Introduction to overmolding process types
Several types of overmolding processes include insert molding, injection molding, overmolding, and polyurethane casting. Let’s discuss each type in brief detail;
1.Insert molding
Insert molding, as the name suggests, involves inserting a metal part into a part being molded in a single injection. Therefore, insert molding, also known as a single-shot injection molding process, effectively eliminates post-processing requirements, provides fast production cycles, and provides an unlimited number of design configurations for high-volume composite part or product manufacturing. In addition to its adaptability, insert molding is often suitable for time-sensitive production. Because it provides a quick way to turn a design into a practical one in a short time.
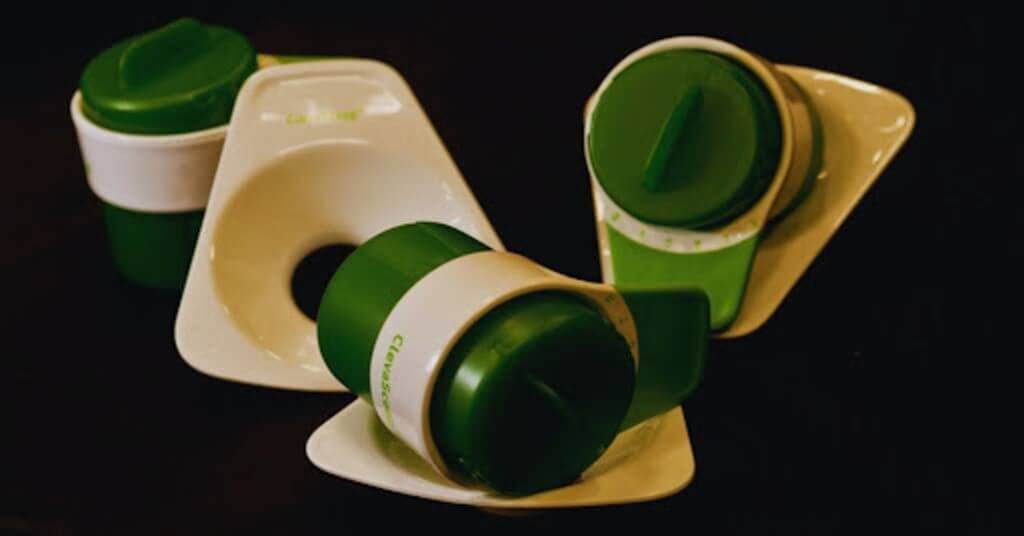
2.Two injection molding
Injection molding is a traditional plastic overmolding technology, also commonly referred to as dual overmolding, 2k overmolding, or double overmolding. As the name suggests, it involves two separate injection molding units located in different locations. Therefore, dual injection molding is relatively complex, expensive and difficult to handle compared to other overmolding technologies. In addition, the mold change rate in its operation is quite high. This technology typically facilitates high-volume part production, with production runs of 10 to 10,000 units.
Products produced by the dual injection molding process typically create a line between two molded parts, and the technology is often used for parts that require different color products and dual strength or hardness properties. However, tooling and material selection often require specialized knowledge to handle part manufacturing projects.
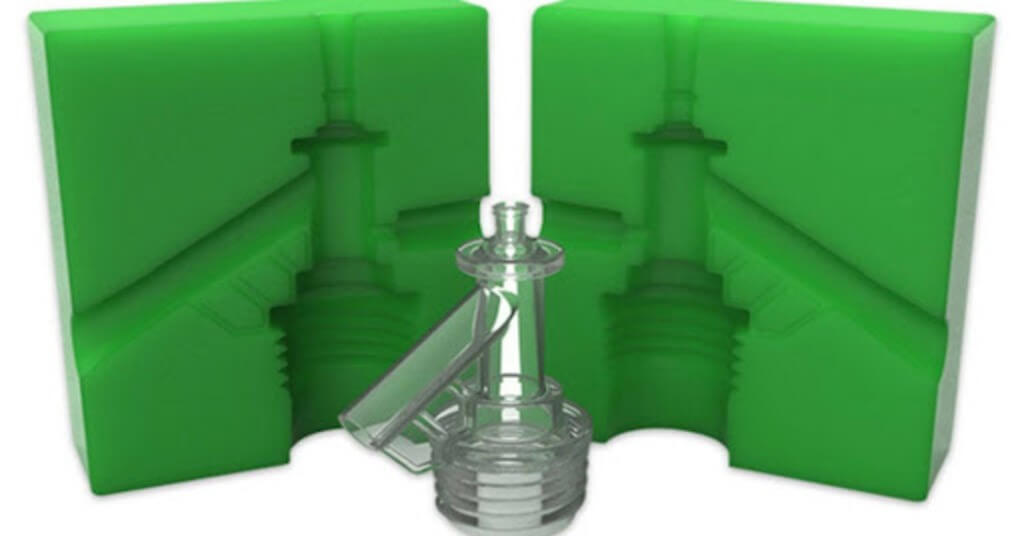
3.Polyurethane molding
Polyurethane molding also has names such as polyurethane casting, vacuum casting and polyurethane casting. Polyurethane casting resin. Typically, silicone molds are used for polyurethane casting, which is used to create high-strength rigid, rubber-like or flexible parts and finely oriented product manufacturing.
Of the technologies mentioned above, polyurethane molding is often practical and economical for manufacturers to use it in a small range of products. During this process, liquid polyurethane is poured into a silicone mold. Through the heating and curing reaction, the desired part is made and slightly demolded as it cools. Typically, silicon molds are made using techniques such as 3D printing and CNC machining. Limited cycle times and the complexity of mold design limit its use to some extent. Nonetheless, polyurethane casting is widely used to manufacture structural devices and develop functional and rapid prototypes.