier and faster to machine—often in 1/2 to 1/4 the time required for steel parts. This efficiency reduces labor costs and speeds up production.
However, the abrasiveness of aluminum can lead to more frequent tool changes, which can increase tool costs. Conversely, steel is more ductile and requires more time and effort to machine, increasing operating costs. Additionally, machining steel generally increases tool wear and energy consumption. Despite these challenges, the longevity and durability of steel may be necessary in certain applications.
6.Common CNC Machining Techniques for Aluminum Alloys
This section discusses the different machining processes applicable to aluminum alloys.
1) CNC Milling
CNC milling is an automated process that typically manufactures aluminum CNC machining parts by rotating a multi-point cutting tool along its axis while the workpiece remains stationary along its axis. The CNC milling cutter gradually removes material from the aluminum workpiece at a controlled speed, which can be done along multiple axes. High tolerances can be achieved when milling aluminum.
2) CNC Drilling
CNC drilling is a common technique for drilling holes in aluminum workpieces. It involves using a multi-point rotating cutting tool of a specific size to move along a straight line perpendicular to the material that needs to be drilled. This process is suitable for machining products that need to be assembled or accommodate screws and bolts.
3) CNC Turning
Aluminum CNC turning involves rotating the workpiece while the single-point cutting tool remains stationary along its axis. The cutting tool or the workpiece undergoes a feed motion relative to each other, depending on the machine that removes the material. The raw material rotates at high speed while the turning center removes material to form the desired shape.
7.Key Challenges in CNC Machining of Aluminum Alloys
Despite the excellent machinability of aluminum, manufacturers and product engineers often encounter frustrations during CNC machining. This section discusses some of these challenges and possible solutions:
1) Ductility of aluminum
The high ductility of aluminum can lead to problems such as poor surface finish, burrs, and chip formation during aluminum CNC machining. Built-up edge often occurs because the material sticks to the cutting tool. As a result, this leads to a shortened tool life.
Solution: You must use the right cutting tools designed specifically for machining aluminum, including carbide or polycrystalline diamond (PCD) tools. You can also use cutting fluid to effectively dissipate heat and reduce friction to ensure excellent surface finish. You may need to fix the aluminum workpiece to minimize deflection and chatter during machining.
2) Thermal Issues During Machining
Aluminum alloys have high thermal conductivity and dissipate heat quickly during CNC machining, which can easily cause problems such as thermal deformation of the workpiece, reduced machining accuracy, and tool wear.
Solution: Use a high-pressure coolant system in aluminum CNC machining to mitigate overheating. Similarly, you can reduce cutting speeds to ensure less heat is generated to prevent thermal expansion of the workpiece.
3) Wear of machine tools
Some aluminum alloys contain silicon, which can make aluminum machining rough. Therefore, you may experience rapid tool wear and frequent tool changes during aluminum CNC machining.
Solution: It is recommended to use high-quality tools with extremely high hardness and toughness to reduce frequent tool changes while increasing productivity. In addition, coatings such as TiAlN (titanium aluminum nitride) or TiCN (titanium carbonitride) ensure longer tool life in high-temperature operations.
More importantly, use tools with sharp cutting edges and correct rake angles to reduce friction. You can also frequently check cutting tools for signs of wear and replace worn tools immediately to prevent damage to the workpiece.
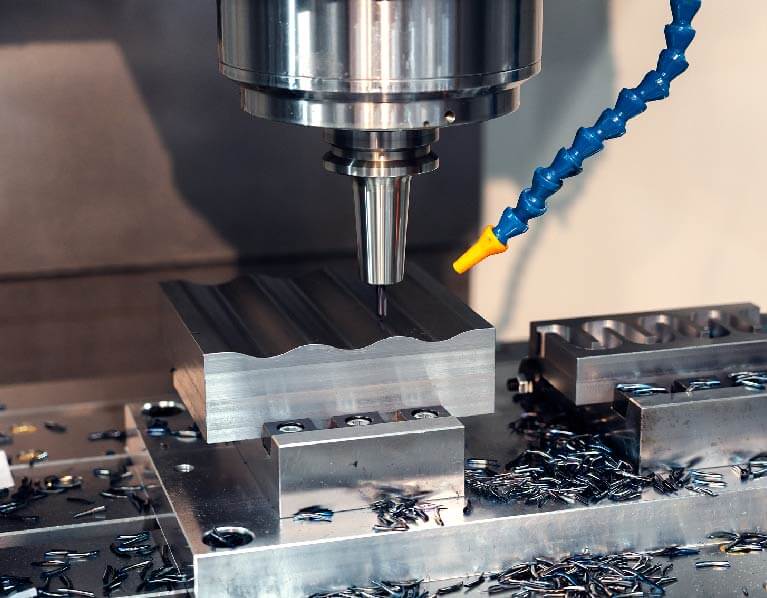
8.Application of aluminum alloy CNC machining parts
Aluminum CNC machining parts have excellent quality and are very suitable for different industries and uses. Here are some typical applications of these parts:
1) Aerospace Innovation
Aluminum alloy CNC parts are ideal for structural parts in the aerospace industry, such as engine components, fuselage components, and landing gear, because aluminum alloys have good mechanical properties. Aluminum has an excellent strength-to-weight ratio and low weight, making it a widely used material for reducing the weight of aircraft.
Aluminum CNC machining helps meet the strict quality standards of the aerospace industry for precision and reliability. Aluminum CNC machining parts play a key role in the production of aerospace structures such as wing panels and fuselage sections.
2) Automotive Engineering
The automotive industry has benefited greatly from the excellent properties of aluminum in manufacturing a variety of automotive parts and systems. Manufacturers and engineers in the automotive industry use aluminum CNC machining parts in automotive engineering, especially engine components, suspension systems, transmission housings, and electric vehicle components.
The light weight, durability, and strength of aluminum alloys make aluminum CNC machining parts an ideal choice for reducing the overall weight of vehicles and ensuring vehicle durability.
3) Consumer Electronics
Aluminum CNC machining parts are widely used in the production of a wide range of consumer electronics products, including laptops, audio devices, smartphones and tablets, and camera parts. Aluminum is suitable for manufacturing the housings of laptops, smartphones, and tablets because it has a sleek and lightweight design that protects the internal components of the electronic device.
In addition, high-end audio devices such as amplifiers, headphones, and speaker housings are often equipped with aluminum CNC machining parts. Aluminum is often used in this application because it can dampen vibrations. In addition, aluminum CNC machining parts have the required strength and can dissipate heat in devices such as cameras.
9.Conclusion
Aluminum CNC machining is a popular product manufacturing process due to the unparalleled potential of aluminum alloys. Aluminum alloys further improve the characteristics and properties of aluminum, making CNC aluminum machining an ideal manufacturing process.
This guide discusses the typical aluminum grades for CNC machining. However, it is essential to know all about CNC aluminum machining and determine the ideal aluminum alloy for your project to fully utilize the potential of aluminum CNC machining.