6 Important Advantages of High Speed Milling Aluminum in CNC Machining
Milling aluminum is an important processing technology in modern industrial manufacturing. As a widely used alloy, aluminum is light, strong, durable and corrosion-resistant. High-speed milling of aluminum shows many unique advantages.
Importance of High Speed Milling Aluminum
Modern industry has an increasing demand for rapid manufacturing, rapid prototyping and customized parts. Customers expect orders to be completed faster and require more precise components. Aluminum is favored in modern production, and high-speed milling is one of the successful CNC aluminum processing methods. Compared with traditional milling, high-speed milling aluminum has extremely high speeds, which allows machinists to increase cutting feeds, bringing many advantages.
1.Higher efficiency
Increase cutting speeds to three times that of conventional milling of aluminum, and increase feeds by two times (for softer aluminum alloys). The machining feed determines the productivity of the entire milling process, and high-speed machining is much more efficient than conventional milling. The machinability of aluminum allows spindle speeds of 18,000 rpm or more. High material removal rates make milling aluminum processing services extremely valuable in the automotive and aerospace industries. Automotive prototypes require a lot of material removal, and the milling setup should be as simple as possible; the aerospace field has many long and large parts with grooves and thin walls, and aircraft and rockets often use aluminum alloys with aluminum content as high as 80%.
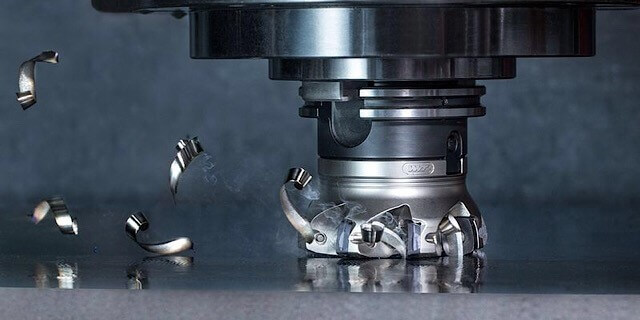
2.Lower cutting temperature
It has been proven that the cutting temperature changes with increasing speed. First, as the speed increases, the temperature also increases. However, as the speed continues to increase, the temperature begins to drop sharply until at some point it no longer changes. Increasing the cutting speed will only reduce the temperature to a small extent. For example, when milling at 300-500 m/min, the temperature may reach 600-800 degrees. However, if the speed is increased to 1200, the temperature drops to less than 200 degrees, and at 1800 m/min the temperature is only 150 degrees. From that point on, faster cutting does not make sense.
Just think about it, only 150-200 degrees! Due to local heat treatment, the material properties of the cutting area do not change, metal grains do not increase, and the cooling requirements are much smaller. I would say this is a good advantage.
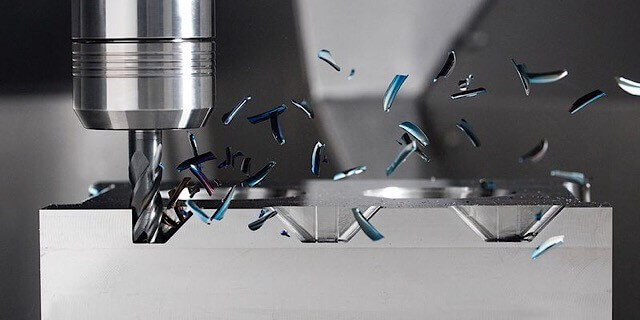
3.Longer Tool Life
It seems paradoxical that the higher the cutting speed, the greater the tool wear. However, when comparing the amount of material removed by high-speed milling aluminum tools with that removed by conventional milling, the difference is obvious.
The reasons why high-speed milling of aluminum is more advantageous are:
First, the cutting temperature is low and the tool material is stronger;
Second, the chip width is small when milling at high speed (the tool rotates faster and cuts thinner chips); In addition, when machining aluminum, the aluminum is soft and tends to stick to the tool cutting edge, reducing sharpness and increasing cutting forces, shortening tool life, which does not happen at high speeds.
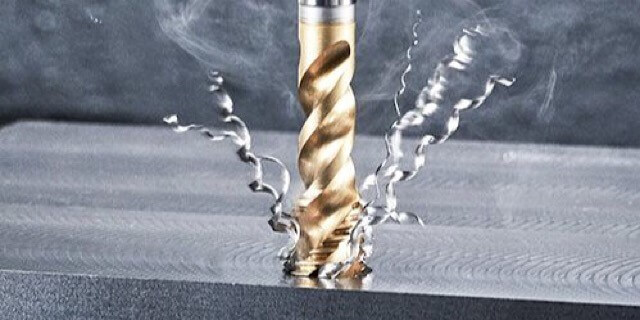
4.Better Precision
We all think that higher feed rates will make the surface finish of aluminum less smooth because the cutting edge of the tool moves farther while the tool can turn and cut off. Generally, this results in wider chips, higher cutting forces, and a poorer surface finish. However, in HSM, despite the high feed rate, the tool speed is high, so the chip is actually thinner than in conventional milling.
5.Constant tool engagement angle
When using an end mill to mill a cavity, making the cavity angle is a problem. When the end mill rotates 90 degrees to form a cavity, the cutting material is doubled, resulting in a local increase in cutting force, which is not conducive to tool life and part accuracy. However, high-speed milling of aluminum has a predetermined tool path generation strategy, including a constant tool engagement angle, the tool machining in a circular trajectory, constant cutting force, unchanged accuracy, and extended tool life.
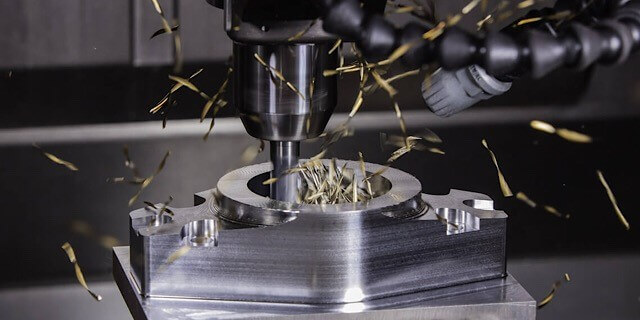
6.Less use of coolant
Some high-speed milling strategies for aluminum machining do not use coolant, requiring little to no cooling of the material and tool at machining at 200 degrees. Some extremely precise operations still use coolant to improve part quality, but the amount used is much less than traditional machining. Some processes use minimum quantity lubrication, applying just enough coolant to form a thin film, reduce friction and provide some cooling.
In summary, high-speed milling aluminum is an innovative production method for making custom parts, aluminum alloy prototypes and small batch production.