Best Practices Guide to Squeeze Casting: Definition and Application
What is squeeze casting?
Squeeze casting is a hybrid process, i.e. it combines casting and forging, suitable for manufacturing metal parts with low porosity and high mechanical properties. It is an improvement on the traditional die-casting process and is compatible with many metals, the most common of which are aluminum, copper, zinc and magnesium. In addition, it is widely popular in the auto parts manufacturing industry because many auto parts are extrusion cast.
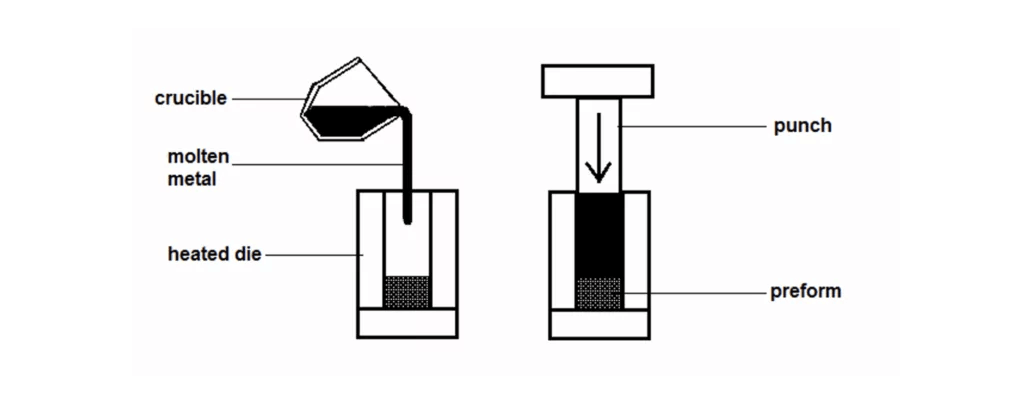
Commonly used materials for extrusion die casting
Extrusion die casting is compatible with ferrous and non-ferrous materials. However, the most commonly used materials for this process are:
1.Aluminum material
Aluminum alloys such as AL6063 and AL6061 are the most commonly used alloys in extrusion die casting. They are strong, lightweight, corrosion-resistant and versatile. Therefore, aluminum extrusion casting is popular in industries such as automotive and aerospace. However, successful aluminum extrusion casting depends on selecting the right alloy and controlling parameters such as pressure and temperature.
2.Copper
Copper alloys such as brass and bronze are common squeeze cast alloys known for their strength, durability, wear resistance, and electrical conductivity. In addition, they are highly castable and can be shaped under pressure until solidified. Squeeze cast copper parts are common in the marine parts manufacturing industry. However, their high cost and characteristics such as easy corrosion and low high-temperature strength limit their use in certain industries.
3.Magnesium
Magnesium alloy is another material that is highly castable and therefore useful for squeeze casting, but is popular for its light weight and high strength-to-weight ratio. Magnesium alloys are an attractive material choice for industries that require lightweight yet strong components, but their flammability and susceptibility to oxidation require precise temperature control.
4.Zinc
Zinc alloys have excellent flow properties, making them compatible with squeeze casting and suitable for manufacturing parts with complex geometries. They are known for their low melting point, requiring less heat than most metals. Although common in squeeze casting, zinc squeeze casting is only suitable for use at lower operating temperatures.
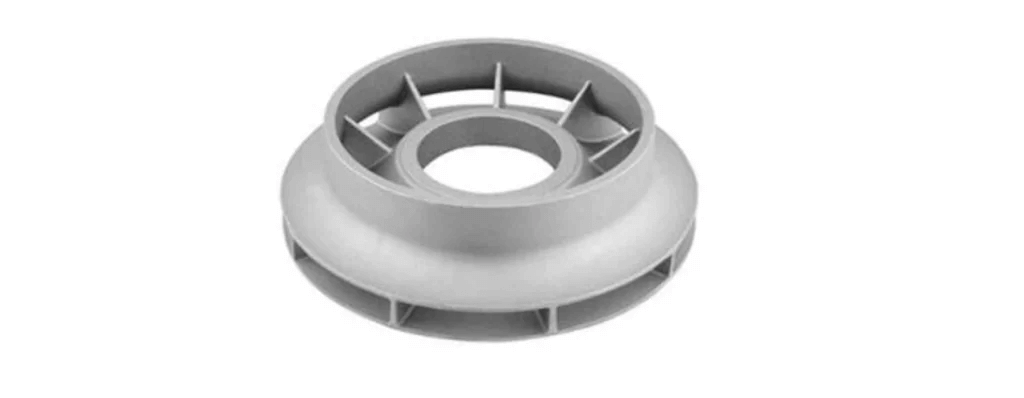
Applications of squeeze casting
Squeeze die casting is suitable for many industries due to its unique process, advantages and casting properties.
1.Automobile industry
A common application of the casting process is the automotive parts industry, where it is suitable for manufacturing high-quality automotive components such as brackets, nodes, chassis and frames. A common example is Porsche, which uses the process to manufacture engine parts.
2.Military industry
Extrusion die casting is also suitable for manufacturing military weapons and heavy machinery. Utilizing materials such as magnesium alloys, the squeeze casting process can produce high-quality parts such as blockbusters, bevel gears, pipes, blades and discs.
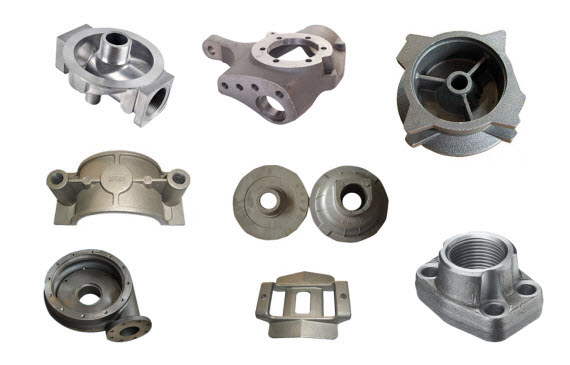
3.Marine parts
The casting process is also compatible with materials such as aluminum, which can be used to make small turbine blades and ship propellers. Its compatibility with heat treatment methods such as annealing also makes it common here, as this can be used to improve the operation of parts in marine environments.
Squeeze casting and high pressure die casting
Squeeze casting is often confused with high pressure die casting. Although both use pressure in casting and the materials are compatible, the casting process is different. HPDC injects molten metal at high speed and high pressure and maintains pressure until solidification. It is suitable for manufacturing thin-walled parts and produces smooth and high-quality castings. Squeeze die casting is a mixture of casting and forging, with slow metal speed (about 0.5m/s), long solidification time, long cycle, and fewer bubbles in the mold cavity, reducing the porosity of the part.
Squeeze casting combines casting and forging techniques, including slowly pouring liquid metal into a preheated mold, and then closing the upper mold on it to form a mold cavity and generate pressure to reduce air bubbles in the mold cavity. The extrusion die-casting process has the advantages of low porosity and high density, and is suitable for manufacturing some industrial parts. While this article introduces you to how the process works so that you can make an informed decision, a cost-effective and quality-focused casting project can be achieved by outsourcing to a reputable custom casting service.