Introduction to common sheet metal welding process types
Sheet metal welding is a vital technology in modern industrial manufacturing. Different sheet metal welding processes have their own characteristics and are suitable for specific scenarios. Let’s take a look at six important sheet metal welding processes.
1.MIG welding
MIG welding (gas metal arc welding) is a widely recognized technology. This method creates a fuse pool by using a solid wire electrode in the welding instrument. The wire is a filler material that facilitates the connection of metal parts. A shielding gas layer is also incorporated into MIG welding equipment to protect the molten stream from contamination by the surrounding atmosphere.
MIG welding is commonly used in many industries, including the automotive and home improvement industries. The main reason for this is a combination of cost-effectiveness and efficiency. The technology works on the most common sheet metal materials including stainless steel and aluminum. It produces high-quality welds, is relatively inexpensive, and does not require sophisticated equipment.
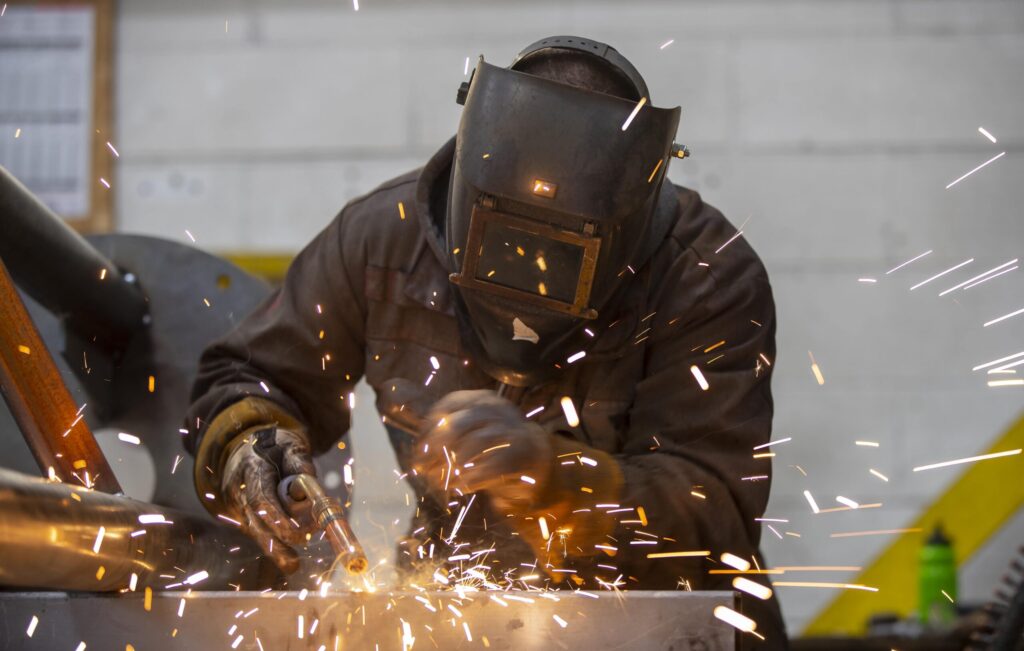
TIG welding
This welding technique works on the principle of arc welding, but uses electric current to pass through a non-consumable tungsten electrode to perform the welding operation. It uses an inert shielding gas to protect the electrode and protect the weld from atmospheric contamination. Helium and argon are the most commonly used shielding gases. TIG welding is most efficient when processing non-ferrous metals such as titanium, nickel, magnesium and aluminum. It is one of the most common methods for manufacturing spurs, motorcycles and door frames. TIG’s ability to handle non-ferrous metals makes it an excellent choice for flight-related industries, including aerospace and aviation.
TIG welding allows for better control of the process and produces stronger welds than alternative technologies. However, it also requires a higher level of welder proficiency and can sometimes be more time consuming.
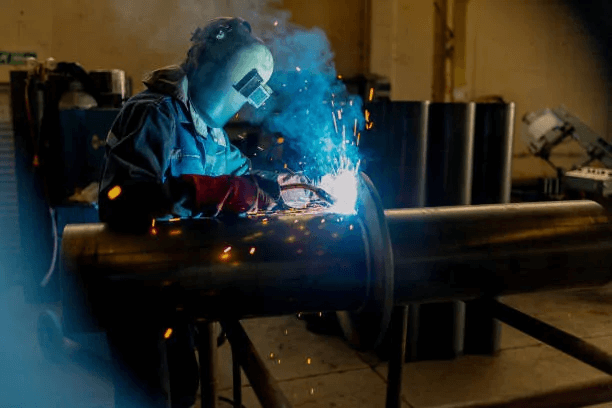
Laser/electron beam welding
Laser and electron beam welding are probably the most expensive processes, and their applications are very limited. Lasers or electron beams were initially used to generate the heat required for the welding process. However, the main difference between the two is that their operation requires the use of specialized and complex equipment.
These methods are very precise, especially in laser welding. This makes them ideal for manufacturing metal parts that require a high degree of complexity. Additionally, they can process more durable metal varieties, including carbon steel, stainless steel and titanium, without affecting the overall aesthetics of the weld. Electron beams and lasers can also be applied to more common substances, including thermoplastics and aluminum. However, this may not be the most economical approach.
Stick welding
Stick welding uses a coated electrode as an electrode and does not use shielding gas. By applying flux on the electrode rod, it decomposes under the action of welding heat to form a protective layer to protect the weld. It is an alternative technology to laser welding. Although it is not precise and the weld is not beautiful, it is efficient and economical. Industries such as shipbuilding, construction and steel manufacturing can benefit from its portability.
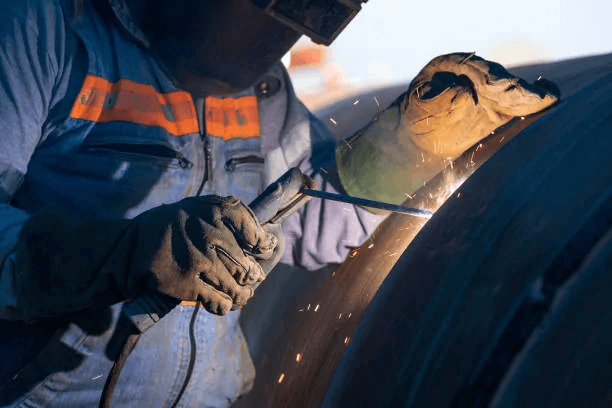
Plasma arc welding
This welding process is comparable to the TIG welding mentioned above in that the welding instrument also contains a tungsten electrode. However, plasma arc welding uses a smaller arc size and allows the electrode to contact the body of the welding tool. By creating a plasma through pressurized gas, various metal components can be melted together. Plasma arc welding requires no filler material and produces high-quality welds with minimal post-weld cleanup. Furthermore, it is a relatively fast method that lacks considerable strength but has extraordinary accuracy. Therefore, it is common in the aerospace and marine industries.
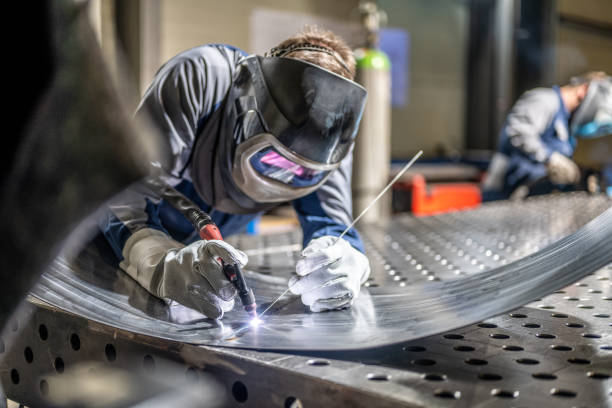
Gas welding
Another possible method of joining molten sheet metal sections is to use gaseous fuel, oxygen, or oxyacetylene to ignite the metal and weld them together. This is one of the more established programs on the list and a fairly common one in the industry. Due to its adaptability and effectiveness, it remains one of the most widely used methods in the metalworking industry. Metal workers use this method on ventilation shafts, ducts, ducts, air conditioning systems, and more. Gas welding is suitable for ferrous and non-ferrous metals, can be operated without electricity, is portable, affordable, and does not require much expertise to operate.