A Comprehensive Guide to Small Batch CNC Machining Aluminum
CNC machining aluminum parts are becoming an excellent choice for many industries. As one of the most popular materials, aluminum has excellent mechanical properties. In terms of processing materials, aluminum machined parts are the most economical because aluminum machined parts can be used for CNC processing in a shorter time compared to other metals. Aluminum machined products also have increased strength, corrosion resistance, and rust resistance.
In addition, aluminum machined parts are chemically resistant, conductive, ductile, and have high strength. Today, CNC machined aluminum parts are widely used in automotive, aerospace, military, medical, and industrial engineering. And product design is developing rapidly, and product developers are shifting their attention from mass production to small-batch manufacturing.
1.CNC Machining Aluminum Services
- Precision CNC Milling: A variety of milling machines, including 3-axis and 5-axis, are available, which helps produce precision machined CNC parts.
- Turning: Turning machines are also equipped in-house. In addition, other machining operations such as knurling, drilling, EDM, etc. are also provided.
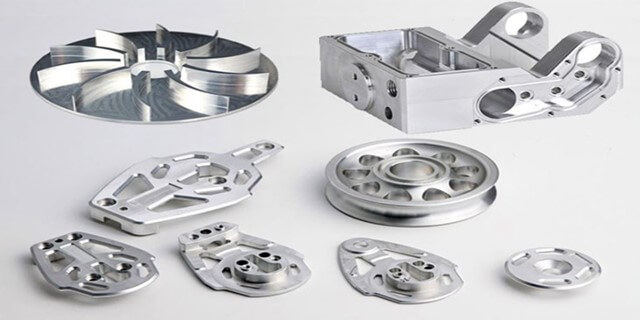
2.Advantages of CNC machining aluminum in small batches
- No mold investment required: Die casting molds usually require a lot of investment. With CNC machining, a lot of startup costs can be saved, and financial risks can also be reduced in the end.
- Short delivery time: It usually takes at least 30 days to build a mold, but CNC machining helps to shorten the timeline to market, and can also help customers seize the market opportunity.
- Higher precision: CNC machining has better tolerances than cast parts. If you need precision parts, CNC machining will be more suitable.
- Better surface finish: Visual parts can usually be made by CNC machining because the surface is really great even without any post-finish.
- More post-processing can be provided: With the help of CNC machined aluminum parts, almost any type of secondary treatment can be used, whether anodizing, powder coating or electronic spraying, chromate.
3.Post-processing of aluminum
- Anodizing: This is an electrolytic passivation process used to increase the thickness of the natural oxide layer on the surface of metal parts, and the parts can be anodized in any color according to requirements. In addition to AL7075, AL6061 has a better anodizing effect.
- Powder coating: In the presence of an electrostatic field, powder is sprayed onto the surface of the part and then cured at high temperatures to form a protective layer. The biggest difference between powder coating and baked finish is the quality of the finish. Baked paint may flow, appear in brush strokes or spray patterns. Powder coating never flows and always has a uniform and even finish.
- E-coating: With e-coating, the substrate is soaked in a bath that may consist of paint, epoxy, or other aqueous solutions. An electric current is then used to attract particles suspended in the liquid solution and deposit them onto the surface of the substrate. Electrodeposition continues until the desired coating thickness level is reached, which can be controlled by increasing or decreasing the voltage level.
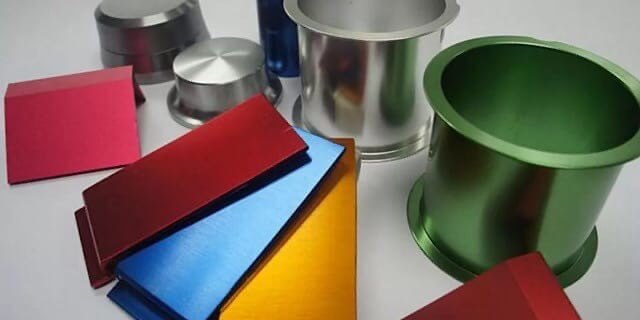
4.Popular CNC machined aluminum parts
- Spline shaft
- Worm gear
- Dials and scales
- EMI shielding housing
- Front panel
- Pins
- Optical reflectors
- Lighting fixtures