The History of CNC Machining: From Manual to Automated Processes
Currently, CNC machining is a popular manufacturing process with a wide range of industrial applications. However, how much do you know about the history of CNC? Have you ever wondered about the history of CNC machines? How do you think people would view machines that made products/tools with little to no guidance centuries ago?
Today’s CNC machining has improved computerized features due to continuous development. However, it is much more than that. In this article, we will answer all of the above questions by taking a deep dive into the history of computer numerical control. This will be explained from the perspective of its origins and its development over the years.
1.What is CNC machining?
CNC machining is a manufacturing process in which a computer uses programming codes to control a machine to make a product. CNC (Computer Numerical Control) machining is a subtractive manufacturing process. This means that a computer program controls these tools (such as drills, milling machines, and lathes) to continuously cut away at the workpiece. This process continues until the desired product is formed.
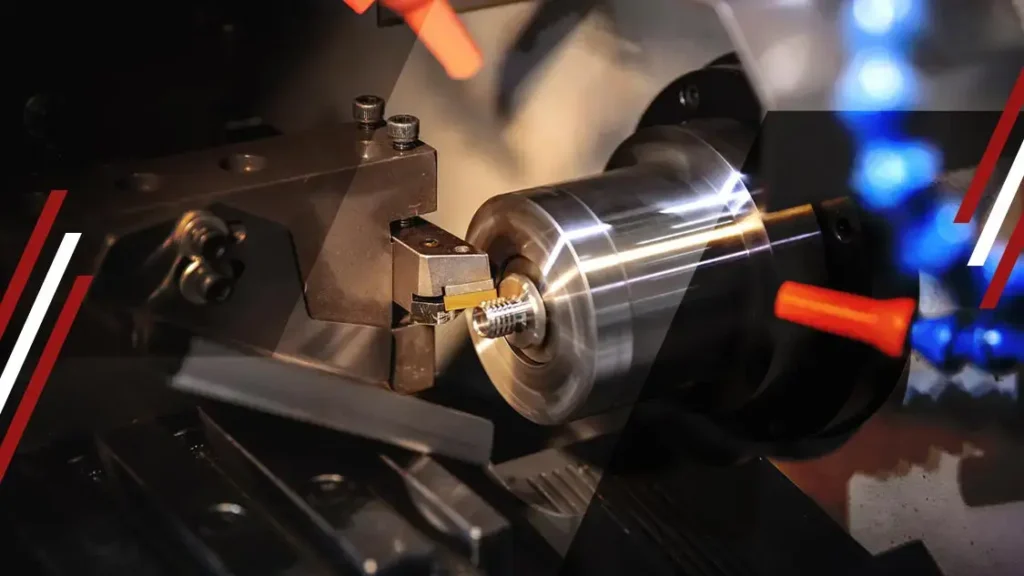
2.Advantages of using CNC machining
CNC machining has a wide range of industrial applications. For example, industries such as aerospace, medical, and consumer electronics rely on its advantages. Here are the advantages of CNC machining.
1) CNC machining is a high-precision process
Many industries require tools that are made using high-precision manufacturing processes. The aviation industry is the top industry that is most notable for this requirement. Since the aviation industry is about human lives, it is unwise to use machines made using low-quality and low-precision manufacturing processes.
2) CNC machining produces parts accurately
Another advantage of CNC machining is its accuracy. Its programming code and operator control allow it to produce parts that are exactly described in the CAD file. Therefore, you don’t need to worry about whether there are many parts that need to fit into a larger assembly. They will fit seamlessly with each other.
3) Material selection
This process has a valuable advantage over other manufacturing processes such as 3D printing. This is because it supports a wide range of materials. With 3D printing and other processes, you have a limited choice of part material types.
The only rule for choosing a material for machining is its compatibility with the manufacturing process. Therefore, you need to consider the following factors:
- Heat resistance.
- Resistance to pressure.
- Hardness.
- Tightening.
- Design tolerances.
Depending on whether you have a CNC machine, you can check the supported materials before you start machining. For example:
- Aluminum.
- Brass.
- Stainless steel.
- Steel.
- Plastic.
3.History of CNC
If you look back at the history of CNC machines, you will find that CNC machining did not start as many people think. Currently, wherever we mention or see the process, we think of it as a computerized process. However, to be precise, CNC machining has only been computerized recently. We will tell you about the history of the process, the first CNC machine, and its evolution over time.
1) The First CNC Machine
The first CNC machine was invented in 1949 by James Parsons. Parsons was a computer pioneer who worked on an Air Force research project. The research was on how to produce helicopter blades and better aircraft skins.
Parsons was able to calculate the coordinates of a helicopter airfoil using an IBM 602A multiplier. He then entered the data into a punch card and used it in a Swiss coordinate drilling machine. This information led to the manufacture of many helicopter blades and aircraft skins. According to the accepted history of CNC, this is considered the first CNC machine. Parsons later received the Joseph Maria Jacquard Memorial Award for his work.
2) Development of CNC Technology
Before the first CNC machine, some machines could be instructed to make other tools. This was called numerical control (NC). You should notice the absence of computerization (C).
Parsons later developed the first CNC machine. With this development, an evolution occurred. Here is a timeline of the evolution that occurred in the history of CNC machining.
1.1952 – 1958
As the Cold War intensified, the manufacturing of many machines and weapons required increased efficiency and productivity. Therefore, in 1952, Richard Kegg worked with MIT to build the first CNC milling machine, the Cincinnati Milacron Hydrotel. Richard Kegg later patented a motor control device for positioning machine tools in 1958.
2.1967 – 1972
CNC machining is gaining more and more acceptance around the world. This is thanks to the development of computer-aided design (CAD) and computer-aided machining (CAM) in 1972. The integration of CAD and CAM into CNC machining has driven the large-scale development of the process. However, the two were not considered a standard part of the manufacturing process.
3.1976 -1989
In 1976, 3D computer-aided design and computer-aided machining were incorporated into CNC machining. In 1989, machines controlled by CAD and CAM software became the industrial standard for CNC machines.
4.Today’s CNC Industry
The evolution of CNC machines is quite unique. From a simple machine controlled with punch cards to a machine driven by software is a mystery. Due to this evolution, CNC machining is faster, more precise, and more accurate than NC and the first CNC machines.
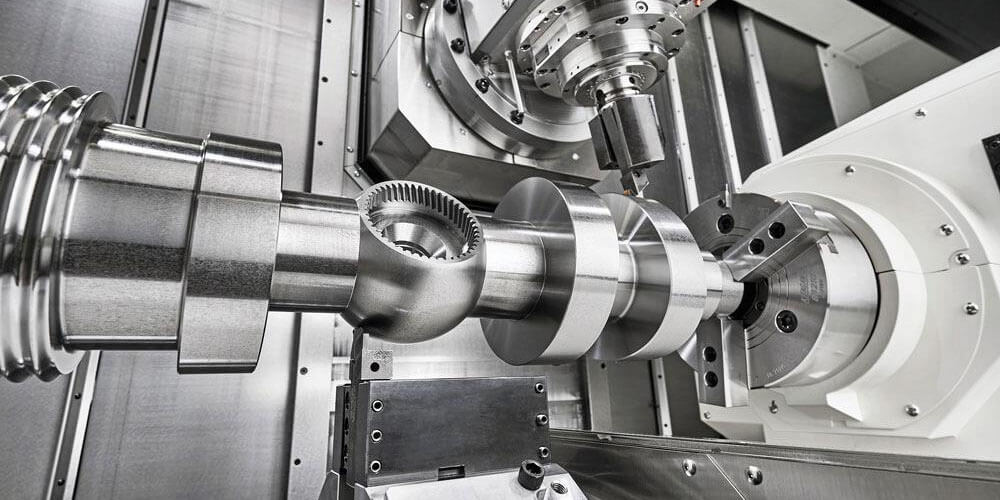
5.CNC Machining Applications
Over time, the process has developed into a widely recognized machining method around the world. Due to its advantages, many companies incorporate it into their manufacturing processes. The process is not only applicable to the industrial sector. It is equally important at the manufacturing level, which determines its use in industry. Here are the applications and manufacturing capabilities of the process in the top industries.
1) Industrial Applications
- Automotive
The automotive industry is a major user of CNC machining. They rely on the manufacturing process both for prototyping and production.
2. Consumer Electronics
While it may be surprising, the consumer electronics industry also uses CNC machining. Companies such as Apple use the process in production. For example, the chassis of the Apple MacBook is made from aluminum that has gone through the process.
3. Aerospace/Military
These two industrial sectors are major users of CNC machining. This is because of its high precision and accuracy. The process is also ideal because it can produce replacement and upgraded versions of any part on demand.
2) Manufacturing Applications
1. Prototyping
CNC machining is a good process for making prototypes because it is autonomous. Once you have a CAD file, you can send it to the CNC machine and the manufacturing will be completed in a very short time. These characteristics make it ideal for making prototypes.
2. Production
With its high precision and accuracy, CNC machining is ideal for making high-quality parts. Its wide range of material support has also increased its usage in part manufacturing.
Therefore, companies that use it to make prototypes also use it to make usable final parts.
3. Tools
CNC machining is a gem in direct manufacturing processes, providing a huge help. However, it can also be used in indirect manufacturing processes, providing assistance for many processes such as injection molding.
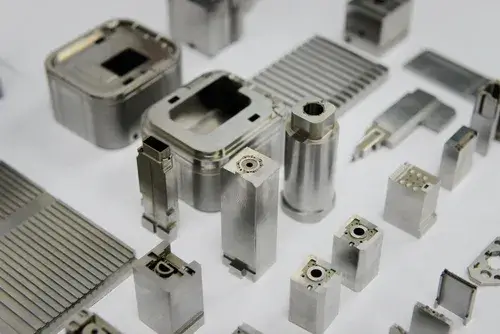
6.Conclusion
The history of CNC machining is very unique. It has evolved from the first CNC machines that required punch cards to software-based machines that require little to no instruction. CNC machining is a top manufacturing process used by many industries.