A Comprehensive Guide to CNC Machining Costs
In addition to the initial CNC machine cost, there are other factors to consider, such as raw materials and CNC machining wages. However, there are some tips you can implement to significantly reduce your overall costs.
1.Avoid tight tolerances
Deep slots are when extended tool travel is required to create a deep cavity in the workpiece. Using a CNC mill to make deep slots can lead to various problems such as tool breakage, accelerated tool wear, tool chatter, tool deflection, wall chatter, coolant delivery, chip recovery, etc. These issues can lead to more frequent tool changes and workpiece breakage, which greatly affects costs. Therefore, avoiding tight tolerances is a good way to reduce costs.
2.Reduce the use of tight tolerances
This refers to the distance between the actual part and the submitted design. It is usually measured in hundredths or thousandths of an inch. Having a part tolerance that is too tight increases the overall cost due to the complexity and demand of the part. Tight tolerances require slower milling operations. Not only that, but it also requires a higher quality CNC machine. This leads to additional equipment costs and higher labor costs because the operator’s salary increases due to long working hours. Therefore, if the project allows, expand the acceptable machining tolerance range. This can speed up milling and reduce CNC machining costs.
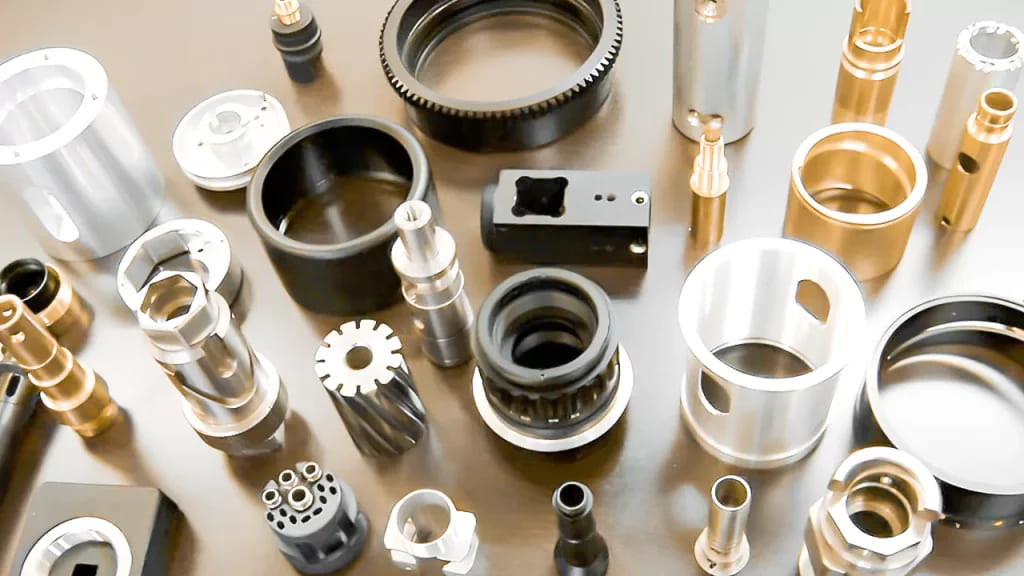
3.Avoid Multiple Finishing
A higher post-processing finish will require the CNC machine to spend a long time machining the product to create a higher quality edge. This increases machine costs, labor costs, and increases wear and tear on the tool. Therefore, it is a good idea to avoid machining the product multiple times. Many products undergo secondary finishing operations, which incur additional finishing costs. Using the final CNC milled product as a finished product is a cheaper option. Other processing and finishing processes include heat treatment, special coatings, anodizing, surface finishing, and special machine operations. However, before undertaking these treatments, their necessity and value should be evaluated.
4.Design Optimization
CAM blueprints lay the foundation for the finished product design. The CAM programming blueprint is then converted to a CAD design, and the program file uploaded to the machine provides the instructions for how to cut the part. Optimizing the design will allow the machine to take the shortest route and cut the least amount of material required to manufacture the final product. This makes better use of time and raw materials.
Inaccurate and incomplete CAD drawings can ultimately be costly in part production. This is because incorrect information on the model may result in the part being made twice to get exactly what you want because your drawings did not communicate this effectively in the first place. Consulting an experienced machinist or engineer during the design phase may increase the initial cost of the project, but it will save more in the long run. This is especially true for high-volume production. It is recommended to invest more in design process planning to save long-term CNC machining costs.
5.Limit thread length
Some manufacturers tend to use longer threads when milling screws and bolts to increase strength. But in many cases, the extra length is unnecessary and a shorter thread is sufficient. The longer the thread, the longer the CNC machining process, the higher the material cost, and the more wasteful the resources, without any additional benefits. Therefore, limit the thread length to the range required to achieve optimal strength.
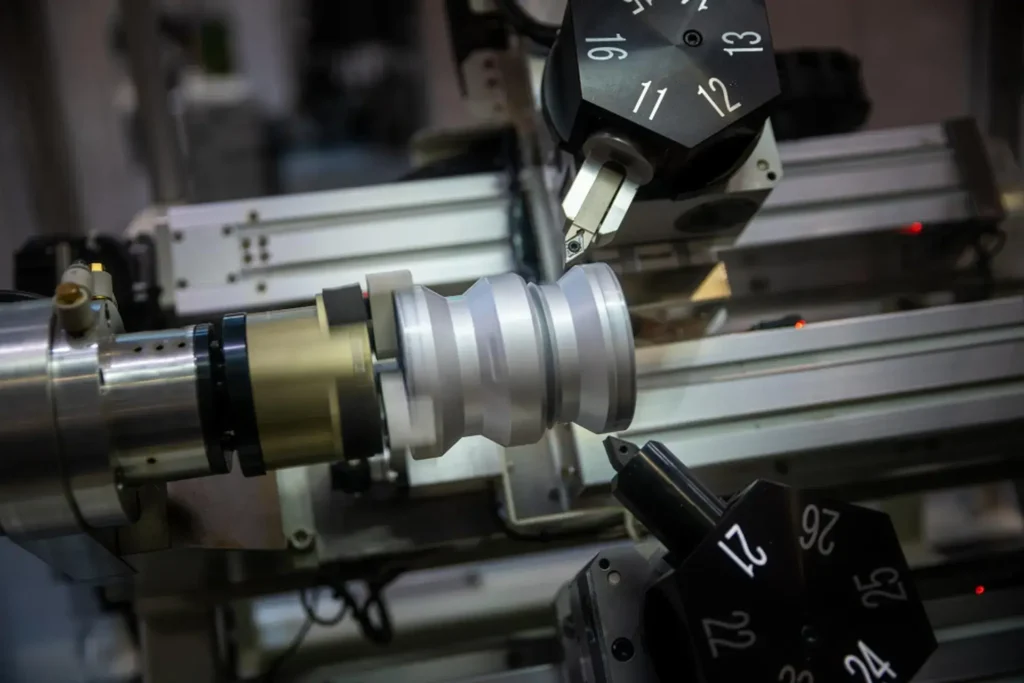
6.Reduce design complexity
High design complexity leads to high design costs and high CNC machining costs. In most cases, complex designs require CNC milling machines with more axes, which can double or triple the total cost. Most complex designs can be broken down into two or several simpler designs that are then milled by a three-axis CNC machine. Assembling these simple designs can create a complex product. By doing this, you can significantly reduce your CNC machining costs.
7.Increase Production Volume
One of the best and easiest ways to reduce CNC machining costs is to increase production volume. When production volume increases, the fixed costs of the process are spread over a large number of CNC machined parts. This can significantly reduce the manufacturing cost of each part. One major benefit that comes with mass production is that the design costs of the parts that are manufactured by the CNC machine become lower. One design blueprint can be used to produce 100, 1000, or 10,000 parts. This can reduce the machining cost of each product.
8.Eliminate Sharp Edges
Sharp edges and 90-degree corners are more time-consuming for a CNC router. This is because the CNC router will go to the edge, stop, turn 90 degrees, and start again. A better way to utilize the CNC machine time is to use fillets and rounded corners. With fillets, the machine can create edges without stopping.
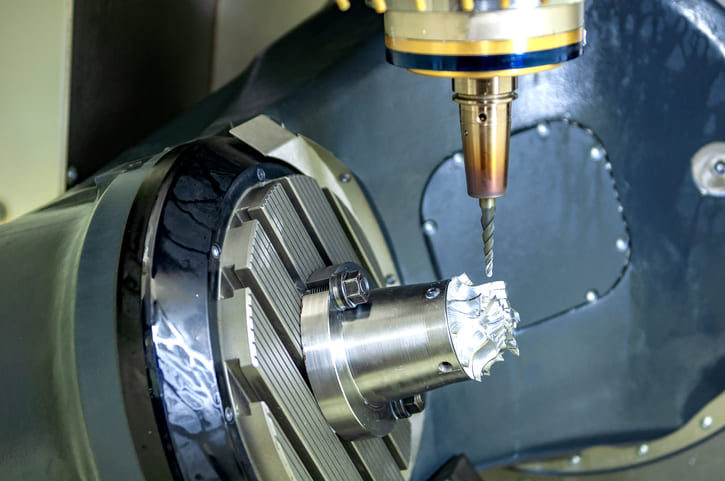
9.Avoid Thin Walls
In most cases, it is best to avoid milling thin walls because they require extra care during CNC machining. Thin walls are fragile and can break due to the force or vibration of the CNC lathe. Therefore, in order to mill thin walls, the CNC machine must cut slowly, which increases time and cost. Even with great care, thin walls have the potential to break, resulting in higher scrap rates. Replacing thin walls with thicker ones may slightly increase material costs, but doing so will significantly reduce CNC machining costs.
10.Use Cheaper Materials
It is recommended to adopt cheaper plastic parts in production whenever possible. Plastics such as Delrin provide sufficient strength in most cases, providing the best value for money.
11.Outsource to a Trusted Manufacturer
When it comes to CNC machining companies, there are many options. However, not every machine shop is the same. A good machine shop is not necessarily the cheapest, but it will provide you with the best value for money and results. Many machine shops offer a lower cost per piece for milling, but make up for it by reducing the quality of the operation. So, while they sound like a good deal at first glance, you may regret it when you receive the parts and find that their quality is unacceptable. To address the question of price vs. quality, find a trusted manufacturer that can provide the quality and price you need.