Comprehensive Guide to Aircraft Drum Shaft Parts
The high-pressure turbine is one of the key components of an aero-engine. The high-pressure turbine drum shaft connects the high-pressure turbine and the high-pressure compressor, and is the main component for transmitting engine torque. The connecting position of the drum shaft in the aero-engine is shown in Figure.
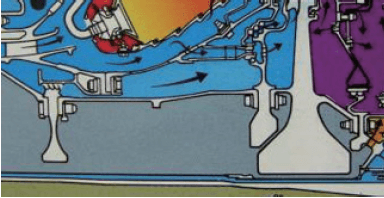
1.Material properties
The material of the high-pressure turbine drum shaft is Inconel 718 (GH4169) alloy, which is an aging precipitation-strengthened nickel-based superalloy. As a difficult-to-machine material, Inconel 718 alloy has the characteristics of poor thermal conductivity, severe work hardening, and easy sticking to the tool.
2.Structural features of parts
The front and rear ends of the high-pressure turbine drum shaft have mounting edges, which is a typical “lace” structure. At the same time, along the circumferential direction, a circle of bolt holes is distributed around the lace, which are respectively connected with the sealing plate of the high-pressure compressor and the sealing plate of the high-pressure turbine through short bolts.
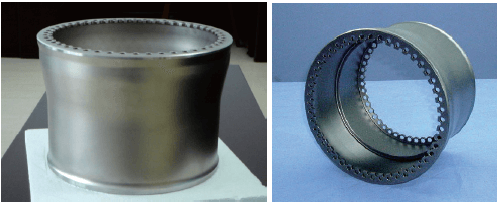
3.Processing methods
The main processing technology of drum shaft parts is turning, drilling and milling “lace”, and the special technology mainly includes fluorescent inspection, shot peening and static balancing.
4.Turning process
The cutting speed is 200m/min, the feed rate is 0.25mm/r, the cutting depth is 2mm, and the tool feed adopts the alternating oblique feed and linear feed. Because it is a typical weak rigidity structure, the solution of wrapping the rubber rope sleeve on the outside of the part can increase the cantilever stiffness of the part, reduce “resonance”, eliminate the vibration problem of the turning tool, and finally the surface roughness and wall thickness change meet the technical requirements. The processing effect after increasing the cantilever stiffness is shown in the figure.
In terms of the clamping method for turning machining, try to use the self-centering chuck for clamping and positioning. Because the self-centering chuck has a self-centering function, the clamping, positioning and alignment can be realized quickly after the parts are clamped, which can save Unnecessary auxiliary preparation time effectively improves processing efficiency.
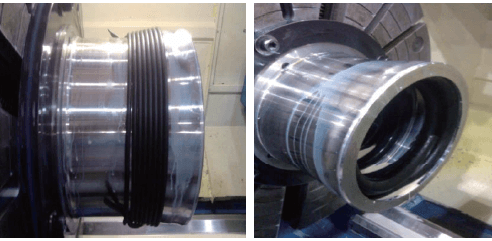
5.Milling process
The milling of drum shaft parts is mainly front and rear end “lace” milling. The technical requirements for the size of the flange surface “lace” . 48 semicircular “laces” of R6.35mm are distributed along the circumferential direction of the flange end face. Using φ11.8mm carbide coated milling cutter.In milling, the application of coated tools and the optimisation of milling processing parameters have effectively reduced tool costs and improved the overall machining efficiency of the parts.
6.What is finishing?
Finishing, or surface finishing, also called surface treatment in some ways, is the final step in parts manufacturing.
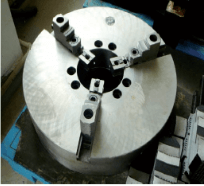
7.why do we need it?
For sustainability! With finishing, parts can easily last 2 or 3 decades and even more, but without it they probably become junk by corrosion in 2 or 3 years.It works well against corrosion! And Xavier provides comprehensive finishing options: chemical conversion coating like Alodine, Surtec etc., oxidizing, anodizing, hard-anodizing, electroplating, galvanizing, powder coating, liquid painting etc., for better appearance and performance! Beautiful, anti-corrosion, low friction, high hardness, electrical resistance, wear resistance, cleanable surface.